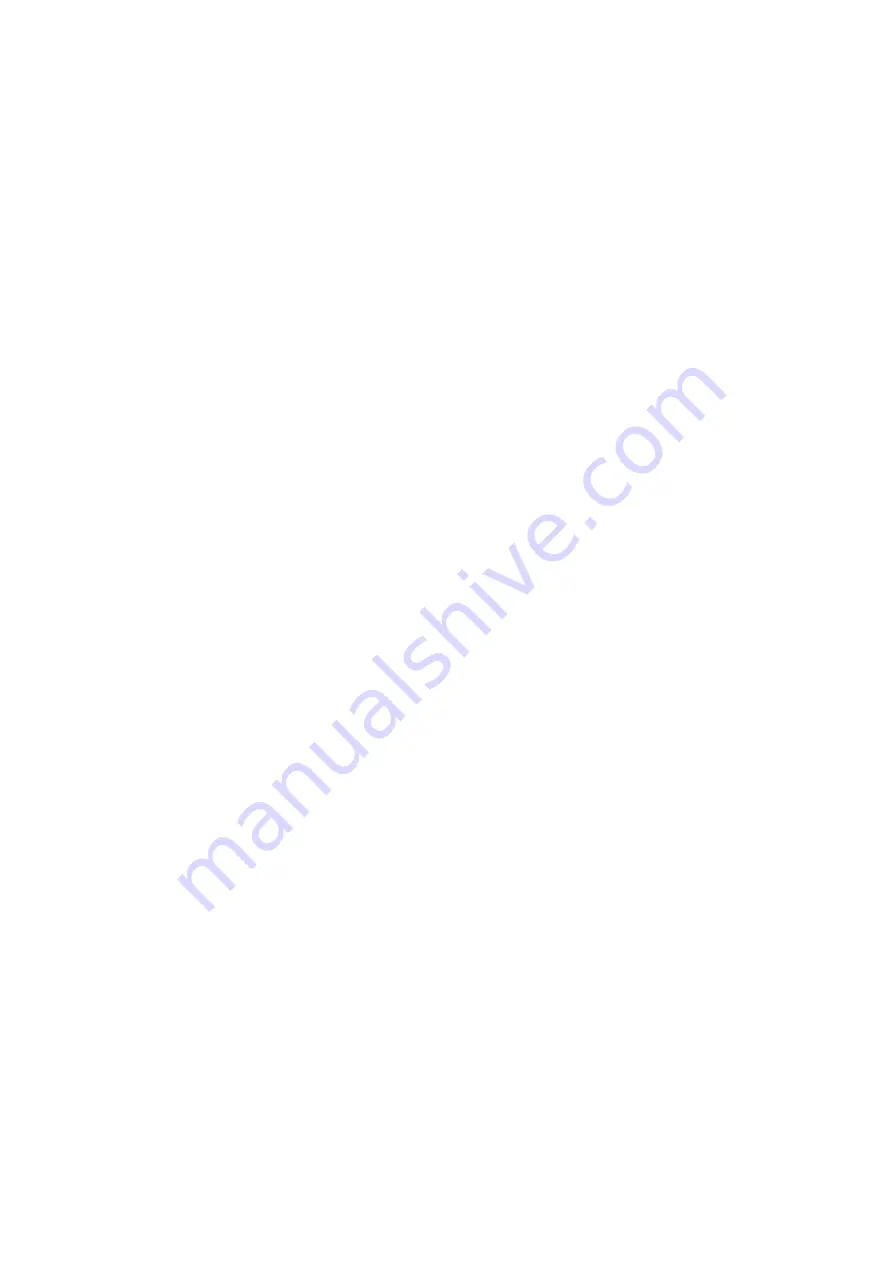
Technical Manual
1-2
It is possible to access the instrument, set-up and maintenance functions, remotely
over the Ethernet connection using a Web Browser on a connected PC.
It is possible to load new software into the instrument using the USB port.
All functions in the G4 Instrument are controlled by set-up parameters. Setting of
parameter values can be performed with
keys
and/or
graphical touch display
on
the front panel.
24 V DC or 110/230 V AC powers the G4 Instrument. All input and output signals
are galvanically isolated from the power supply by operational insulation.
Functions
Measurement with strain gauge transducers.
Both excitation voltage and output signal are measured at the transducer to avoid
influence from voltage drop in the connection cable. Excitation to the transducer, from
the G4 Instrument is provided over separate wires.
A shielded 6-wire cable must be used to connect a distant transducer to the instrument.
A/D conversion.
The analog signals from the transducer are converted to digital form and filtered
to give an internal transducer signal with high resolution.
Calculation.
The transducer excitation and signal values are combined to form an internal
transducer signal, representing the load on the transducer. Influenced by calibration
data, this signal is converted to a digital measurement value, the force value, which
can be presented at the local display window and at external equipment.
Error supervision.
As long as the error supervision detects no error, the signal ‘In process’ is present
but if an error is detected, ‘In process’ will be off and a specific error message will be
displayed. ‘In process’ can be set to control any digital output. Note that there are
force channel specific and instrument specific error detection.
Levels.
32 level comparators in the instrument can be set to switch at defined signal levels with
any selected hysteresis added, meaning that the switch level can be different for
increasing and decreasing signal. It’s possible to set level switching delays. Output
signals from these comparators are available on the serial communication. The level
comparator outputs can also be set to control digital outputs from the instrument.
Communication.
The G4 Instrument utilizes the serial interface, Ethernet and a fieldbus interface for
communication with control computer. The serial interface consists of a RS-232
(COM1) connection and a RS-485/RS-422 (COM2) connection. COM2 can be used
with 2- or 4-wire connection.
Force values, web tension values, level status, error status etc. can be collected and
commands given through the communication interfaces. Modbus RTU protocol is used
for the serial interfaces and Modbus TCP for the Ethernet connection. For the optional
fieldbus interface Profibus or DeviceNet can be used.
Содержание G4-DT
Страница 1: ...G4 Multi Channel Force Instrument Program version 101 1 0 0 Technical Manual PM DT HE types GB ...
Страница 2: ......
Страница 18: ...Technical Manual 1 14 ...
Страница 36: ...Technical Manual 2 18 ...
Страница 45: ...G4 Multi Channel Force Instrument 4 5 ...
Страница 76: ...Technical Manual 4 36 ...
Страница 82: ...Technical Manual 5 6 ...
Страница 92: ...Technical Manual 6 10 ...
Страница 138: ...Technical Manual 7 46 ...
Страница 158: ...Technical Manual 8 20 ...
Страница 164: ...Technical Manual 9 6 ...
Страница 170: ......
Страница 171: ...G4 Multi Channel Force Instrument Appendix 1 ...
Страница 172: ...Technical Manual ...
Страница 173: ......