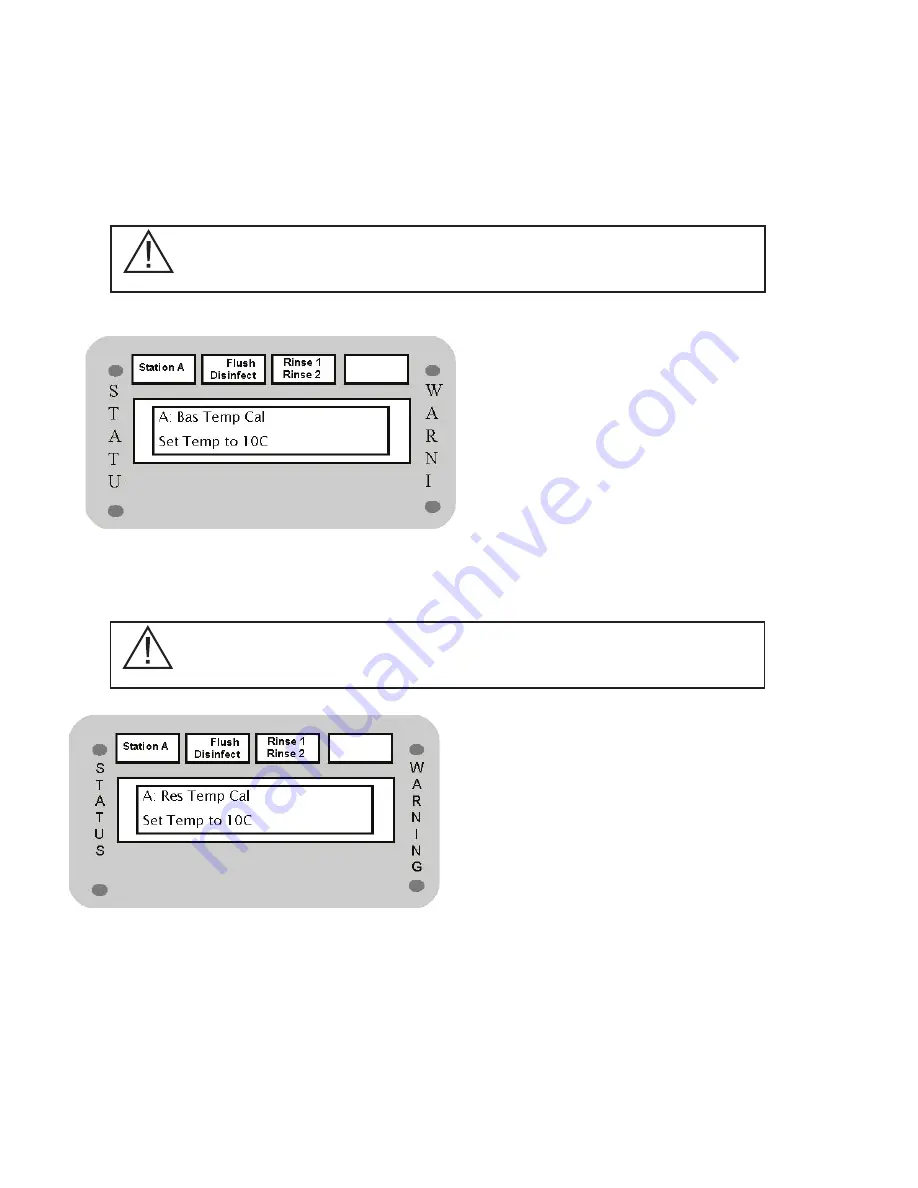
66
Function 31–Calibrate Basin Thermistor
This function calibrates the basin thermistor for the selected station.
Caution!
DO NOT attempt to calibrate the thermistor. Call MEDIVATORS
Technical Support for detailed instructions before proceeding.
Function 32–Calibrate Reservoir Thermistor
This function calibrates the reservoir thermistor for the selected station.
Caution!
DO NOT attempt to calibrate the thermistor. Call MEDIVATORS
Technical Support for detailed instructions before proceeding
Function 37-SSG Sub-Menu.
This function allows access to test the Single Shot Generator (SSG)
!
!
Summary of Contents for MEDIVATORS DSD EDGE
Page 1: ...1 Service Manual System Version 5 65...
Page 23: ...23 Figure 5 Function Keys...
Page 27: ...27 Figure 6 Set Date Screen...
Page 29: ...29 Figure 7 Set Time Screens...
Page 33: ...33 Figure 9 Display Log Screen and sample entry...
Page 42: ...42 Figure 14 Custom Program Setup Screens P1 Detergent Inject Set Minutes 00 00...
Page 43: ...43 Figure 15 Custom Program Setup Screen...
Page 51: ...51 Figure 22 Set Delayed Startup Screen...
Page 54: ...54...
Page 96: ...96 Notes...
Page 101: ...101 Figure 4 Depress locking ring Figure 5 Insert tube Figure 6 Locking ring out...
Page 115: ...115 Figure 28 Filter locations Figure 29 Disconnect the filter Figure 30 Verify inlet side...
Page 119: ...119 Figure 33 Fuse locations...
Page 121: ...121 Figure 34 Connect pressure gauge Figure 35 Bleed some air...
Page 141: ...141...
Page 142: ...142...
Page 143: ...143...
Page 149: ...149...
Page 150: ...150...
Page 151: ...151...