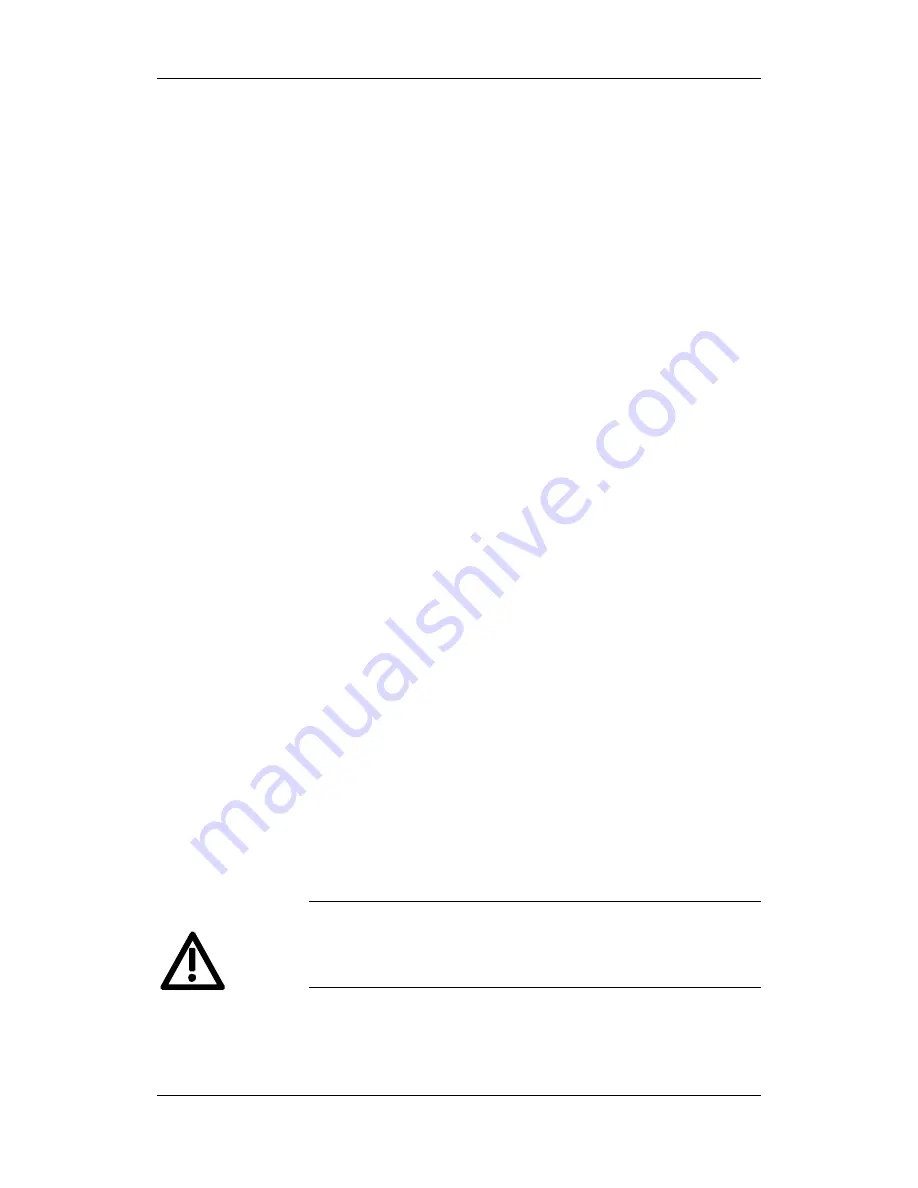
Parameterizing Steps
05.2006
6SE7087-2JD60 Siemens
AG
9-52
Operating Instructions
SIMOVERT MASTERDRIVES
♦
As the rated magnetizing current
P103
(not to be confused with the
no-load current during operation with rated frequency
P107
and
rated voltage
P101
) is usually not known, you can first enter 0.0 %.
With the aid of the power factor (cosPHI)
P104,
an approximate
value is calculated and displayed in
r119
.
Experience shows that the approximation supplies values which are
rather on the large side in the case of motors with a high rating (over
800 kW), whereas it supplies values which are slightly too low in the
case of motors with low rating (below 22 kW).
The magnetizing current is defined as a field-generating current
component during operation at the rated point of the machine
(U =
P101
, f =
P107
, n =
P108
, i =
P102
).
♦
The rated frequency
P107
and the rated speed
P108
automatically
result in the calculation of the pole pair number
P109
. If the
connected motor is designed as a generator and the generator data
are on the rating plate (oversynchronous rated speed), you have to
correct the pole pair number manually (increase by 1 if the motor is
at least 4-pole), so that the rated slip (
r110
) can be correctly
calculated.
♦
In the case of asynchronous motors, instead of the synchronous no-
load speed, enter the real motor rated speed in
P108
, i.e. the slip
frequency at nominal load has to be derived from parameters
P107...P109
.
♦
The rated motor slip (1 -
P108
/60 x
P109
/
P107
) should usually be
greater than 0.35 % x
P107
.
These low values are, however, only achieved in the case of motors
with a very high rating (above approx. 1000 kW).
Motors with average rating (45..800 kW) have slip values around
2.0...0.6 %.
Motors with low rating (below 22 kW) can also have slip values up to
10 %.
♦
It is possible to achieve a more accurate evaluation of the rated slip
after standstill measurement (
P115
= 2) by taking into account the
temperature evaluation for the rotor resistance
P127
.
On cold motors (approx. 20 °C), the value is usually around 70 %
(
±
10 %) and on warm motors (operating temperature) around
100 % (
±
10 %). If there are any large differences, you can proceed
on the assumption that the rated frequency
P107
or the rated speed
P108
do not correspond to the real values.
♦
If the rated motor frequency (engineered!) is below 8 Hz, you have
to set
P107
= 8.0Hz in the drive setting. The rated motor voltage
P101
has to be calculated in the ratio 8 Hz / f
Mot,N and the rated
motor speed
P108
should result in the same slip:
P108
= ((8 Hz -
P107
old) x 60 /
P109
) +
P108
old.
During motor identification (P115 = 2...7) inverter pulses are released
and the drive rotates!
For reasons of safety, identification should first be carried out without
coupling of the load.
WARNING