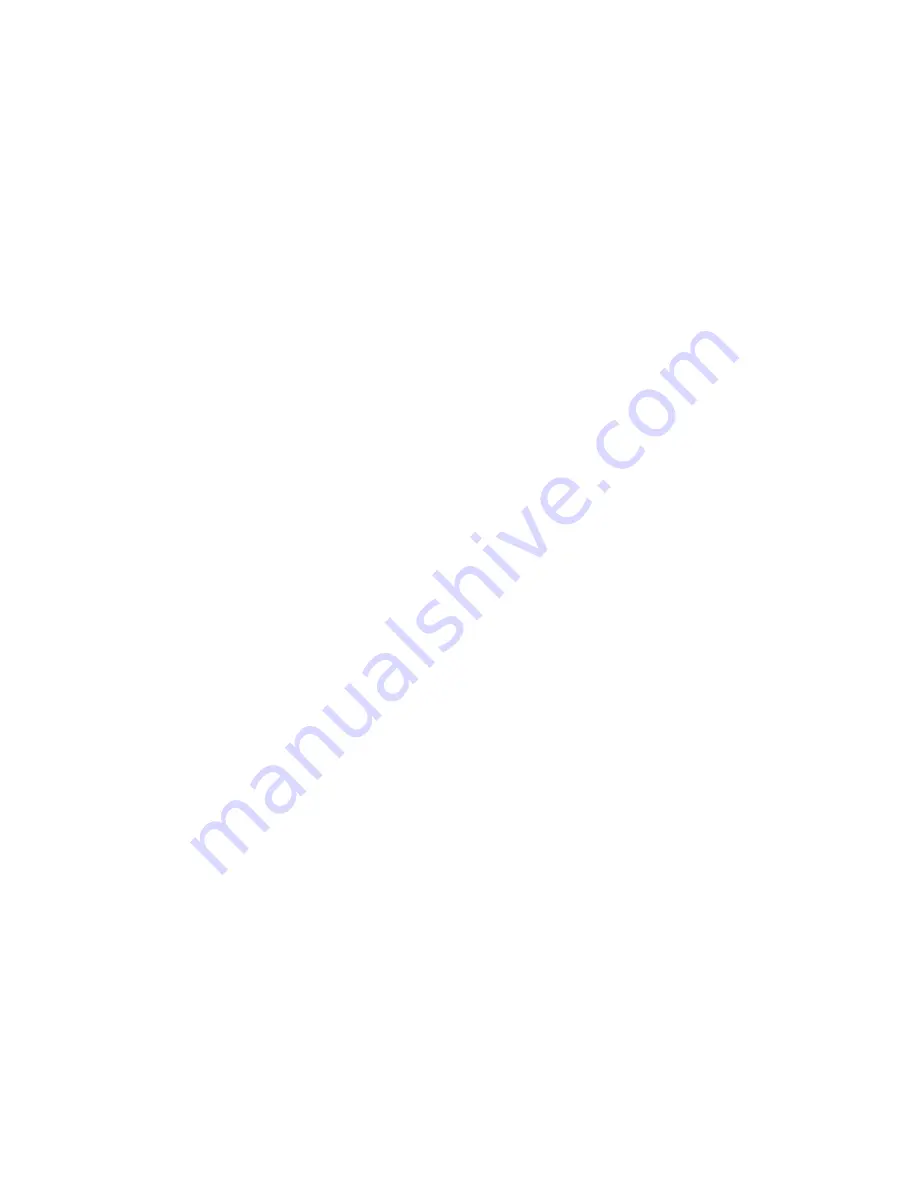
Knurling is a process in which metal is displaced and raised, thereby reducing clearance,
providing a true center, and oil control. In some cases, a knurled valve guide will not stand
up for more than a short time.
Installing a guide insert involves machining the worn guide to accept a bronze insert. One
style is the coil-type which is installed into a guide that has been threaded. Another is the
thin-walled insert where the worn guide is reamed oversize to accept a split-sleeve insert.
After the insert is installed, a special tool is then run through the guide to expand the
insert, locking it to the guide. The insert is then reamed to provide the proper valve stem
clearance.
Reaming for oversize valves restores normal clearances and provides a true valve seat.
Most cast-in type guides can be reamed to accept a valve with an oversize stem.
Oversized valves are generally 0.003 to 0.030 in. (0.076 to 0.762mm), with 0.015 in.
(0.381mm) being the most common.
To replace cast-in type valve guides, they must be drilled out, and then reamed to accept
replacement guides. This must be done on a fixture which will allow centering and leveling
off of the original valve seat or guide, otherwise a serious guide-to-seat misalignment can
occur making it impossible to properly machine the seat.
Replaceable-type guides, commonly found in aluminum cylinder heads are pressed into
the cylinder head. A hammer and a stepped drift or punch may be used to install and
remove the guides. Before removing the guides, measure the protrusion on the spring side
of the head and record it for installation. Use the stepped drift to hammer out the old guide
from the combustion chamber side of the head. When installing, determine whether or not
the guide seals a water jacket in the head. If it does, use the recommended sealing agent.
If the valve guides do not seal any water jackets grease the valve guide and its bore. Use
the stepped drift and a hammer to drive the new guide into the cylinder head from the
spring side (top) of the cylinder head. A stack of washers the same thickness as the
measured protrusion may help the installation process. Measure the guide heights to verify
correct installation.
Valve Seats
NOTE:
Before any valve seat machining can be performed, the guides must be within
factory recommended specifications.
NOTE:
If any machining or replacements were made to the valve guides, the seats must
be machined.
If the seats are in good condition, the valves can be lapped to the seats, and the cylinder
head assembled.
If the valve seats are worn, cracked or damaged, they must be replaced. The valve seat
must be perfectly centered to the valve guide, which requires very accurate machining.
Summary of Contents for TrailBlazer
Page 1: ......
Page 26: ...Fig 3 Typical body and undervehicle maintenance locations Refer to chart for descriptions ...
Page 29: ......
Page 30: ......
Page 31: ......
Page 175: ...Spring free length check Valve spring squareness check ...
Page 192: ...Front of piston mark ...
Page 361: ...5 3L Engine Except Saab Underhood Fuse Block 2003 2005 Early Production ...
Page 469: ...Removing the outer band from the CV boot Removing the inner band from the CV boot ...
Page 470: ...Removing the CV boot from the joint housing Clean the CV joint housing prior to removing boot ...
Page 471: ...Removing the CV joint housing assembly Removing the CV joint ...
Page 472: ...Inspecting the CV joint housing Removing the CV joint outer snap ring ...
Page 473: ...Checking the CV joint snap ring for wear CV joint snap ring typical ...
Page 474: ...Removing the CV joint assembly Removing the CV joint inner snap ring ...
Page 475: ...Installing the CV joint assembly typical ...
Page 553: ...9 Torque the lug nuts to specification 10 Lower the vehicle ...
Page 556: ...Toe in Frame Misalignment Frame misalignment ...
Page 588: ...Bleeding caliper ...
Page 624: ...Manifold gauge set components Refrigerant recovery recycling station ...
Page 676: ...A C Specifications ...
Page 677: ......