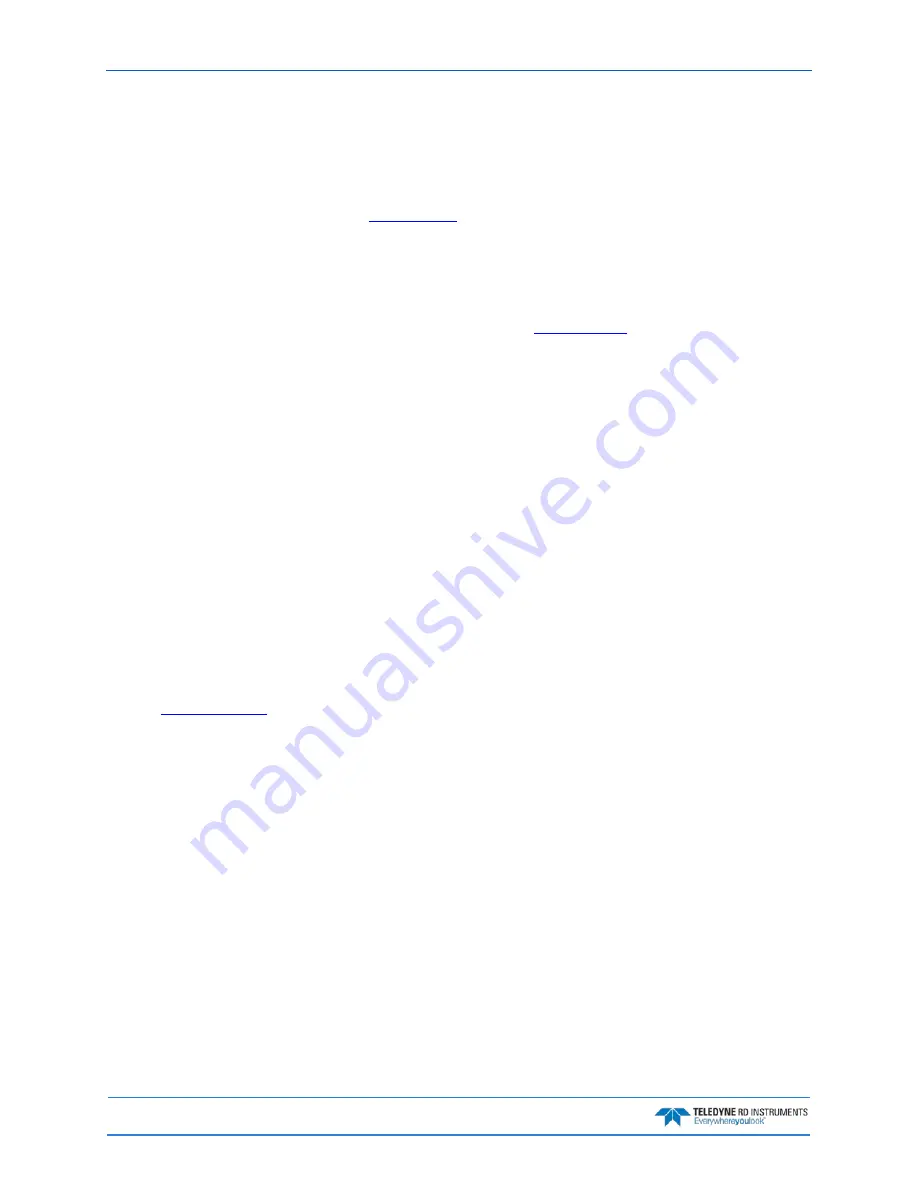
April
2018
Pathfinder DVL Guide
Page 50
EAR-Controlled Technology Subject to Restrictions Contained on the Cover Page.
Triggering
There are two methods for triggering the DVL:
Sending ASCII Character through Serial Port
.
When the system is interfaced to a serial port (e.g. a navigation
computer), the system can be setup to wait for an input before each ping. To setup the DVL in this fash-
ion, clear the Auto Ping Cycle bit in the
by sending CFx0xxx, where the x’s represent the set-
tings of the other parameters. Start the DVL pinging with the CS command. The DVL will output a ‘<’ be-
fore each ping and wait for input. Send any valid ASCII character to trigger the ping. The instrument will
not enter sleep mode while it is waiting for the trigger.
Using Low-Latency Triggering
. The trigger methods shown above all have latencies ranging from a few mil-
liseconds to a few hundred milliseconds, which may be excessive for high-precision applications. Conse-
quently, TRDI has developed a low-latency trigger method (see
). To configure the DVL
for low-latency triggering, set the CX command to enable trigger input. Start the DVL pinging with
the CS command. The DVL will then wait for a trigger before each ping. Setting the trigger lines to a
break state for no less than 10 microseconds sends the trigger. The DVL will then ping within 1 millisec-
ond of the leading edge of the break pulse. Note that it is possible through the CX command settings to
set a timeout for the DVL to wait for a Trigger and then shall no Trigger occur during that time it will ei-
ther Self Deploy and never look for Trigger again or Ping once and then go back to waiting for Trigger.
The input trigger voltage is 3.3VDC to 7VDC.
Design Considerations & Bench Test
To avoid problems when the DVL is installed in the final system, it is helpful to perform a bench test prior
to installation. In the bench test, the DVL should be exercised along with all the other components that
will be installed in the final system. By performing this initial bench test EMI and acoustic interference
issues can be identified and remedied while all the system components are easily accessible.
The recommended types of systems that should be bench tested are described below.
1. If possible, select components and systems that are acoustically, and RF wise “out of band”, based
on the specifications from the manufacturer of that equipment.
2. It is important to test for all EMI interference that may be occurring in the system. Bench test all
of the equipment in air, and see if there are interfering sources by using the FFT tool (refer to
for instructions on it use), after which you can plan the shielding and grounding
strategy.
3. Spread out the various systems and components that you intend to use on the bench in a pattern
similar to how they will work.
4. While observing the FFT use the DVL as a “probe” and pass the DVL over live components (in-
cluding hydraulic actuators) you intend to use in your design. Identify any unacceptable interfer-
ence.
5. While observing the FFT use the DVL as a “probe” and touch it against components or systems to
check their acoustic signature. Identify any unacceptable interference.
6. Try varying bench test temperatures, so it can be determined if there are tank circuits in your sys-
tem that “tunes into” our band, or visa-versa.