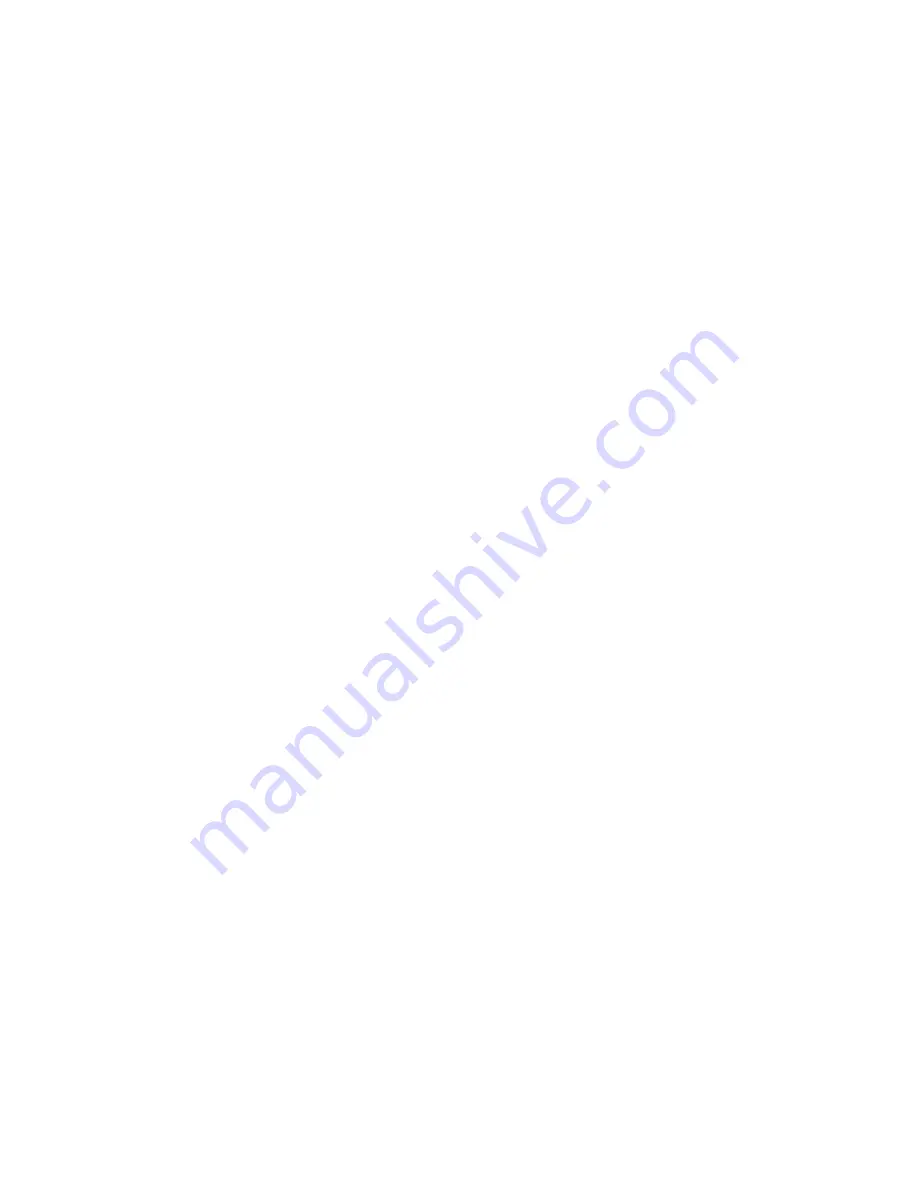
test, then plug the "noid" light into the injector connector. Start the engine and the "noid"
light should flash, signaling that the injector driver circuit is working. If the "noid" light
flashes, but the injector does not click when plugged in, test the injector’s resistance.
Resistance should be between 13.8-15.2 Ohms. Repeat this procedure on each injector,
noting which cylinder(s) are faulty.
If the "noid" light does not flash, the injector driver circuit is faulty. Shut OFF the engine,
and then disconnect the negative battery cable. Unplug the "noid" light from the injector
connector and unplug the PCM. Check the harness between the appropriate pins on the
harness side of the PCM connector and the injector connector. Resistance should be less
than 5.0 ohms; if not, repair the circuit. If resistance is within specification, the injector
driver inside the PCM is faulty. Replace the PCM.
Fuel Injector Balance Test
Preliminary Checks
1. Verify spark or lack of spark available at each cylinder
2. Verify fuel pressure and condition of fuel supply system
Injector Balance Test Procedure
1. Connect a fuel pressure gauge to the fuel rail pressure connection.
2. Connect a Scan Tool, turn the to "ON" and Select Special Functions, Fuel System -
Injector Balance Test
3. Select injector #1; the fuel system will prime. Record the initial pressure reading
immediately after the fuel pump shuts off.
4. Press the soft key to pulse the first injector. Record the 'Pressure After Pulse'
reading immediately after the injector stops pulsing
5. Select and test each remaining injector. Be sure to record the Initial Pressure
reading after each fuel system prime!
Injector Balance Test Analysis
1. Subtract the 'Pressure After Pulse' reading from the Initial Pressure reading for
each cylinder, record as Subtracted Value.
2. Identify and record the 'Maximum Subtracted Value' and the 'Minimum Subtracted
Value'.
3. Subtract the Minimum Reading from the Maximum Reading to obtain Max
Difference.
4. If the Max Difference is less than 20 kPa (2.9psi), the injector are all flowing about
the same and should not be replaced.
5. If the Max Difference is greater than 20 kPa (2.9psi), you have one or more faulty
injector(s). Replace the injector that appears to be different than the rest (Injector
#4 in the example above). Repeat the balance test with the new injector to make
sure that Max Difference is now less than 20 kPa (2.9psi).
Summary of Contents for TrailBlazer
Page 1: ......
Page 26: ...Fig 3 Typical body and undervehicle maintenance locations Refer to chart for descriptions ...
Page 29: ......
Page 30: ......
Page 31: ......
Page 175: ...Spring free length check Valve spring squareness check ...
Page 192: ...Front of piston mark ...
Page 361: ...5 3L Engine Except Saab Underhood Fuse Block 2003 2005 Early Production ...
Page 469: ...Removing the outer band from the CV boot Removing the inner band from the CV boot ...
Page 470: ...Removing the CV boot from the joint housing Clean the CV joint housing prior to removing boot ...
Page 471: ...Removing the CV joint housing assembly Removing the CV joint ...
Page 472: ...Inspecting the CV joint housing Removing the CV joint outer snap ring ...
Page 473: ...Checking the CV joint snap ring for wear CV joint snap ring typical ...
Page 474: ...Removing the CV joint assembly Removing the CV joint inner snap ring ...
Page 475: ...Installing the CV joint assembly typical ...
Page 553: ...9 Torque the lug nuts to specification 10 Lower the vehicle ...
Page 556: ...Toe in Frame Misalignment Frame misalignment ...
Page 588: ...Bleeding caliper ...
Page 624: ...Manifold gauge set components Refrigerant recovery recycling station ...
Page 676: ...A C Specifications ...
Page 677: ......