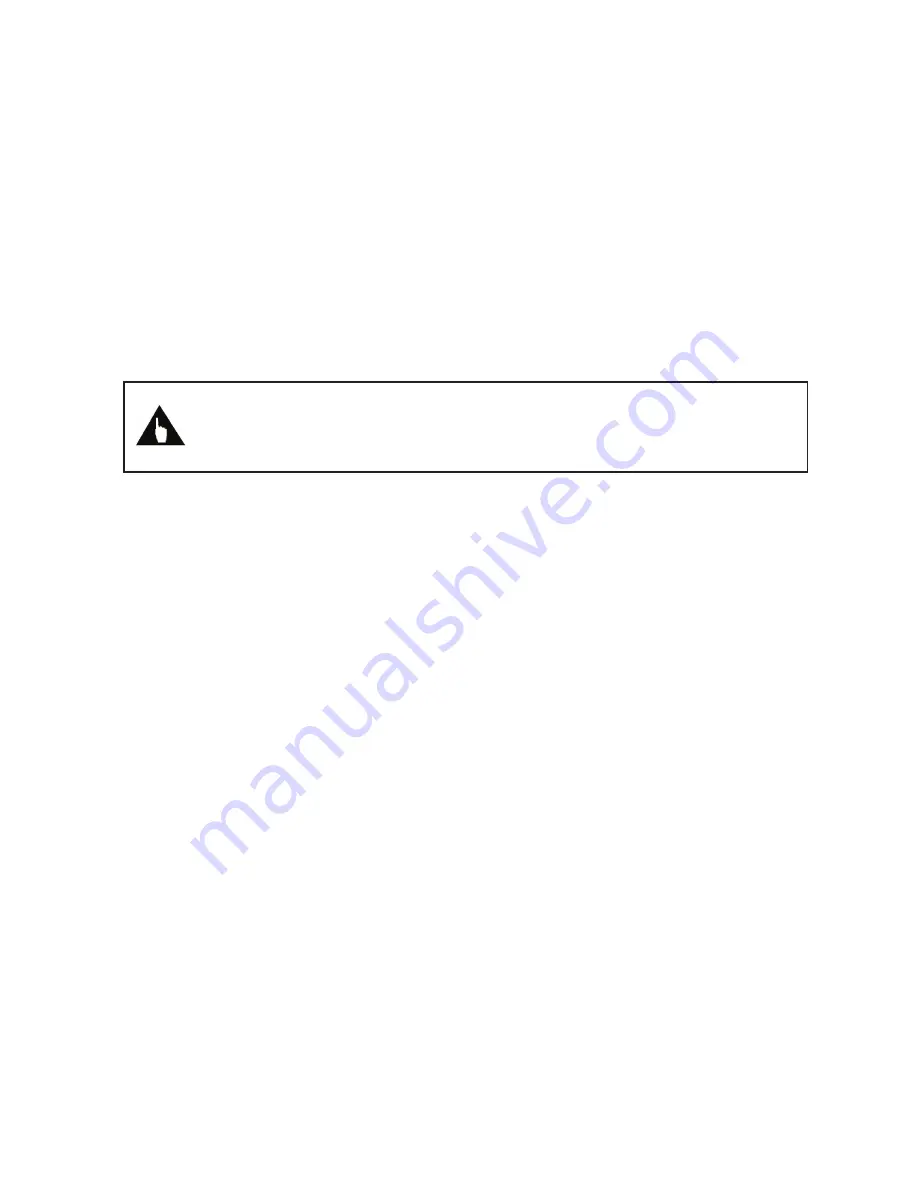
123
Troubleshooting Guide
Use this section to identify and correct operational problems. If none of the solutions correct the problem, or if the prob-
lem recurs, contact your customer support.
Note: During a leak test, there is a 40 second delay at the start of the cycle. The
disinfection cycle will not start until the leak test is complete.
This is normal operation and is not considered an “error”.
Reprocessor does not start.
No power to the reprocessor. ..............................
Check the main power connection.
GFCI is tripped ...................................................
Locate the GFCI on the inside back wall of the reprocessor.
Press the reset button on the GFCI. If the GFCI cannot be
reset, contact your customer support.
Main circuit breaker is tripped............................
Reset the circuit breaker. If the circuit breaker cannot be
reset, contact your customer support.
Defective connection to reprocessor...................
Unplug the reprocessor from wall socket. Check the power cable for damage.
Defective connection to motherboard.................
Check connections between the control panel and the
motherboard. Replace defective components, if necessary.
Blown power supply fuse ...................................
Check the power supply fuse, replace if necessary
Disinfection cycle does not start.
Software/hardware locked ..................................
Disconnect then reconnect the main power to reset the system.
Keypad not responding .......................................
Check the keypad connection. Replace the ribbon cable, if necessary.
Control panel defective.......................................
Replace the control panel.
Slow water fill into basin.
Air pressure insufficient to open valves..............
Verify the compressor is working correctly. Check the external air regulator
on non-compressor reprocessors. Contact your Facility
Maintenance representative.
Insufficient water supply pressure, flow rate......
Contact your location building maintenance.
External water pre-filter plugged........................
Replace the filter cartridge.
Internal water filter is plugged............................
If the pressure is low, replace the 0.2micron bio-retentive water filter.
Incoming water regulator setting is incorrect .....
Check the regulator setting. The setting must be flowing
pressure of 35 to 40psi. Do not adjust the regulator if the
setting is correct—check for a plugged filter.
Chapter 7
TROUBLESHOOTING
Summary of Contents for MEDIVATORS DSD EDGE
Page 1: ...1 Service Manual System Version 5 65...
Page 23: ...23 Figure 5 Function Keys...
Page 27: ...27 Figure 6 Set Date Screen...
Page 29: ...29 Figure 7 Set Time Screens...
Page 33: ...33 Figure 9 Display Log Screen and sample entry...
Page 42: ...42 Figure 14 Custom Program Setup Screens P1 Detergent Inject Set Minutes 00 00...
Page 43: ...43 Figure 15 Custom Program Setup Screen...
Page 51: ...51 Figure 22 Set Delayed Startup Screen...
Page 54: ...54...
Page 96: ...96 Notes...
Page 101: ...101 Figure 4 Depress locking ring Figure 5 Insert tube Figure 6 Locking ring out...
Page 115: ...115 Figure 28 Filter locations Figure 29 Disconnect the filter Figure 30 Verify inlet side...
Page 119: ...119 Figure 33 Fuse locations...
Page 121: ...121 Figure 34 Connect pressure gauge Figure 35 Bleed some air...
Page 141: ...141...
Page 142: ...142...
Page 143: ...143...
Page 149: ...149...
Page 150: ...150...
Page 151: ...151...