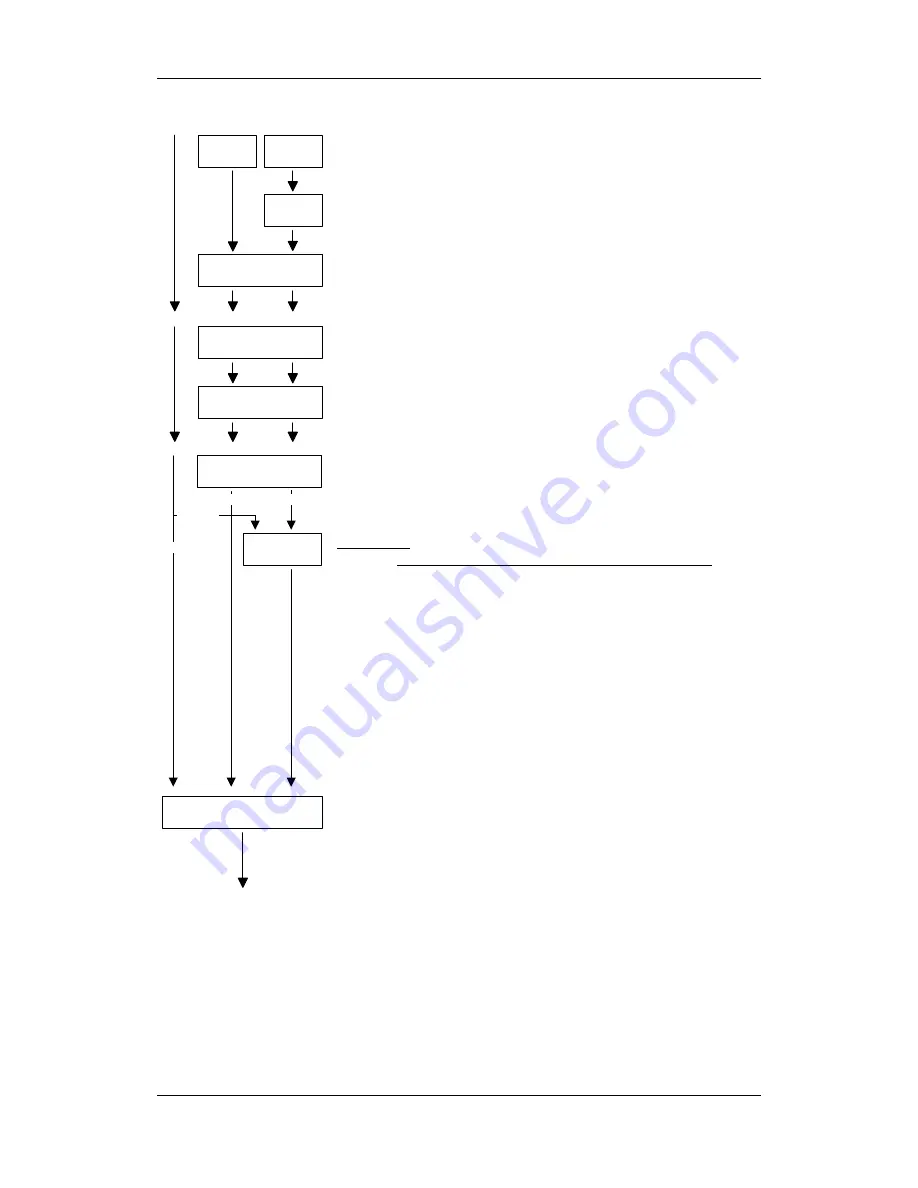
Parameterizing Steps
05.2006
6SE7087-2JD60 Siemens
AG
9-54
Operating Instructions
SIMOVERT MASTERDRIVES
P104=?
IEC motor: Cos (phi)
as per rating plate
NEMA motor: rated output [Hp]
(Group drives: total of all output ratings)
P105=?
NEMA motor: Enter the motor efficiency in %
as per rating plate
P106=?
P107 = ?
Enter the rated motor frequency in Hz
as per rating plate
P108 = ?
Enter the rated motor speed in rpm
as per rating plate
P109 = ?
Enter the motor pole pair number
(This is calculated automatically)
P113 = ?
Enter the rated motor torque in Nm
as per rating plate or motor catalog (this is only used for
normalizing the process data and visualization parameters)
P114 = ?
P100=0,1,2
P100 = 3,4,5
WARNING!
INCORRECT SETTINGS CAN BE DANGEROUS!
Process-related conditions for closed-loop control
0: Drive for standard applications (e.g. pumps)
1: Drive with strong torsion, gear play, large moments of inertia
(e.g. paper machine)
2: Drive for very dynamic accelerations (without load inertia)
(e.g. shears)
3: Drive for strong schock stressing (e.g. roll drive)
4: Drive with high smooth running characteristics at low speeds.
5: Drives with modest response requirements, which can be
optimized in their efficiency with frequent part-load operation.
6: Drive with high starting torque.
7: Dynamic torque response in field-weakening range
See next section for description
P100>2
P100=1,2
Calculate motor model for "Automatic parameterization"
Reference values P350 to P354 are set to the rated motor
values.
The motor parameters and controller settings are calculated.
P115 = 1