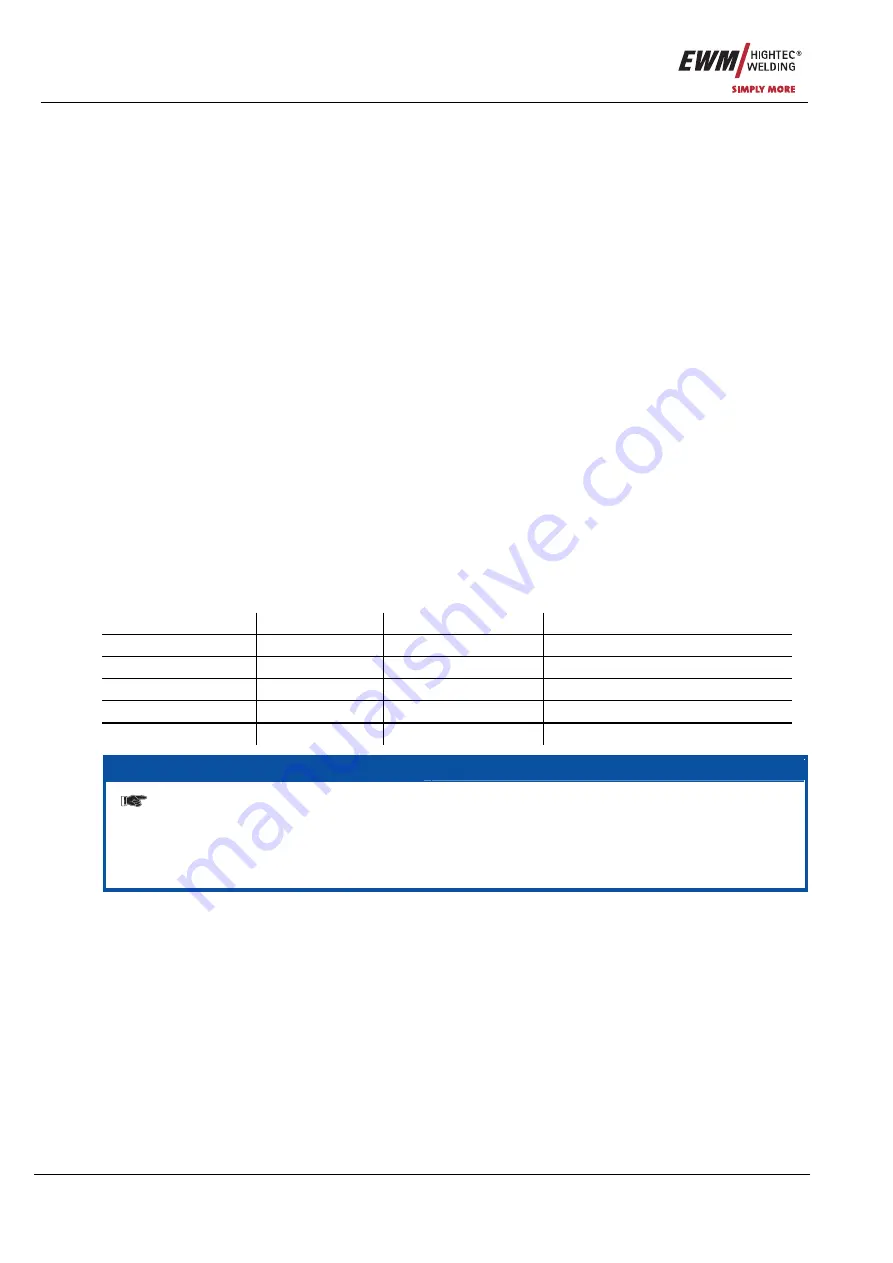
Commissioning
General connection of the BUSINTX11
12
Item No.: 099-008225-EWM01
4 Commissioning
This chapter describes for you the commissioning process of the BUSINTX11, step-by-step, as well as its
operating functions.
4.1
General connection of the BUSINTX11
4.1.1
The system bus
The BUSINTX11 is integrated into the PHOENIX/TETRIX welding system using a digital system bus. The
connection can be made in two different ways, depending on the type of installation for the control:
• Connection via the 15-pole SUB-D plug X12 when installing the BUSINTX11 on the power source (in
the suspended casing on the rear of the power source).
• Connection via the 7-pole X13 binder plug connector using the round cable control line. This is the
preferred connection method for external assembly of the BUSINTX11, e.g. in a switching cabinet.
In general with external assembly, it is important to ensure that the bus cabling for connecting the
BUSINTX11 to the relevant field bus is as far away as possible from potential sources of interference
(such as HF-carrying cables or cables under load), as otherwise there is a risk of bus assemblies being
damaged by the effects of excess voltages.
4.1.2
Power supply
4.1.2.1 Internal
The interface is normally supplied with power via a standalone, isolated power supply via the system bus.
The bus node remains addressable as long as the welding power source is switched on.
4.1.2.2 External
So that the bus node remains functional even after the system is shut down (e.g. for continued operation
of the user-defined inputs and outputs), an optional, external voltage of 24V DC must be used which is
powered by a separate module!
Depending on the design of the control, the PCBs vary for the power supply. The table below clarifies the
connection of the voltage:
System PCB
Plug
Pin
Polarity
SV+/-15V/1A X5
1
+24V
X5
2 GND
SV IBUS3
X2
1
+24V
X2
2 GND
NOTE
Depending on the field bus used, an external power supply is required
(e.g. on the Interbus).
When using the external power supply, the original EWM module must be used, otherwise
the potential isolation within the system is cancelled. EWM accepts no responsibility for
operating problems caused by this.