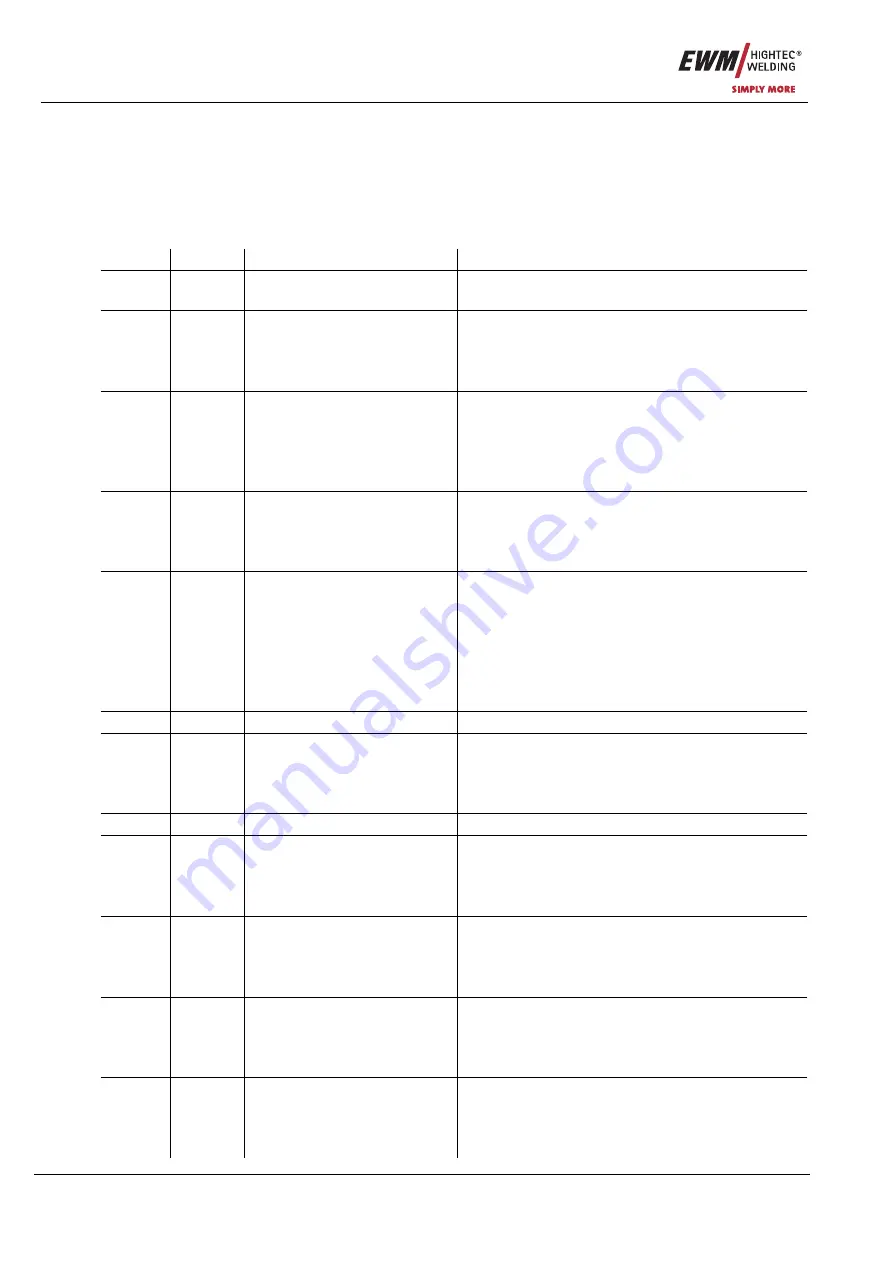
Profiles for PHOENIX MIG/MAG systems
Profiles for the CANopen module
44
Item No.: 099-008225-EWM01
7.2
Profiles for the CANopen module
In general the module uses the standard Rx-PDOs 1 and 2 (no. 1 for digital and no. 2 for analogue
signals) and the standard Tx-PDOs 1 to 3 (no. 1 for digital and nos. 2 and 3 for analogue data).
7.2.1
Reis Robotics profile (switch position 0)
The module uses a data capacity of 6 words (12 bytes) for the input data and 7 words (14 bytes) for the
output data.
Rx-PDO 1
Cob ID = 200h + address
Byte
no.
Bit no.
Function
Description
0 0 Start
Bit allocation:
0
1
Start signal to initiate the welding process
Signal stop on system
Signal start on system
0 1 Robot
ready
Bit allocation:
0
1
Safety signal for rapid shut-down
No ready message from robot, no start possible,
rapid shut-down carried out in the process
Robot ready message, start is possible
0
2
Select welding mode
Bit allocation:
0
1
Select between normal/pulse welding
Normal welding active
Pulse welding active
0
3-4
Select operating mode
Bit allocation:
Bit1 Bit0
0 0
0 1
1 0
1 1
Select between non-latched/special non-latched
Non-latched operating mode
Not used
Not used
Special non-latched operating mode
0 5 Reserved
0
6
Check monitoring function
Bit allocation:
0
1
Activate/deactivate welding parameter monitoring
Monitoring deactivated
Monitoring activated
0 7 Reserved
1
0
Gas test 1
Bit allocation:
0
1
Manual check of the process gas supply
Gas supply off
Gas supply on
1 1 Inching
Bit allocation:
0
1
Signal for wire inching function on the wire feed
drive
Inching off
Inching on
1 2 Reverse
inching
Bit allocation:
0
1
Signal for reverse wire inching function
Reverse inching off
Reverse inching on
1 3 Error
reset
Bit allocation:
0
1
Acknowledgement signal for system error
Signal must have positive edge for
acknowledgement