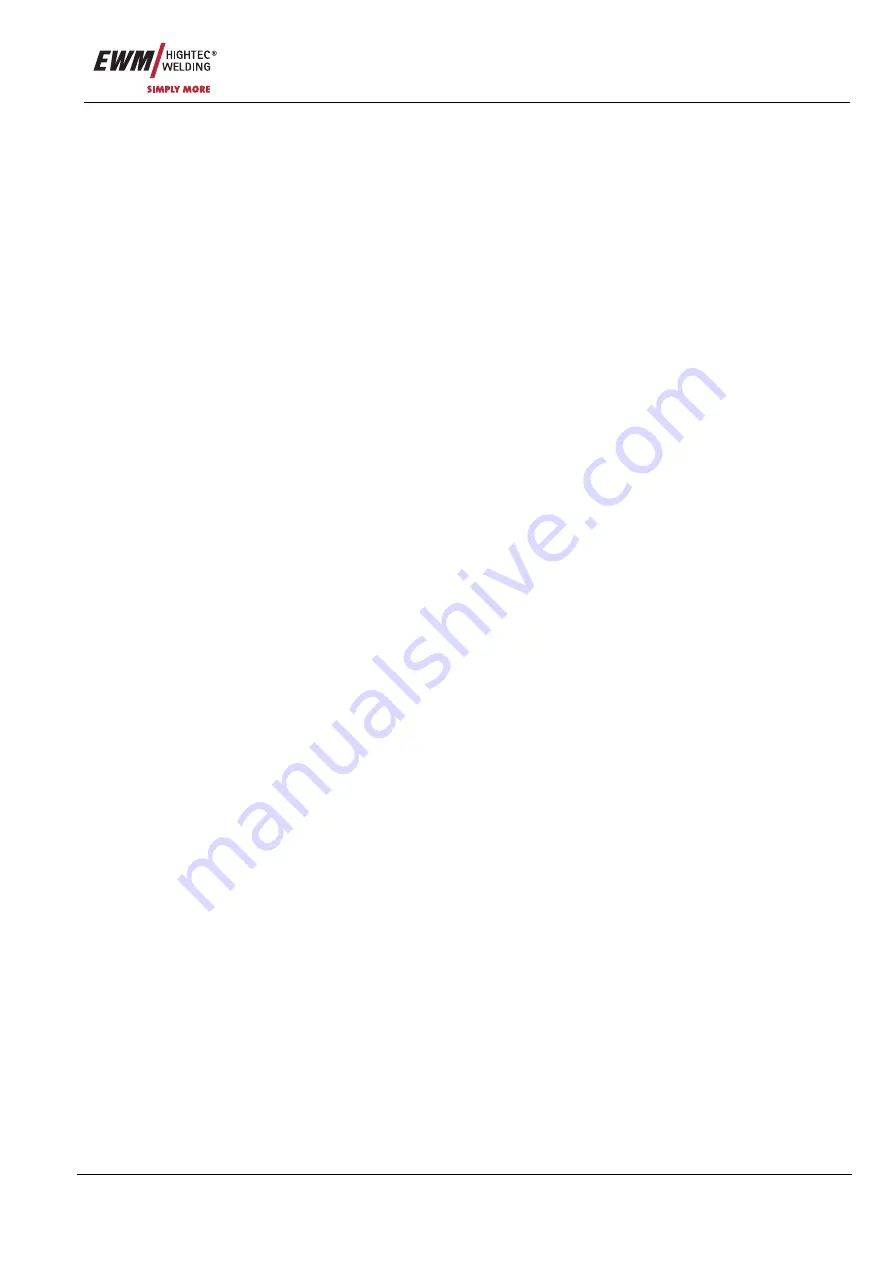
Operative mode
Check-back of the process parameters
Item No.: 099-008225-EWM01
31
5.9.6
Ready for welding
The system is ready for welding and accepts a start signal from the PLC. The signal is reset in the event
of errors. When switching a job, the signal is reset for a duration of approx. 200 ms.
From software version 0.0.A.X, the signal is no longer reset during the process!
5.9.7
Sticking
The wire touches the workpiece, or is fused to the workpiece. Virtually no current flows via the workpiece.
The detection is carried out at the end of the welding process (see also chapter “Fusing detection” for
more information). With TETRIX systems with retrofitted sensor voltage, it is also possible to detect the
fusing of the electrode in TIG processes.
5.9.8
Error number
Indicates a system error together with the “Collective error” status signal (see also chapter “Operating
problems, causes and remedies”). System errors must be acknowledged before re-starting.
Some system errors cannot be acknowledged due to their severity.
5.9.9
Actual welding voltage value
Transfer of the actual welding voltage of the process. The value is updated every 30ms.
5.9.10 Actual welding current value
Transfers the actual welding current in the process; value is updated every 30ms.
When using the configuration with fast actual value detection, the values for voltage and current
are updated every 5ms in the corresponding configuration of the field bus. This should be taken
into account when designing the field bus system and the transfer cycles.
5.9.11 Actual wire feed speed value
Transfer of the current wire speed for the process. Value is updated every 30ms.
5.9.12 Actual motor current value
Transfer of the actual motor current for the wire conveyor system. Value is updated every 30ms.
5.9.13 Parameter monitoring
Display of the status for the parameters being monitored. Signals are normally set to 0 if the monitoring is
inactive or the parameter in question is within the tolerance band (for details, see chapter Monitoring
function).
5.9.14 I > 0 Auxiliary process
Feedback from the auxiliary process to the PLC. Set when the auxiliary process is activated or reset, if
the auxiliary process has been deactivated.
5.9.15 Process signals diagram
To explain the process signals, a description of the non-latched special operating mode is given below. In
non-latched operating mode, the start and end programs are left out as appropriate: