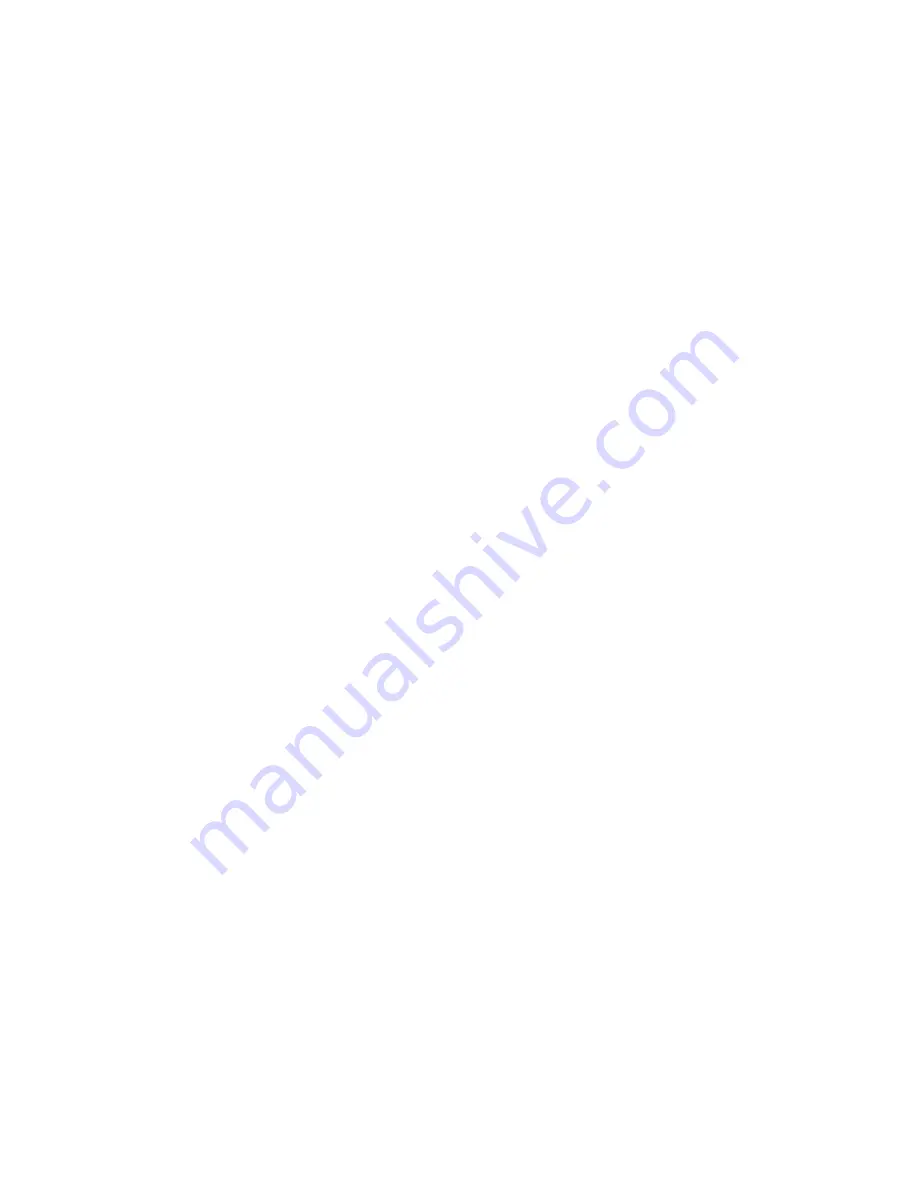
6-56 | Model 933S UV Analyzer
14. Close the Configurator Software, power down the computer, and
disconnect the serial cable from the analyzer’s Communications Port.
Close the Communications Port cover and hand-tighten the screw to
secure it in place.
15. Using a soft, nonabrasive cloth, gently clean the joining areas (flame-
path) of the Upper Enclosure and its door and replace the (24) M10
screws. Tighten the M10 screws to 9.0 Nm, ±1.0 Nm (80 in.-lb, ±9 in.-
lb).
The procedure is complete.
Summary of Contents for 933S
Page 24: ...1 8 Model 933S UV Analyzer This page intentionally left blank...
Page 34: ...2 10 Model 933S UV Analyzer...
Page 35: ...Specifications 2 11...
Page 36: ...2 12 Model 933S UV Analyzer 2016 12 16...
Page 37: ...Specifications 2 13...
Page 38: ...2 14 Model 933S UV Analyzer...
Page 39: ...Specifications 2 15...
Page 46: ...2 22 Model 933S UV Analyzer This page intentionally left blank...
Page 52: ...3 6 Model 933S UV Analyzer Figure 3 1 Analyzer backpan dimensions European...
Page 91: ...Installation and Start Up 3 45 Figure 3 24 Column Profile...
Page 94: ...3 48 Model 933S UV Analyzer This page intentionally left blank...
Page 176: ...5 12 Model 933S UV Analyzer This page intentionally left blank...
Page 190: ...6 14 Model 933S UV Analyzer Figure 6 3 1 Standard Range Cell 40 cm or smaller...
Page 191: ...Maintenance and Troubleshooting 6 15 Figure 6 3 2 Low Range White Cell 81 2 cm P N 100 1780 1A...
Page 197: ...Maintenance and Troubleshooting 6 21 Figure 6 4 Column Block assembly...
Page 246: ...6 70 Model 933S UV Analyzer Figure 6 18 Microcontroller board P N 100 1781 SW400...
Page 264: ...7 8 Model 933S UV Analyzer This page intentionally left blank...
Page 272: ...A 8 Model 933S UV Analyzer Lower Enclosure Layout WX 14838...
Page 274: ...A 10 Model 933S UV Analyzer RS 232 Communications Cable Connections 300 9480...
Page 279: ...Appendix A Drawings A 15 Optical Bench Board P N 100 1662...
Page 280: ...A 16 Model 933S UV Analyzer PMT Buffer Board 100 0140...
Page 288: ...S 2 Model 933S UV Analyzer This page intentionally left blank...