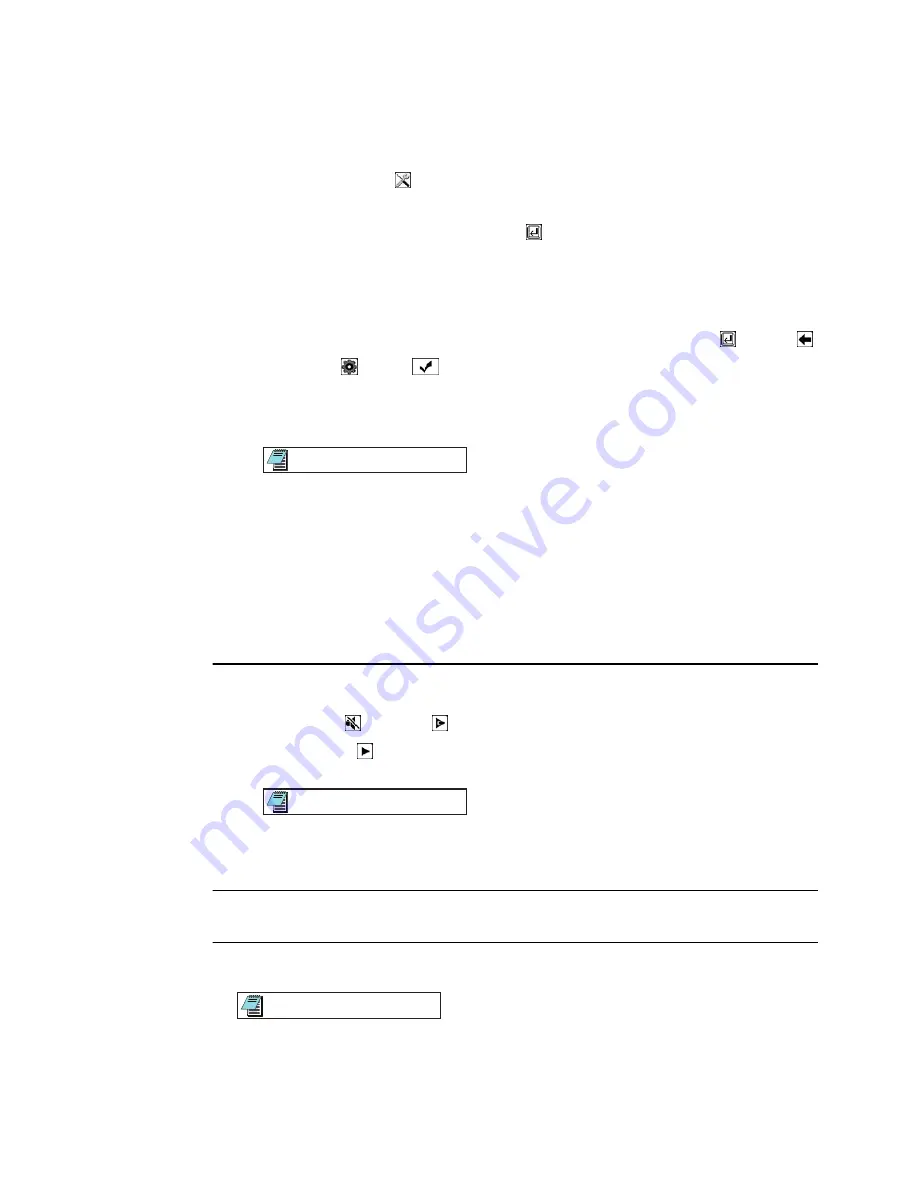
b. Perform this procedure from the Direct Track Sampling module control panel.
Select
Maintenance
on the control panel.
c. Select the number field to display the onscreen keyboard.
d. Enter function code
91
and select
Enter
twice to hold tubes at bar code reader
BR03 and to release tubes after bar code reader BR03. This ensures that the system
reads and registers the bar code IDs at BR03.
e. As the samples pass through the DTS sampling position make a note of the sample
ID numbers for later retrieval. See Note below.
f. After the system releases all tubes from BR03 and BR02, select
Enter
and
Exit
.
g. Select
Auto
and
OK
to resume operation.
h. Perform troubleshooting on the connected analyzer as necessary to re-establish
communication with the Direct Track Sampling module.
Note
The analyzer does not aspirate samples exiting the DTS connection. If the
analyzer is a dynamic analyzer (AU680, DxC 700 AU, or DxI), Cennexus
automatically recognizes that the analyzer has not aspirated the samples and
reroutes them to another analyzer for testing. If the analyzer is a non-dynamic
analyzer, the system considers aspiration to be complete, and you must
manually request retesting or retrieve samples using Cennexus for offline
testing.
i. Use the Cennexus retrieval function to manually collect the samples, or use the LIS
console to order retests on the samples noted in step e above.
20
If the Abbott i2000SR Direct Track Sampling module T-Lane generates a CCIE error
when you press the main track Stop button:
a. Select
Mute
and
Clear
on the control panel to clear the errors.
b. Select
Restart
on the control panel to resume operation.
Note
Pressing the main track Stop button does not affect the Abbott i2000SR,
because the Abbott i2000SR is on a separate power system, but doing so does
generate the CCIE error.
21
At the T-Lanes, if a stopper is jamming the sample tube carrier, push it forward to
release the carrier. Leave other tubes and sample tube carriers alone.
22
At the Aliquotter and Labeler components:
Note
Regardless of the status of the Aliquotter and Labeler, the recovery procedure is
the same.
Error Recovery Procedures
Power Express Aliquot Error Recovery Procedures
3
B31449AE
3-13
Summary of Contents for Power Express Aliquot
Page 6: ...Warranty and Service vi B31449AE...
Page 22: ...Introduction Scope of this Manual xxii B31449AE...
Page 30: ...Power Express Aliquot Module Description Components 1 8 B31449AE...
Page 110: ...Figure 4 3 Tube Supply Sensor Diagram 4 50 B31449AE Troubleshooting...
Page 111: ...Figure 4 4 Label Supply Sensor Diagram B31449AE 4 51 Troubleshooting...
Page 112: ...Aliquot Unit Figure 4 5 Overview Sensor Diagram 4 52 B31449AE Troubleshooting...
Page 114: ...Figure 4 7 Tip Supply Sensor Diagram 4 54 B31449AE Troubleshooting...
Page 117: ...Figure 4 10 Optional Track Sensor Diagram B31449AE 4 57 Troubleshooting...
Page 118: ...Figure 4 11 Merge Lane Sensor Diagram 4 58 B31449AE Troubleshooting...
Page 120: ...Related Documents Related Documents A 2 B31449AE...
Page 121: ......
Page 122: ...www beckmancoulter com 2018 Beckman Coulter Inc All Rights Reserved...