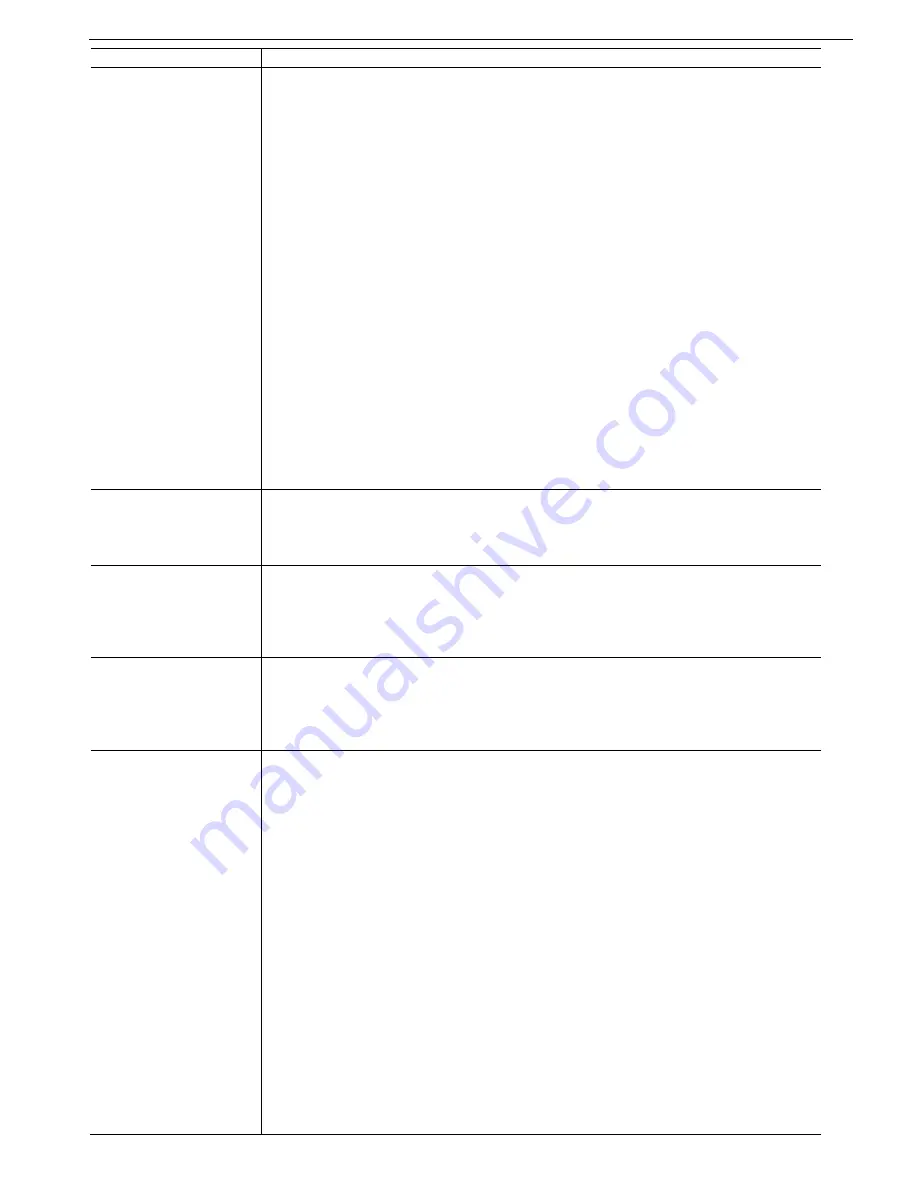
124 • Trouble Shooting
_____________________________________________________________________________________________
Problem
What To Do
UNDER/NO
VOLTAGE trip occurs
immediately after
starting.
Verify that all three mains phases are connected.
At low voltage, testing a missing phase can cause UNDER/NO VOLTAGE
trip.
Verify that the test harness is connected to the EPT-Tx while testing at low
voltage.
Verify that the Line Contactor is closed, at least for a short time, at the
beginning of the start process.
If external line (mains) contactor is used, ensure that its auxiliary contact is
wired back to the HRVS-DN cabinet and used (in series with RS relay
contact) to initiate the start command (this contact should not be bridged in
the customer terminals).
Check UNDERVOLT. TRIP setting level in MAIN & PROTECT page.
Verify that the Electronic Potential Transformer Receiver (EPT-Rx) fuse
located in the Receiver auxiliary supply plug is OK.
Verify that the fiber optics wires connecting the EPT-Tx and EPT-Rx are
properly connected.
Move the external mains connection from upstream of the Line Contactor to
down stream the Line Contactor and turn on the mains voltage . Check
120VAC line to line between EPT-Rx output terminals. Try to start now.
Take out fibers 11 and 13 from the EPT-Rx, they should emit red light with
the same intensity.
Check that the 15 pin white connector is properly connected, at the back of
the Control Module.
OVER VOLTAGE trip
occurs immediately
after starting.
Make sure that the mains testing voltage is 400V or as written as on the test
harness.
If it is higher, disconnect the mains voltage immediately.
Check OVERVOLT. TRIP setting level in MAIN & PROTECT page.
PHASE SEQUENCE
trip occurs
immediately after
starting.
Phase sequence of the mains lines is wrong.
Two options are available:
o
Swap two input lines.
o
Set PHASE SEQUENCE setting in FAULT PARAMETERS as
required.
TOO MANY STARTS
trip occurs
immediately after
starting.
The default setting allows for one start per 20 minutes.
To reset the fault find the NUMBER OF STARTS setting at the end of the
START PARAMETERS page, increase setting to OFF, then reset. Store at
the end of the page.
Be sure to set for medium voltage operation after end of testing.
S.SCR OR WR CON.
Trip occurs after
starting.
Verify that the motor’s rated current multiplied by the Gain (as set by the dip
switches) is greater than or equal to 30% of FLC.
It may occur when the load is not a motor.
Verify that fiber optic wires 1,3 & 5 are properly connected.
Verify that Current Gain dip switches are set equally for the three phases and
according to the ratio between starter rated current and testing motor rated
current.
Try to start using SOFT START CURVE 0, the basic curve. If the motor is not
loaded and has no inertia, the motor may vibrate after reaching full speed.
This is normal and will not occur with the MV motor.
o
If the test motor starts properly then the current transformers and their
wiring should be checked.
o
If the test motor does not start properly
the measured current may be
too low.
Perform a firing test as described on section
14.3 page 121.
Check fuses and fuses holders in phases firing power supplies. Refer to
section
10.2.4 page 93.
Sometimes SOFT START CURVE 0 enables the soft start process, even if a
CT or its wiring is problematic, if mains conditions are not ideal or with non-
standard motor. Current in every phase must, however be above 5% of
starter FLC, or the same trip might occur.