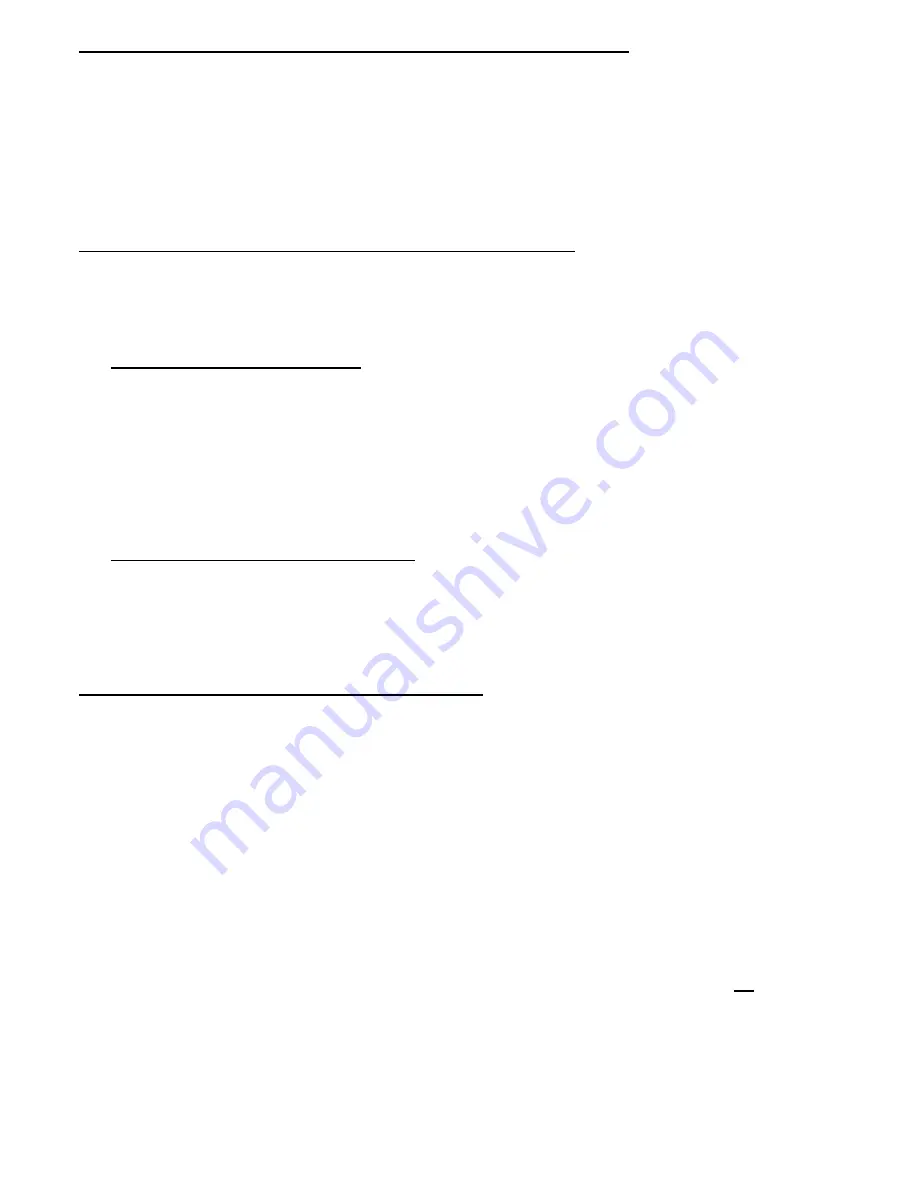
- 4 -
1.2.3 DENYING ACCESS TO THE EDITOR MODE VIA PLCI
Machine parameter "P627(7)" indicates whether this feature is available or not.
P627(7) = 0This feature
is not
available.
P627(7) = 1This feature
is
available.
When using this feature, access to the editor mode at the CNC depends on the status of PLCI output O26, as well as
on the current conditions (protected memory, number of the program to be locked).
O26 = 0
Free access to the editor mode (it is protected by current conditions).
O26 = 1
Denied access to the editor mode.
1.2.4 SPINDLE CONTROLLED VIA CNC OR VIA PLCI
From this version on, the spindle analog output may be set either by the CNC or by the PLCI. Machine parameter "P627(7)"
indicates whether this feature is available or not.
P627(7) = 0This feature
is not
available
P627(7) = 1This feature
is
available
Setting the spindle analog output via PLCI
To do this, use the combination: M1956 - R156.
Register R156 sets the spindle analog output in units of 2.442 mV. (10 / 4095)
R156 = 0000 1111 1111 1111
(R1256=4095)
= 10V.
R156 = 0001 1111 1111 1111
= -10V.
R156 = 0000 0000 0000 0001
(R1256=1)
= 2.5 mV.
R156 = 0001 0000 0000 0001
= -2.5 mV.
In order for the CNC to assume the value allocated to register R156, one must activate mark M1956 as described
in the PLCI Manual (section 5.5.2. Writing internal CNC variables).
Spindle controlled either by the CNC or by the PLCI
The CNC may have two internal spindle analog outputs, that of the CNC itself and the one set by the PLCI.
Use PLCI output O27 to "tell" the CNC which one of them to output.
O27 = 0
Spindle analog output set by the CNC itself.
O27 = 1
Spindle analog output set by the PLCI (combination: M1956-R156).
1.3 READING INTERNAL CNC VARIABLES
From this version on, the PLCI and the PLC64 have access to more internal CNC information.
With the PLCI, there is no need to activate a mark to access this information. The CNC itself updates this information
at the beginning of each PLCI cycle scan.
With the PLC 64, the corresponding mark must be consulted every time a CNC variable is to be checked.
The CNC information now accessible is:
Real S in rpm (REG119 at the PLCI, M1919 at the PLC64)
Not to be mistaken with R112 which indicates the programmed Spindle speed (S).
It is given in rpm and in hexadecimal format. Example: S 2487 R119= 967
Number of the block in execution (REG120 at the PLCI, M1920 at the PLC64)
It is given in hexadecimal format. Example: N120 R120= 78
Code of the last key pressed (B0-7 REG121 at the PLCI, Not available at the PLC64)
Not to be mistaken with register R118 which also indicates the code corresponding to the last key pressed,
but
-
-
When pressing a key, both registers have the same value; but
the data in R121 is only kept there for one cycle
scan
whereas
R118 keeps its value until another key is pressed
.
When pressing the same key several times, (for example: 1111):
R121 will show code "1" four times (once per cycle scan).
R118 will always show the same value, thus not being able to tell whether the "1" key has been pressed once
or more times.
The key codes are listed in the appendix of the PLCI manual.
Summary of Contents for 8025 GP
Page 1: ...CNC 8025 GP M MS New Features Ref 0107in...
Page 9: ...FAGOR 8025 8030 CNC Models M MG MS GP OPERATING MANUAL Ref 9701 in...
Page 14: ...COMPARISON TABLE FOR MILL MODEL FAGOR 8025 8030 CNCs...
Page 22: ...Introduction 1 INTRODUCTION...
Page 94: ...ERROR CODES...
Page 102: ...FAGOR 8025 8030 CNC Models M MG MS GP PROGRAMMING MANUAL Ref 9701 in...
Page 107: ...COMPARISON TABLE FOR MILL MODEL FAGOR 8025 8030 CNCs...
Page 115: ...Introduction 1 INTRODUCTION...
Page 164: ...44 8025 8030 CNC PROGRAMMING MANUAL 2 N50 G90 G03 G36 R5 X50 Y50 I0 J30 F100 N60 G01 X50 Y0...
Page 177: ...8025 8030 CNC PROGRAMMING MANUAL 57 C P P P C P P P C P P P...
Page 178: ...58 8025 8030 CNC PROGRAMMING MANUAL P P C P C P P P C P P P P P C P C P P P...
Page 179: ...8025 8030 CNC PROGRAMMING MANUAL 59 C P P P C P P P P P C P P P C P C P P P...
Page 251: ...8025 8030 CNC PROGRAMMING MANUAL 131 Pitch in X Pitch in Y...
Page 255: ...8025 8030 CNC PROGRAMMING MANUAL 135 Pitch in Y Pitch in X...
Page 259: ...8025 8030 CNC PROGRAMMING MANUAL 139...
Page 262: ...142 8025 8030 CNC PROGRAMMING MANUAL...
Page 266: ...146 8025 8030 CNC PROGRAMMING MANUAL...
Page 279: ...8025 8030 CNC PROGRAMMING MANUAL 159 Starting plane Reference plane...
Page 284: ...164 8025 8030 CNC PROGRAMMING MANUAL Starting plane Reference plane...
Page 288: ...168 8025 8030 CNC PROGRAMMING MANUAL Reference plane Starting plane...
Page 299: ...8025 8030 CNC PROGRAMMING MANUAL 179 Starting plane Reference plane...
Page 314: ...194 8025 8030 CNC PROGRAMMING MANUAL FEED...
Page 321: ...8025 8030 CNC PROGRAMMING MANUAL 201 Starting plane Ref plane Feed...
Page 336: ...216 8025 8030 CNC PROGRAMMING MANUAL DIRECTION AND SIGN OF THE ANGLES XY Plane XZ Plane...
Page 389: ...8025 8030 CNC PROGRAMMING MANUAL 269 Subroutines flow chart...
Page 392: ...ERROR CODES...
Page 400: ...FAGOR 8025 8030 CNC APPLICATIONS MANUAL Ref 9701 in...