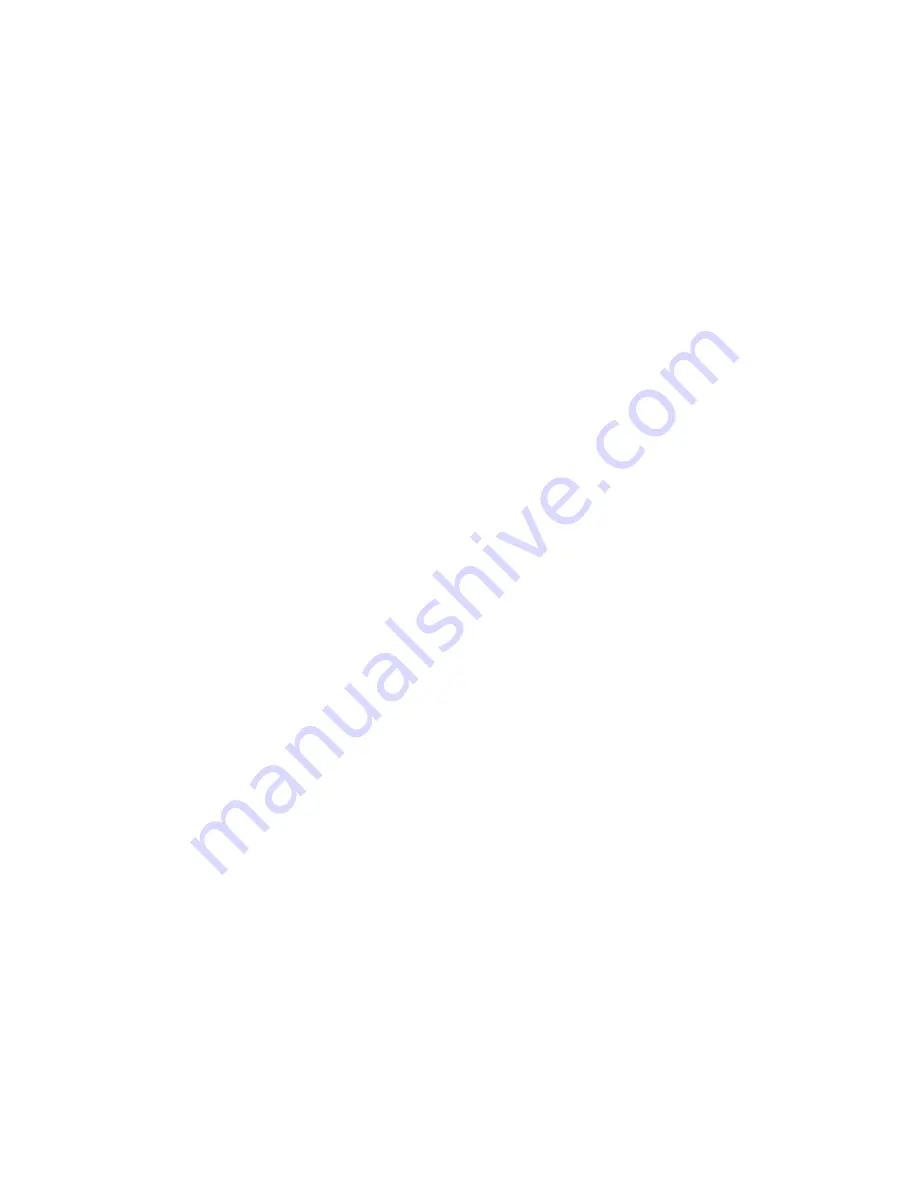
All pistons employ some type of seal, usually made of rubber, to minimize fluid leakage. A
rubber dust boot seals the outer end of the cylinder against dust and dirt. The boot fits
around the outer end of the piston on disc brake calipers, and around the brake actuating
rod on wheel cylinders.
The hydraulic system operates as follows: When at rest, the entire system, from the
piston(s) in the master cylinder to those in the wheel cylinders or calipers, is full of brake
fluid. Upon application of the brake pedal, fluid trapped in front of the master cylinder
piston(s) is forced through the lines to the wheel cylinders. Here, it forces the pistons
outward, in the case of drum brakes, and inward toward the disc, in the case of disc
brakes. The motion of the pistons is opposed by return springs mounted outside the
cylinders in drum brakes, and by spring seals, in disc brakes.
Upon release of the brake pedal, a spring located inside the master cylinder immediately
returns the master cylinder pistons to the normal position. The pistons contain check
valves and the master cylinder has compensating ports drilled in it. These are uncovered
as the pistons reach their normal position. The piston check valves allow fluid to flow
toward the wheel cylinders or calipers as the pistons withdraw. Then, as the return springs
force the brake pads or shoes into the released position, the excess fluid reservoir through
the compensating ports. It is during the time the pedal is in the released position that any
fluid that has leaked out of the system will be replaced through the compensating ports.
Dual circuit master cylinders employ two pistons, located one behind the other, in the
same cylinder. The primary piston is actuated directly by mechanical linkage from the
brake pedal through the power booster. The secondary piston is actuated by fluid trapped
between the two pistons. If a leak develops in front of the secondary piston, it moves
forward until it bottoms against the front of the master cylinder, and the fluid trapped
between the pistons will operate the rear brakes. If the rear brakes develop a leak, the
primary piston will move forward until direct contact with the secondary piston takes place,
and it will force the secondary piston to actuate the front brakes. In either case, the brake
pedal moves farther when the brakes are applied, and less braking power is available.
All dual circuit systems use a switch to warn the driver when only half of the brake system
is operational. This switch is usually located in a valve body which is mounted on the
firewall or the frame below the master cylinder. A hydraulic piston receives pressure from
both circuits, each circuit's pressure being applied to one end of the piston. When the
pressures are in balance, the piston remains stationary. When one circuit has a leak,
however, the greater pressure in that circuit during application of the brakes will push the
piston to one side, closing the switch and activating the brake warning light.
In disc brake systems, this valve body also contains a metering valve and, in some cases,
a proportioning valve. The metering valve keeps pressure from traveling to the disc brakes
on the front wheels until the brake shoes on the rear wheels have contacted the drums,
ensuring that the front brakes will never be used alone. The proportioning valve controls
the pressure to the rear brakes to lessen the chance of rear wheel lock-up during very
hard braking.
Warning lights may be tested by depressing the brake pedal and holding it while opening
one of the wheel cylinder bleeder screws. If this does not cause the light to go on,
Summary of Contents for TrailBlazer
Page 1: ......
Page 26: ...Fig 3 Typical body and undervehicle maintenance locations Refer to chart for descriptions ...
Page 29: ......
Page 30: ......
Page 31: ......
Page 175: ...Spring free length check Valve spring squareness check ...
Page 192: ...Front of piston mark ...
Page 361: ...5 3L Engine Except Saab Underhood Fuse Block 2003 2005 Early Production ...
Page 469: ...Removing the outer band from the CV boot Removing the inner band from the CV boot ...
Page 470: ...Removing the CV boot from the joint housing Clean the CV joint housing prior to removing boot ...
Page 471: ...Removing the CV joint housing assembly Removing the CV joint ...
Page 472: ...Inspecting the CV joint housing Removing the CV joint outer snap ring ...
Page 473: ...Checking the CV joint snap ring for wear CV joint snap ring typical ...
Page 474: ...Removing the CV joint assembly Removing the CV joint inner snap ring ...
Page 475: ...Installing the CV joint assembly typical ...
Page 553: ...9 Torque the lug nuts to specification 10 Lower the vehicle ...
Page 556: ...Toe in Frame Misalignment Frame misalignment ...
Page 588: ...Bleeding caliper ...
Page 624: ...Manifold gauge set components Refrigerant recovery recycling station ...
Page 676: ...A C Specifications ...
Page 677: ......