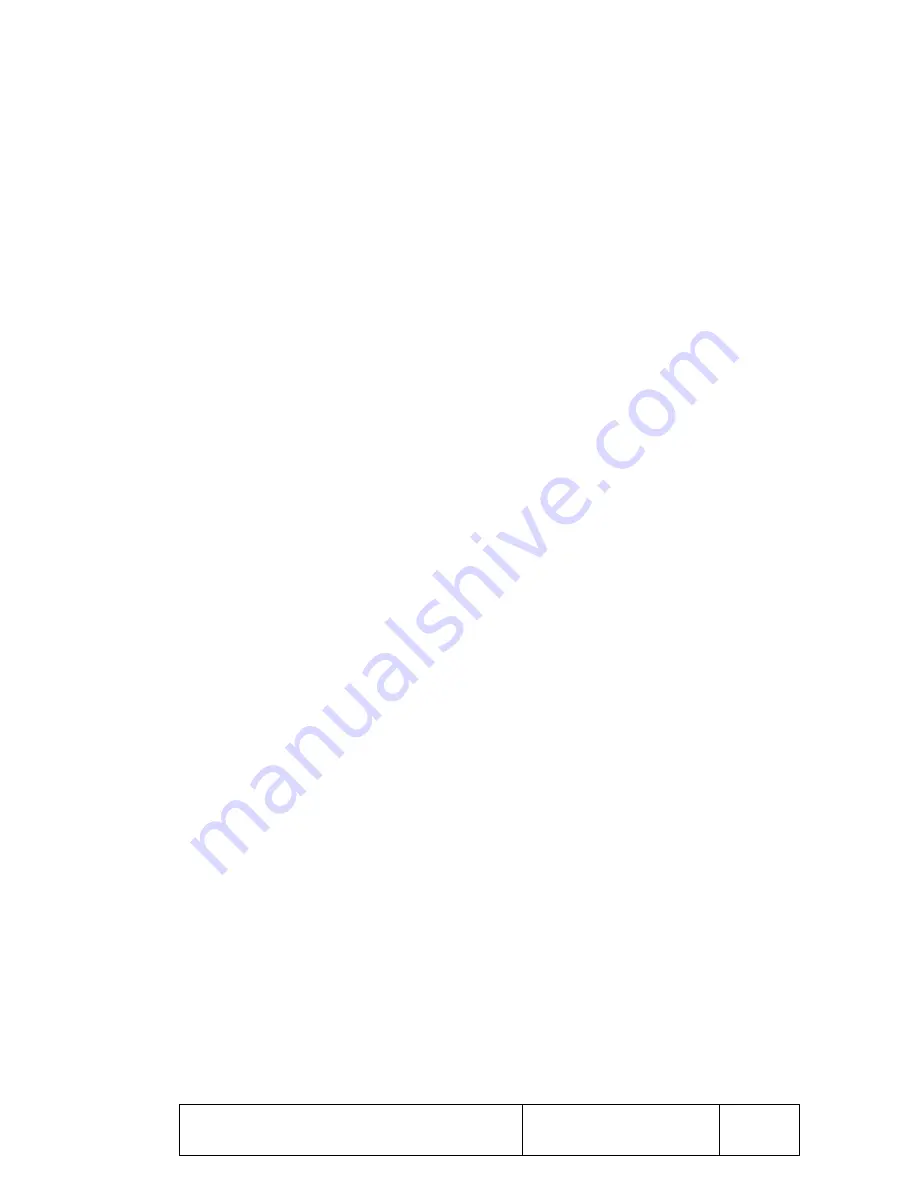
Page
Chapter: 1
Section:
LASER MACHINES
5
1.3 SHEETMETAL TRACING
When using this feature, it is necessary to set machine parameter P622(6) to "1".
With this feature it is possible to keep the focusing distance of the laser beam constant,
thus achieving an optimum machining quality even on very wavy sheetmetal surfaces.
To do this, a sensor must be used attached to the axis of the laser beam. This sensor
will provide, at all times, the feedback signals indicating to the CNC the deviations
of the actual sheetmetal surface with respect to its theoretical value.
The axis supporting the focus of the laser beam must be set as the "Z" axis and the
feedback signals of the sensor must be connected through the "V" axis feedback
input. Also, the "V" axis must be set as a DRO axis by means of machine parameter
“P617(3)=1”.
The CNC offers miscellaneous (auxiliary) functions M97, M98 and M99 which have
the following meaning when working with this feature (sheetmetal tracing):
M97 to activate the "sheetmetal tracing" feature. This function is used when
the counting directions of the Z and V axes are the same.
M98 to activate the "sheetmetal tracing" feature. This function is used when
the counting directions of the Z and V axes are not the same.
M99 to end or cancel the "sheetmetal tracing" feature.
The machine parameters to be set when using this feature are:
P619(3) Analog S output proportional to actual axis feedrate.
P622(6) Sheetmetal tracing on laser machines.
P806
Beam focusing distance (between beam and sheetmetal).
P807
Maximum sheetmetal deflection.
P808
Analog voltage corresponding to maximum Z axis feedrate.
Whenever the "sheetmetal tracing" feature is used, the CNC behaves as follows:
1.- When M97 or M98 is executed, the CNC will activate this feature.
2.- The laser beam (Z axis) will move towards the sheetmetal until the sensor attached
to it makes contact with the sheetmetal surface.
The maximum feedrate to be used in this approach move is set by machine
parameter "P808".
As a safety measure, the Z axis must be moved before executing M97 or M98.
Otherwise, the CNC will issue error 102.
SHEETMETAL TRACING
Summary of Contents for 8025 GP
Page 1: ...CNC 8025 GP M MS New Features Ref 0107in...
Page 9: ...FAGOR 8025 8030 CNC Models M MG MS GP OPERATING MANUAL Ref 9701 in...
Page 14: ...COMPARISON TABLE FOR MILL MODEL FAGOR 8025 8030 CNCs...
Page 22: ...Introduction 1 INTRODUCTION...
Page 94: ...ERROR CODES...
Page 102: ...FAGOR 8025 8030 CNC Models M MG MS GP PROGRAMMING MANUAL Ref 9701 in...
Page 107: ...COMPARISON TABLE FOR MILL MODEL FAGOR 8025 8030 CNCs...
Page 115: ...Introduction 1 INTRODUCTION...
Page 164: ...44 8025 8030 CNC PROGRAMMING MANUAL 2 N50 G90 G03 G36 R5 X50 Y50 I0 J30 F100 N60 G01 X50 Y0...
Page 177: ...8025 8030 CNC PROGRAMMING MANUAL 57 C P P P C P P P C P P P...
Page 178: ...58 8025 8030 CNC PROGRAMMING MANUAL P P C P C P P P C P P P P P C P C P P P...
Page 179: ...8025 8030 CNC PROGRAMMING MANUAL 59 C P P P C P P P P P C P P P C P C P P P...
Page 251: ...8025 8030 CNC PROGRAMMING MANUAL 131 Pitch in X Pitch in Y...
Page 255: ...8025 8030 CNC PROGRAMMING MANUAL 135 Pitch in Y Pitch in X...
Page 259: ...8025 8030 CNC PROGRAMMING MANUAL 139...
Page 262: ...142 8025 8030 CNC PROGRAMMING MANUAL...
Page 266: ...146 8025 8030 CNC PROGRAMMING MANUAL...
Page 279: ...8025 8030 CNC PROGRAMMING MANUAL 159 Starting plane Reference plane...
Page 284: ...164 8025 8030 CNC PROGRAMMING MANUAL Starting plane Reference plane...
Page 288: ...168 8025 8030 CNC PROGRAMMING MANUAL Reference plane Starting plane...
Page 299: ...8025 8030 CNC PROGRAMMING MANUAL 179 Starting plane Reference plane...
Page 314: ...194 8025 8030 CNC PROGRAMMING MANUAL FEED...
Page 321: ...8025 8030 CNC PROGRAMMING MANUAL 201 Starting plane Ref plane Feed...
Page 336: ...216 8025 8030 CNC PROGRAMMING MANUAL DIRECTION AND SIGN OF THE ANGLES XY Plane XZ Plane...
Page 389: ...8025 8030 CNC PROGRAMMING MANUAL 269 Subroutines flow chart...
Page 392: ...ERROR CODES...
Page 400: ...FAGOR 8025 8030 CNC APPLICATIONS MANUAL Ref 9701 in...