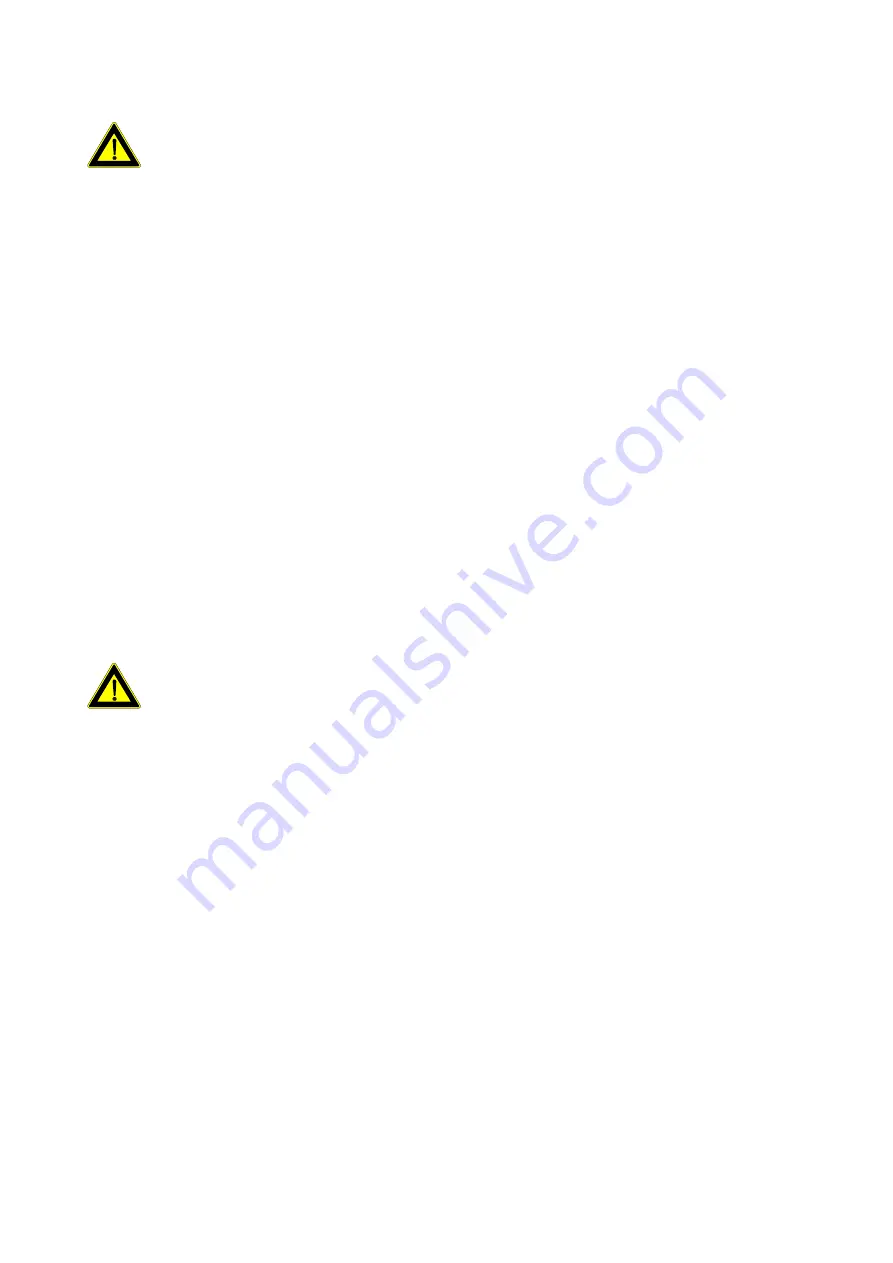
All information, illustrations and technical specifications in these operating instructions are based on the latest information available at the time of
publication. We reserve the right to make design changes at any time without prior notification.
46
7.0. Operation
7.1. General Information
ATTENTION:
The TERRA FLOAT operator is
responsible for persons
located inside the working
area.
Never operate the TERRA FLOAT
without its safety devices.
If you do operate the TERRA
SPIKE without safety devices,
you expose yourself and
others to extreme danger.
Always check the immediate
surroundings when starting to
drive (Caution - CHILDREN!).
Do not drive backwards when
the TERRA FLOAT is operating.
Avoid big changes in
direction while using
yielding tractors.
The equipment version with a
drawbar is
NOT
approved for
travel on public roads!
In the case of the equipment
version with a three-point
frame, the rear hydraulic
system of the tractor must
always be in the floating
position during operation.
7.2. Driving characteristics
CAUTION !
When the TERRA FLOAT has been
installed, this may have an
influence on the driving and
operational qualities of the
tractor.
Always adapt your driving
style to match the terrain
and ground conditions.
Special care should be taken
when working and turning on a
slope.
- DANGER OF TOPPLING !
A better result is obtained at
low speeds.
Do not make any sharp turns.