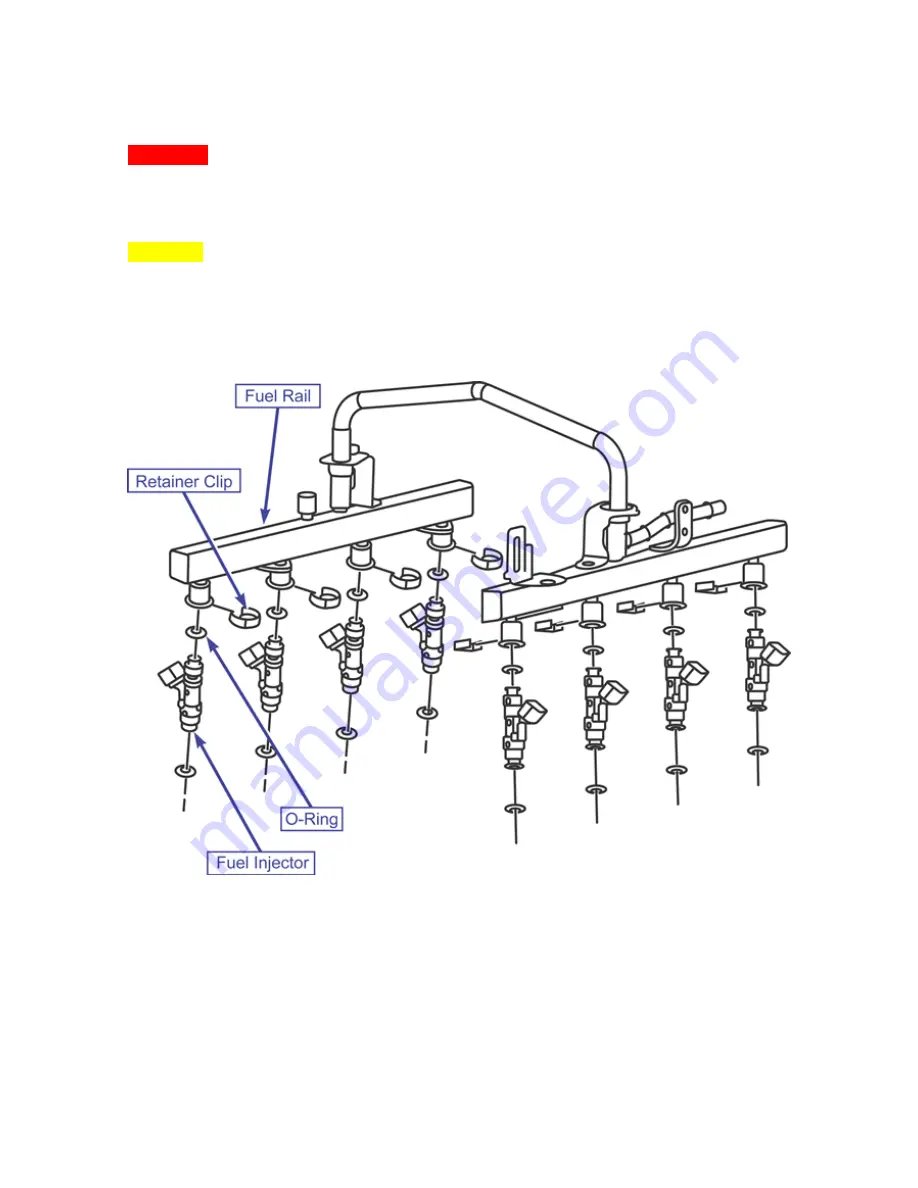
To Remove:
WARNING
Be careful when removing the fuel injectors in order to prevent damage to the connector
pins and nozzles. Submerging the injectors in any cleaners or solvents may damage the
injectors.
CAUTION
Fuel injector leakage may contaminate the engine oil.
Fuel injector removal and installation
1. Remove the fuel rail assembly from the cylinder head.
2. Disconnect the fuel injector connectors.
3. Remove and discard the fuel injector retainer clips from the fuel injectors
4. Remove the fuel injectors from the fuel rail.
5. Remove and discard the fuel injector o-ring seals.
Summary of Contents for TrailBlazer
Page 1: ......
Page 26: ...Fig 3 Typical body and undervehicle maintenance locations Refer to chart for descriptions ...
Page 29: ......
Page 30: ......
Page 31: ......
Page 175: ...Spring free length check Valve spring squareness check ...
Page 192: ...Front of piston mark ...
Page 361: ...5 3L Engine Except Saab Underhood Fuse Block 2003 2005 Early Production ...
Page 469: ...Removing the outer band from the CV boot Removing the inner band from the CV boot ...
Page 470: ...Removing the CV boot from the joint housing Clean the CV joint housing prior to removing boot ...
Page 471: ...Removing the CV joint housing assembly Removing the CV joint ...
Page 472: ...Inspecting the CV joint housing Removing the CV joint outer snap ring ...
Page 473: ...Checking the CV joint snap ring for wear CV joint snap ring typical ...
Page 474: ...Removing the CV joint assembly Removing the CV joint inner snap ring ...
Page 475: ...Installing the CV joint assembly typical ...
Page 553: ...9 Torque the lug nuts to specification 10 Lower the vehicle ...
Page 556: ...Toe in Frame Misalignment Frame misalignment ...
Page 588: ...Bleeding caliper ...
Page 624: ...Manifold gauge set components Refrigerant recovery recycling station ...
Page 676: ...A C Specifications ...
Page 677: ......