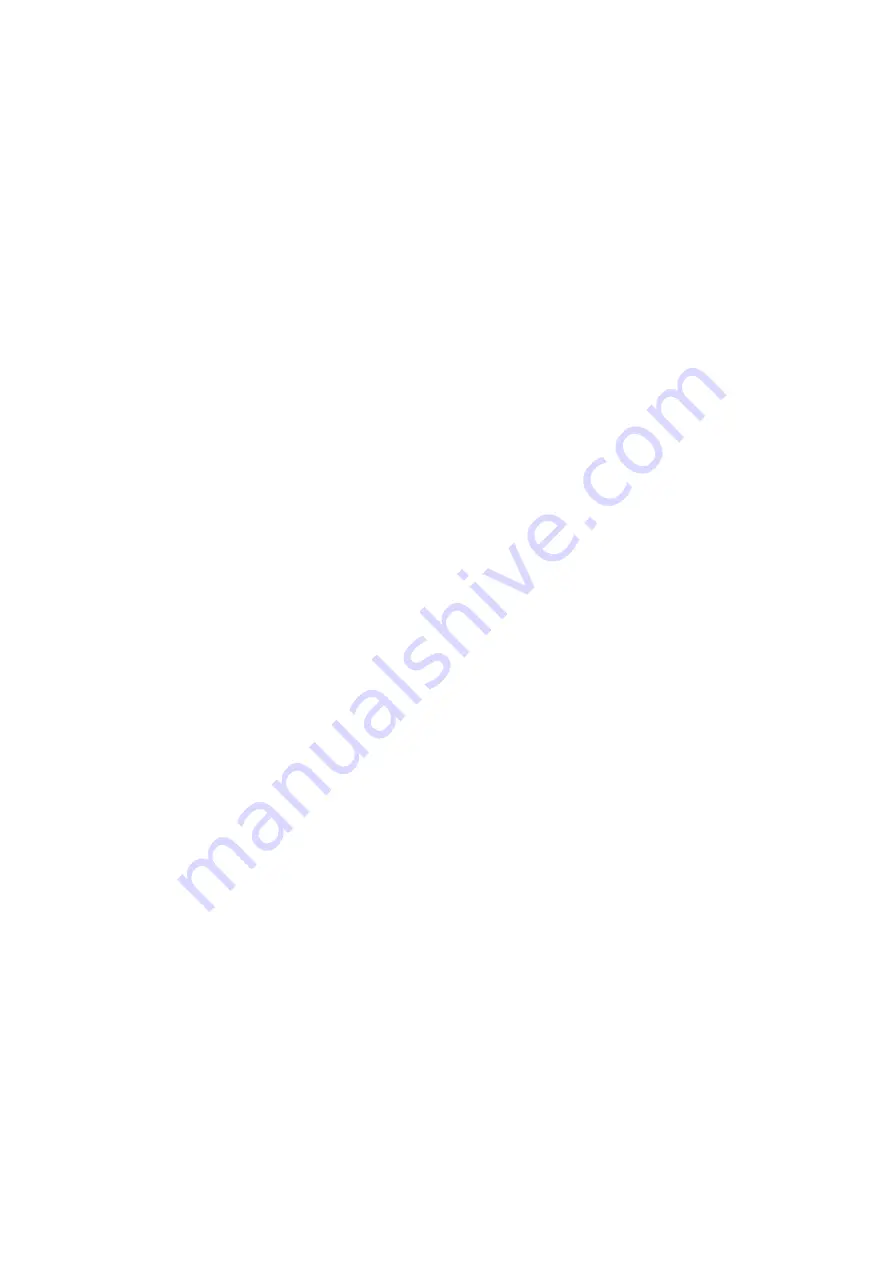
Though paper is loaded in the cassette, the display of the message "load paper of the drawer."
"The original scanning area is dirty." is displayed due to poor adjustment....................................... 67
"Place the originals again." is displayed after starting to copy with the copy board.......................... 70
The waste toner assembly cover does not open when the packing tape is removed....................... 72
The primary transfer roller drive coupling is coming off and breaking due to interfering with
Breakage of the boss of the idler gear due to wrongly assembled pick-up roller.............................. 75
Toner leaking from the ITB cleaning unit due to coming off of waste toner gear holder may occur.. 76
Opening waste toner cover/ toner leakage due to the defect waste toner case................................77
The LCD control panel displays a blank screen due to the disconnection of the HDMI cable.......... 79
Safety cover coming off of Tray 1 due to the safety cover being pressed hard to the rear side
Measures when paper is not stapled (corner/double) after installation (Inner Finisher-G1/H1/K1)...96
Noise (grinding-like noise) from the right rear side of Main Body......................................................98
Noise (squeaking noise) from the right rear side of Main Body.......................................................101
After turning ON the main switch, Abnormal noise/the display of the message "Close the upper
The waste toner gear holder comes off due to the contact during setting the yellow developing
Abnormal noises/toner leaking from the ITB cleaning unit due to coming off of waste toner
Noise of tooth jump from the main drive assembly and blurred image due to gear mounting
Abnormal sound from the registration guide unit during feeding papers.........................................113
Abnormal (chirruping) noise of the second delivery drive assembly of the main unit due to
Noise (an abnormal noise from meshing failure of tooth)/ toner soiling inside the machine /
stained images due to disengagement between gears in the waste toner drive assembly......... 118
"Replace Toner Cartridge" message is displayed on the initial installation or after replacing
"Toner cart. may be malfunctioning" message displayed due to a bottle connector cable failure
0107/0A07/010A/0A0A Jam code since harness is caught.............................................................122
0106/010B Jam Code due to the soiled duplex merging roller........................................................123
E514-0002/1C14 Jam code due to incorrect paper width of the aligning plate of the processing
020A jam cord due to the deformed 2nd delivery upper guide........................................................131
0003 jam code due to the use of ADF under a high temperature environment...............................134
ii
Summary of Contents for imageRUNNER ADVANCE C3330 Series
Page 83: ...iR ADV C3325i US 120V QTW07191 78 ...
Page 85: ...iR ADV C3325i US 120V QTW07191 iR ADV C3330i US 120V G QTX00507 80 ...
Page 105: ...If the symptom does not improve check other causes 100 ...
Page 124: ...4 Mount the left cover upper and then close the front cover 119 ...
Page 144: ...139 ...
Page 176: ...Inner Finisher_G1 EX QVA13172 171 ...
Page 197: ...Inner Finisher G1 EX QVA10470 192 ...