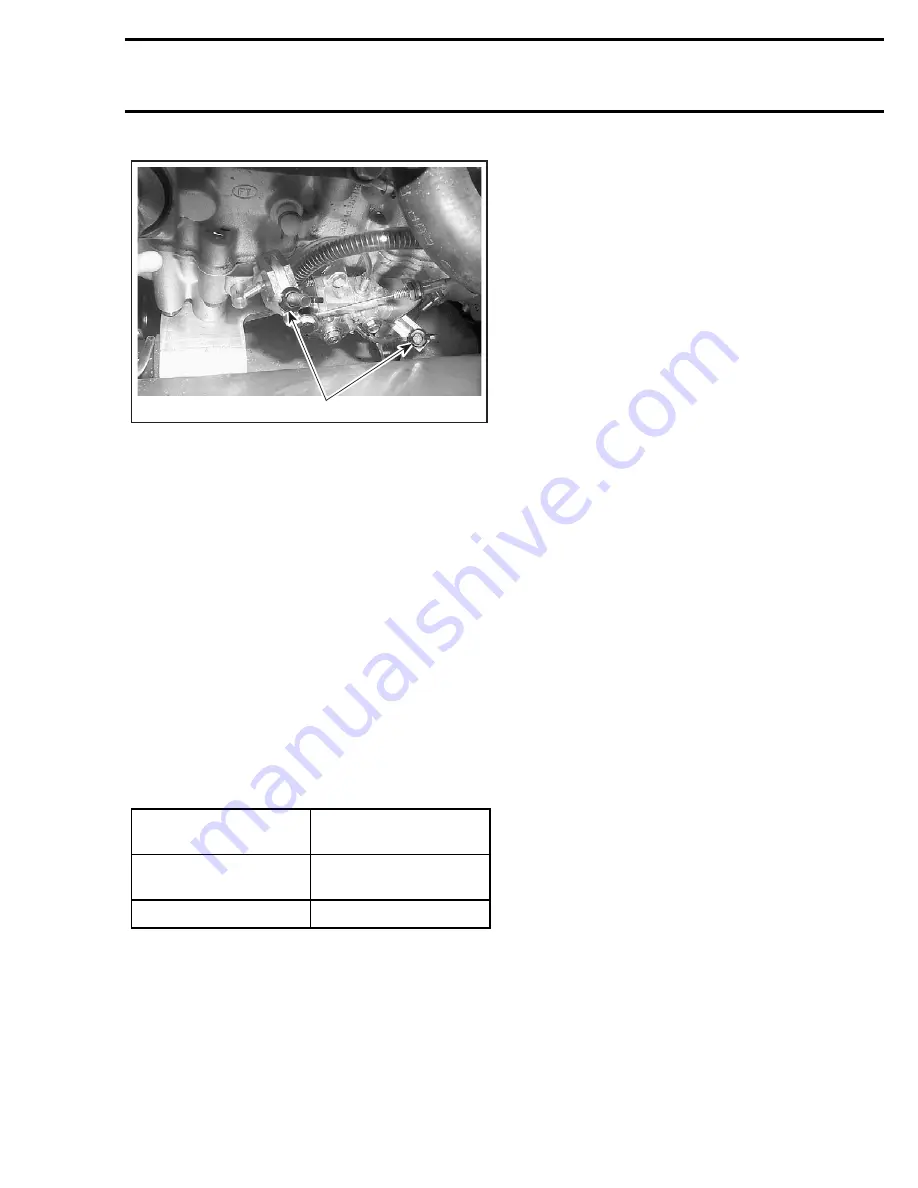
SECTION 05 - ENGINE PREPARATION
MMC2005-001_05A.FM
05-125
1
A33D13A
1. Hose pinchers on outlet hoses
Connect leak testing kit pu
m
p to special cap.
Pressurize oil syste
m
to 21 kPa (3 PSI).
T
hat pres-
sure
m
ust not drop during 3
m
inutes.
If pressure drops, locate leak(s) and repair/replace
leaking co
m
ponent(s).
NOTE:
An oil pu
m
p shaft test
m
ust be done to
co
m
plete the oil syste
m
leak test. Refer to LEA
K
T
ES
T
AND ENGINE DIMENSION MEASURE-
MEN
T
for the procedure.
OIL PUMP IDENTIFICATION
Pu
m
p Lever
Different engines need different pu
m
ps.
See
identification on lever
n
o. 4
.
CAUTION:
Always
m
ou
n
t proper pu
m
p o
n
e
n
-
gi
n
e.
ENGINE TYPE
OIL PUMP
IDENTIFICATION
5
93,
5
93 HO and
5
93 HO SDI
02
793 HO and SDI
01
CLEANING
Clean all
m
etal co
m
ponents in a non-ferrous
m
etal
cleaner.
DI
S
A
SS
EMBLY
NOTE:
So
m
e oil pu
m
p co
m
ponents are not avail-
able as single parts.
I
n
jectio
n
Oil Reservoir
E
m
pty injection oil reservoir
n
o. 6
by siphoning
injection oil.
Re
m
ove:
– air box
– upper screw (near reservoir cap)
– rewind starter support and grip
– hose protector support
– electronic
m
odule (MPEM)
– lower nut
n
o. 9
, screw
n
o. 10
and
n
o. 11
.
NOTE:
Cut the ties retaining the wiring harness if
necessary.
I
n
jectio
n
Oil Level
S
e
n
sor
T
o re
m
ove the switch, use the following proce-
dure.
Re
m
ove injection oil reservoir, as
m
entioned
above..
Unplug switch connector.
Pull oil level switch
n
o. 7
out of reservoir.
Before replacing the injection oil level sensor
n
o. 7
, check it according to the following proce-
dure:
CAUTION:
Do
n
ot re
m
ove or be
n
d the reed
switch protective float lock. It ca
n
da
m
age the
reed switch glass.
W
ith the float
m
agnet ring at the lowest position.
Using an oh
mm
eter, probe the connector.
Summary of Contents for ski-doo MACH Z 1000 SDI
Page 1: ...Mmc 2005 001 Racing FH8 Wed Sep 15 15 27 01 2004 Page 1 C M Y CM MY CY CMY K...
Page 118: ...04 36 MMC2005 001_04A FM SECTION 04 SUSPENSION SC 3 SC 4 RAS SC IV REAR SUSPENSION 0...
Page 124: ...04 42 MMC2005 001_04A FM SECTION 04 SUSPENSION SC 3 SC 4 RAS...
Page 476: ...MMC2005 001_13A FM 13 1 SECTION 13 ACCESSORIES TABLE OF CONTENTS 0 ACCESSORIES 13 02...
Page 493: ...Mmc 2005 001 Racing FH8 Wed Sep 15 15 27 01 2004 Page 1 C M Y CM MY CY CMY K...