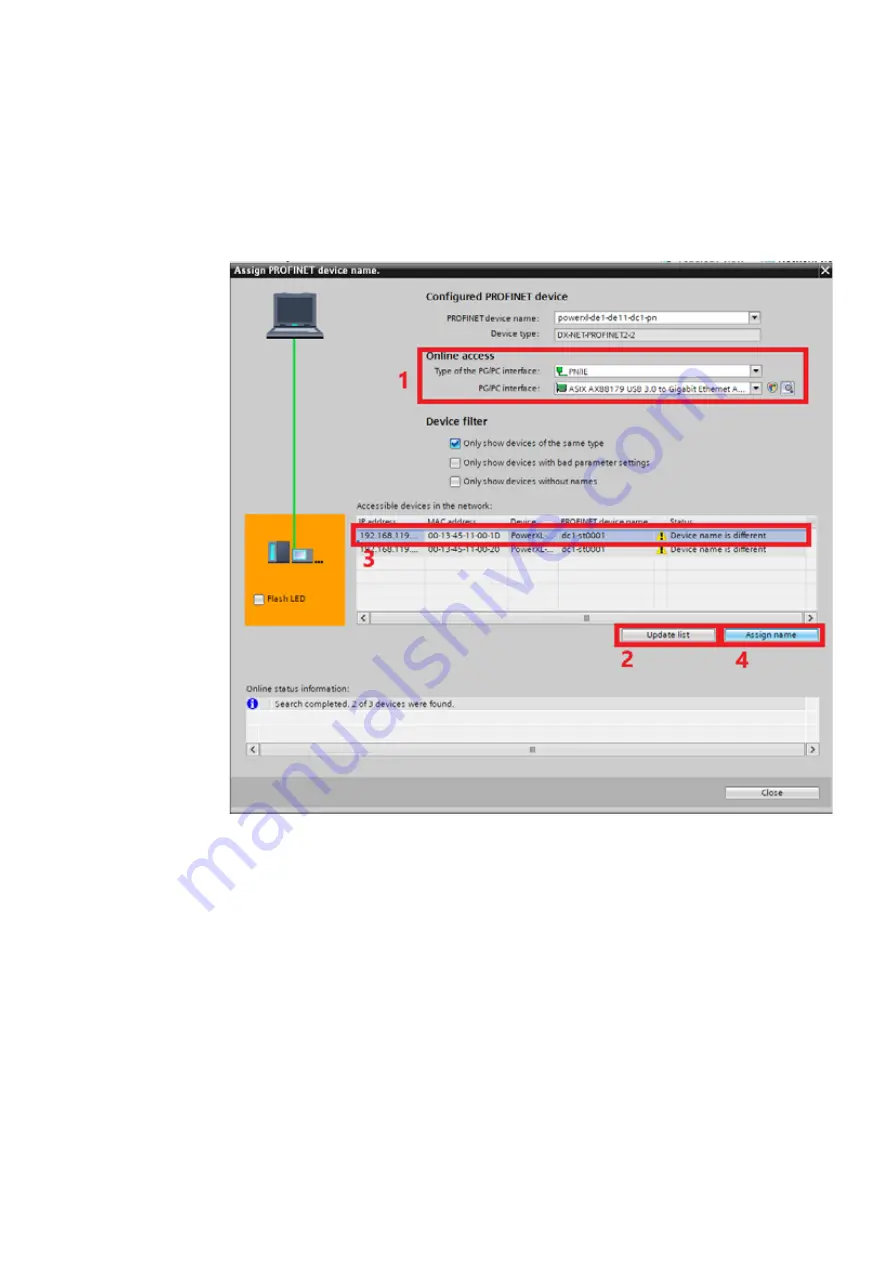
5 Application example
5.7 Example program – DX-NET-PROFINET2-2 with TIA Portal
DX-NET-PROFINET2-2
01/22 MN040062EN
www.eaton.com
109
▶
10.Select the properties of the DX-NET-PROFINET2-2 communication
interface.
You can assign the IP address and the device name in the “PROFINET inter-
face” settings. Then click
Assign name
.
Figure 48:
Assigning device names