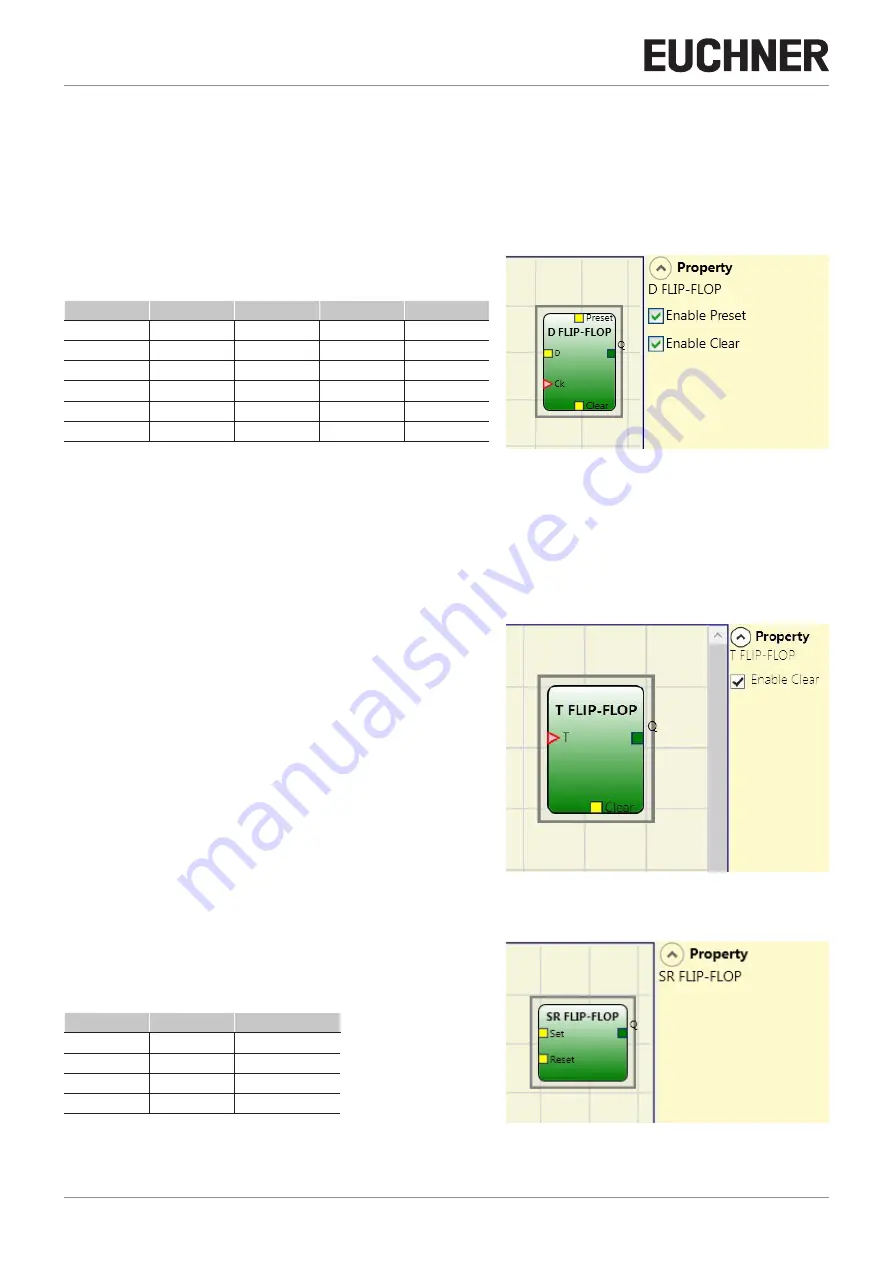
Operating Instructions
Modular Safety Control System MSC
132
(Translation of the original operating instructions) 2121331-04-04/19
9.4.2. Memory operators
Operators of the type MEMORY make it possible to save data (TRUE or FALSE) that come from other project components.
Status changes are undertaken according to the truth tables given for each operator.
9.4.2.1. D FLIP FLOP (max. number = 16)
Using the D FLIP-FLOP operator the status set previously on the Q
output is saved according to the following truth table.
Preset
Clear
Ck
D
Q
1
0
X
X
1
0
1
X
X
0
1
1
X
X
0
0
0
L
X
Retain memory
0
0
Rising edge
1
1
0
0
Rising edge
0
0
Figure 149: D Flip-Flop
Parameter
Enable Preset: If selected, the Q output can be set to "1" (TRUE).
Enable Clear: If selected, the memory process can be reset.
9.4.2.2. T FLIP FLOP (max. number = 16)
This operator toggles the Q output on each rising edge on the T
(Toggle) input .
Parameter
Enable Clear: If selected, the memory process can be reset.
Figure 150: T Flip-Flop
9.4.2.3. SR FLIP FLOP (max. number = 16)
Using the SR FLIP-FLOP operator the Q output is set to "1" using Set
and "0" using Reset.
See truth table below:
SET
Reset
Q
0
0
Retain memory
0
1
0
1
0
1
1
1
0
Figure 151: SR Flip-Flop
Summary of Contents for MSC
Page 1: ...EN Operating Instructions Installation and use Modular Safety Control System MSC ...
Page 171: ......
Page 173: ......