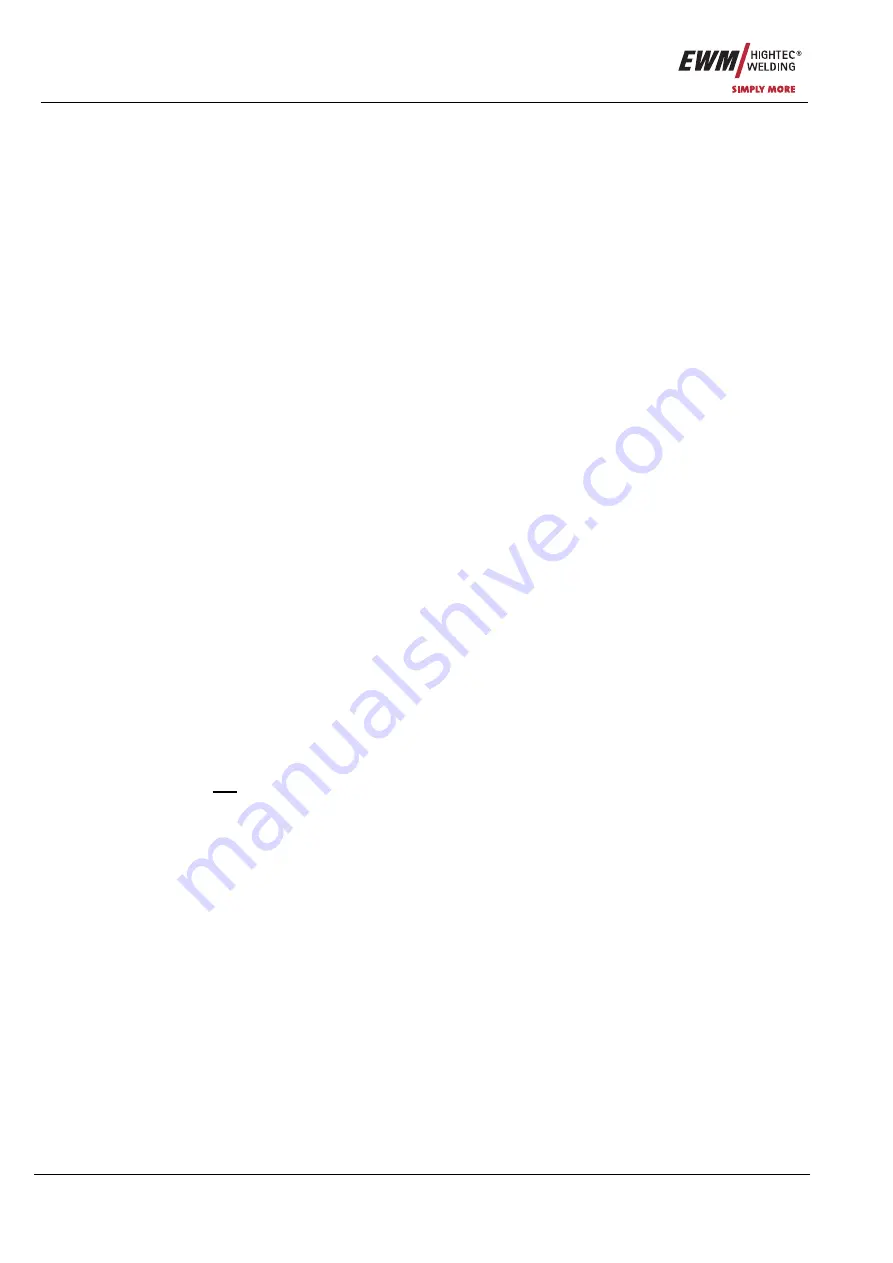
Operative mode
Check-back of the process parameters
30
Item No.: 099-008225-EWM01
5.8.12 Welding simulation
Activates the simulation of the welding process signals for the actual programming/testing of automation
controls without active welding process with complete signal exchange (see also chapter “Welding
simulation”).
5.8.13 JOB mode
In this mode the information for operating type and welding type are not taken from individual actuation
signals, but rather from the welding program actuated.
5.8.14 User-defined output
This signal can be used to activate the user-defined relay output on the module.
5.8.15 WF switching
This signal can be used to change over 2 wire feed drive units when the system is at a standstill. By
default, WF number 1 active after switching on (see also the operating manual on the “WF switching”
option).
5.8.16 TANDEM operation (PHOENIX only)
This function is available as an optional software and in PHOENIX systems permits the control of one
power source in each case (for TANDEM systems, 2 BUSINTX11 are required). The input signal is used
to determine which power source is the documented power source in the TANDEM combination.
On non-actuation, the power source is configured as the slave.
5.9
Check-back of the process parameters
During operation, a variety of parameters are transferred to the higher level control via the field bus.
Some of these parameters are available as a visual signal on the module in the form of LEDs (see
chapter “Status display”).
5.9.1
I > 0 (Current flows signal)
Used to feed back the welding process to the PLC. The signal is normally set by the process after the arc
has been ignited and cancelled after the arc has been extinguished. For improved signal matching with
the higher level control, the signal is stored for a certain period during welding in the event of a stoppage
(see also chapter “Signals for matching with the positioning device”)
The signal can be reset by a fault during the welding process.
5.9.2
User-defined inputs
There are 3 additional inputs with 24V logic which can be used by the user. The signals are filtered using
a time constant of approx. 50ms.
The signals are also processed further with an external power supply when the welding machine has
been switched off.
The inputs are not isolated.
5.9.3
Process active
In order to indicate the end of the welding process to the higher level control, this signal is reset when the
system is in idle mode. During the welding process the signal is set to 1.
5.9.4
Main current signal
Used specifically in non-latched special operating mode to trigger the positioning device to the end of the
ignition program, or the start of the end program.
5.9.5
Collision protection
Indicates the status from a collision protection device connected to the module. The signal has a wire
break-proof design, which means that it is still active even if the sensor is not active. This should be taken
into account when designing the system and programming the machine.
The signal is treated with high priority to ensure rapid processing and also continues to be processed with
an external power supply to the module when the welding machine has been shut down.