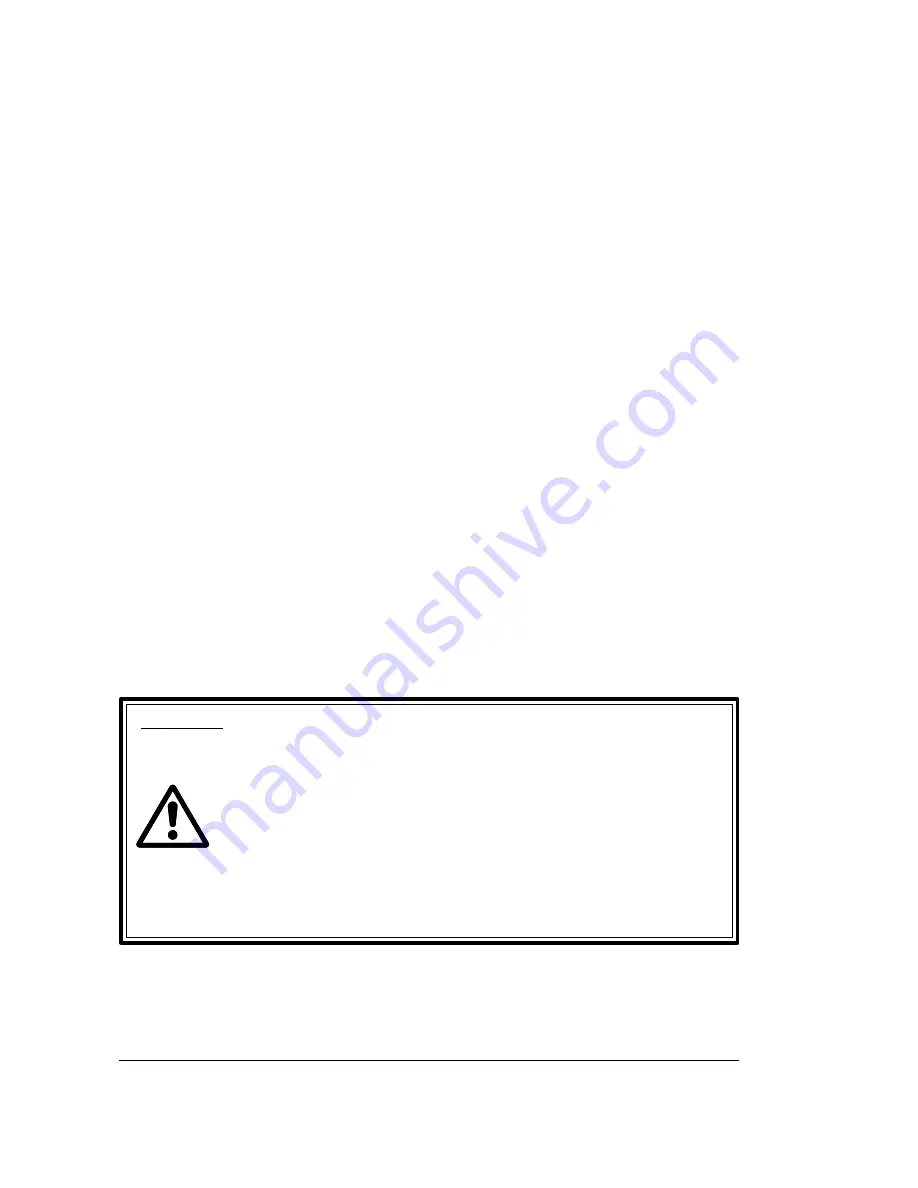
190
8025/8030 CNC PROGRAMMING MANUAL
6.32.8. G87. Rectangular pocket milling canned cycle
The operations and movements of the tool are as follows:
- If the spindle was previously running, it continues to rotate in the same direction. If it
was not running it starts clockwise (M03).
- Rapid movement of the Z axis from the starting plane to the reference (approach) plane.
- Movement a 50% of the working feedrate (F) of the Z axis for a distance equal to (D+B).
D: Distance between the reference plane and the surface of the part.
B: Depth value of each machining pass.
- Milling at working feedrate (F) of the pocket surface by steps defined by C, to a distance
L (finishing pass), of the pocket wall.
- Milling at the working feedrate H, of the finishing pass.
- After completing the finishing pass, the tool withdraws in rapid move to the pocket
center, positioning the Z axis 1 mm higher. In this way, the first penetration is finished.
- Movement at 50% of the working feedrate (F) of the Z axis for a distance equal to B+1.
- Milling at working feedrate (F) of the pocket surface (second penetration).
- The above steps are repeated until the full depth of the pocket is reached.
- Once the pocket is completed, the tool withdraws in rapid (Z axis) to the reference plane
(if G99 has been programmed) or to the starting plane (if G98 has been programmed).
Atention:
To enable a good finish to be achieved in the machining of pockets the
CNC performs a tangential approach and tangential exit in the last pass
of each of thepenetrations. For this purpose, the tool has to withdraw to
the center of the pocket before beginning the milling of the wall. To avoid
problems and possible machining malfunctions, it is mandatory to
program the tool code (T2.2) and to enter in the tool table the value of the
radius of the tool that is to be used. If the radius value entered in the tool
table is RO, the final wall pass is performed like all the others; i.e. with
neither tangential entry nor tangential exit. The value or R must never
be negative. If T2.2 is not programmed, the CNC takes as tool radius the
value of R of the last corrector.
Summary of Contents for 8025 GP
Page 1: ...CNC 8025 GP M MS New Features Ref 0107in...
Page 9: ...FAGOR 8025 8030 CNC Models M MG MS GP OPERATING MANUAL Ref 9701 in...
Page 14: ...COMPARISON TABLE FOR MILL MODEL FAGOR 8025 8030 CNCs...
Page 22: ...Introduction 1 INTRODUCTION...
Page 94: ...ERROR CODES...
Page 102: ...FAGOR 8025 8030 CNC Models M MG MS GP PROGRAMMING MANUAL Ref 9701 in...
Page 107: ...COMPARISON TABLE FOR MILL MODEL FAGOR 8025 8030 CNCs...
Page 115: ...Introduction 1 INTRODUCTION...
Page 164: ...44 8025 8030 CNC PROGRAMMING MANUAL 2 N50 G90 G03 G36 R5 X50 Y50 I0 J30 F100 N60 G01 X50 Y0...
Page 177: ...8025 8030 CNC PROGRAMMING MANUAL 57 C P P P C P P P C P P P...
Page 178: ...58 8025 8030 CNC PROGRAMMING MANUAL P P C P C P P P C P P P P P C P C P P P...
Page 179: ...8025 8030 CNC PROGRAMMING MANUAL 59 C P P P C P P P P P C P P P C P C P P P...
Page 251: ...8025 8030 CNC PROGRAMMING MANUAL 131 Pitch in X Pitch in Y...
Page 255: ...8025 8030 CNC PROGRAMMING MANUAL 135 Pitch in Y Pitch in X...
Page 259: ...8025 8030 CNC PROGRAMMING MANUAL 139...
Page 262: ...142 8025 8030 CNC PROGRAMMING MANUAL...
Page 266: ...146 8025 8030 CNC PROGRAMMING MANUAL...
Page 279: ...8025 8030 CNC PROGRAMMING MANUAL 159 Starting plane Reference plane...
Page 284: ...164 8025 8030 CNC PROGRAMMING MANUAL Starting plane Reference plane...
Page 288: ...168 8025 8030 CNC PROGRAMMING MANUAL Reference plane Starting plane...
Page 299: ...8025 8030 CNC PROGRAMMING MANUAL 179 Starting plane Reference plane...
Page 314: ...194 8025 8030 CNC PROGRAMMING MANUAL FEED...
Page 321: ...8025 8030 CNC PROGRAMMING MANUAL 201 Starting plane Ref plane Feed...
Page 336: ...216 8025 8030 CNC PROGRAMMING MANUAL DIRECTION AND SIGN OF THE ANGLES XY Plane XZ Plane...
Page 389: ...8025 8030 CNC PROGRAMMING MANUAL 269 Subroutines flow chart...
Page 392: ...ERROR CODES...
Page 400: ...FAGOR 8025 8030 CNC APPLICATIONS MANUAL Ref 9701 in...