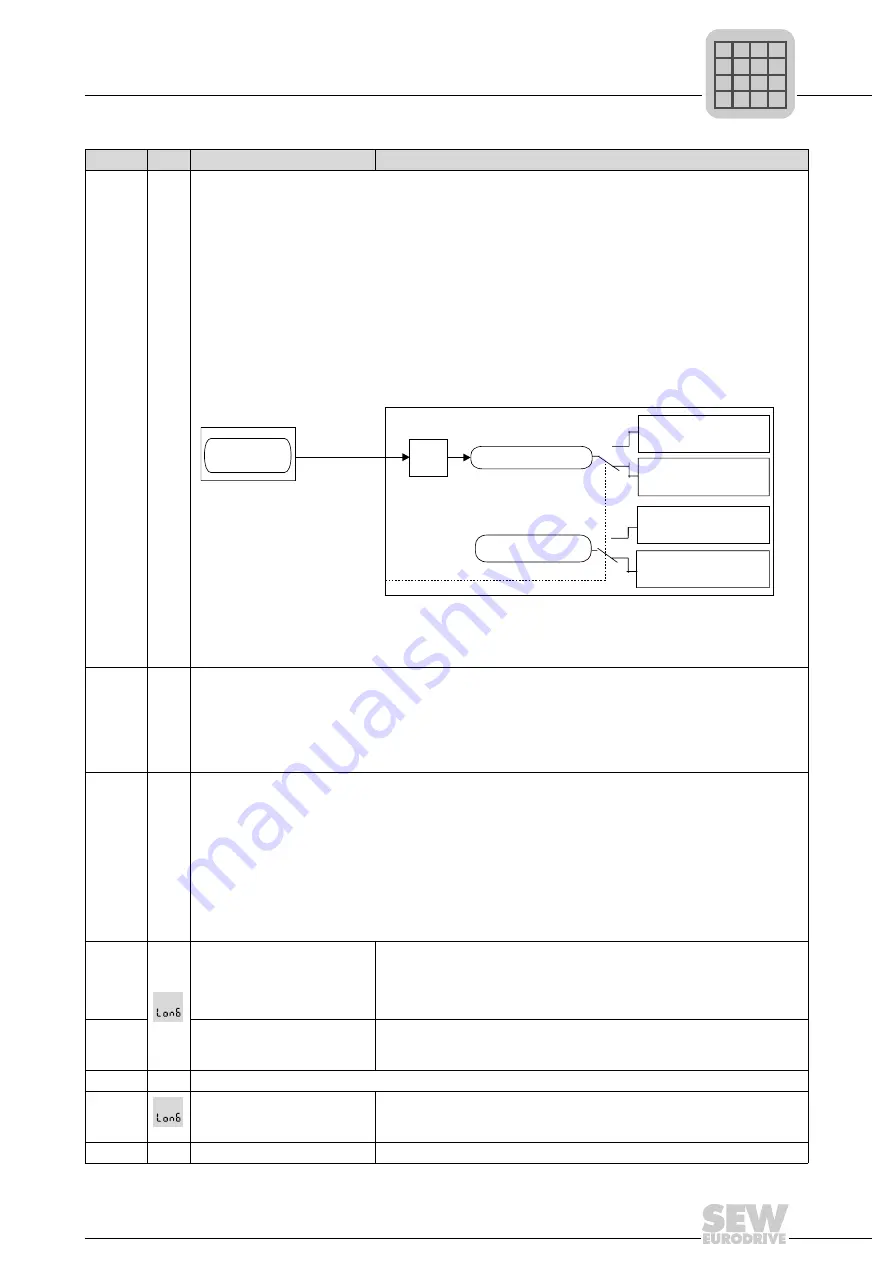
System Manual V2 – MOVITRAC® B
107
5
Explanation of the parameters
Parameters
75_
Master/slave function
(in preparation)
The master-slave function allows for implementing automatical functions such as speed synchronization, shared
load and torque control (slave). The RS-485 interface or the system bus interface can be used as the communica-
tion link. P100 "Setpoint source" must then be set to master SBus or master RS485. The process output data PO1
... PO3 (P870, P871, P872) are automatically set by the firmware. A programmable terminal function, "Slave free
runn." (P60_/P61_) makes it possible to separate the slave from the master setpoint of the master and switch it to
a local control mode (like control source bipolar/fixed setpoint).
For the slave, the process data P87x are automatically assigned as follows:
–
PO1 = Control word 1
–
PO2 = Speed or current in M-control
–
PO3 = IPOS PO data
–
PI1 = Status word 1
–
PI2 = Speed
–
PI3: IPOS PI data
P811 RS-485 Group address or P882 SBus Group address must be set to the same value in master and slave. For
master/slave operation via RS-485 interface, set P811 RS-485 Group address to a value greater than 100. For
operation via system bus (e.g. master/slave operation), the bus terminating resistors at the start and end of the
system bus must be activated.
Connection check
•
System bus (SBus): P883 SBus timeout interval is in effect when there is a communication link via the SBus. If
P883 SBus timeout interval = 0, there is no monitoring of data transmission via the SBus.
•
RS-485 interface: A connection check is always in effect if the communication link takes place via the RS-485
interface; P812 RS-485 timeout interval does not have any function. The slave inverter must receive a valid
RS-485 telegram within the fixed time interval of t = 500 ms. If the time is exceeded, the slave drives are
stopped at the emergency stop ramp and fault signal F43 "RS485 timeout" is issued.
Overview of functions of master/slave operation
Speed synchronization:
Master
Slave
Master controlled
P750 Slave setpoint:
P100 Setpoint source:
Slave controlled
SPEED (485+SBus)
MASTER SBus
P700 Operating mode 1:
MASTER RS485:
VFC
P700 Operating mode 1:
VFC & hoist
VFC
V/f characteristic curve
VFC & hoist
V/f & DC braking
V/f characteristic
V/f & DC braking
750
Slave setpoint
The setpoint to be transferred to the master is set on the master. The
"MASTER-SLAVE OFF" setting must be retained on the slave.
•
MASTER-SLAVE OFF
•
SPEED (RS485)
•
SPEED (SBus1)
751
Scaling slave setpoint
Setting range: –10 ...
0
... 1 ... 10
The setpoint sent from the master is multiplied by this factor which is set in the
slave.
76_
Manual operation
760
Locking RUN/STOP keys (see
Startup / External setpoint selec-
tion)
off / OFF
(RUN/STOP keys are activated and can be used for starting and
stopping the motor)
on / ON (RUN/STOP keys are locked and therefore do not function)
77_
Energy-saving function
No.
FBG
Name
Description
Master
RS-485 / SBus
Slave
0
1
0
1
= Master SBus
= Master RS-485
P751
Scaling
slave setpoint
P750
Slave setpoint
Slave free-running
P101 control source
P100 setpoint source
= Bipolar fixed setpoint /
fixed setpoint
If P100 = Master ,
Enable via master *
)
= Input terminals
P
i
f
kVA
Hz
n
Содержание MOVITRAC MC07B0037-2A3-4-00
Страница 250: ......