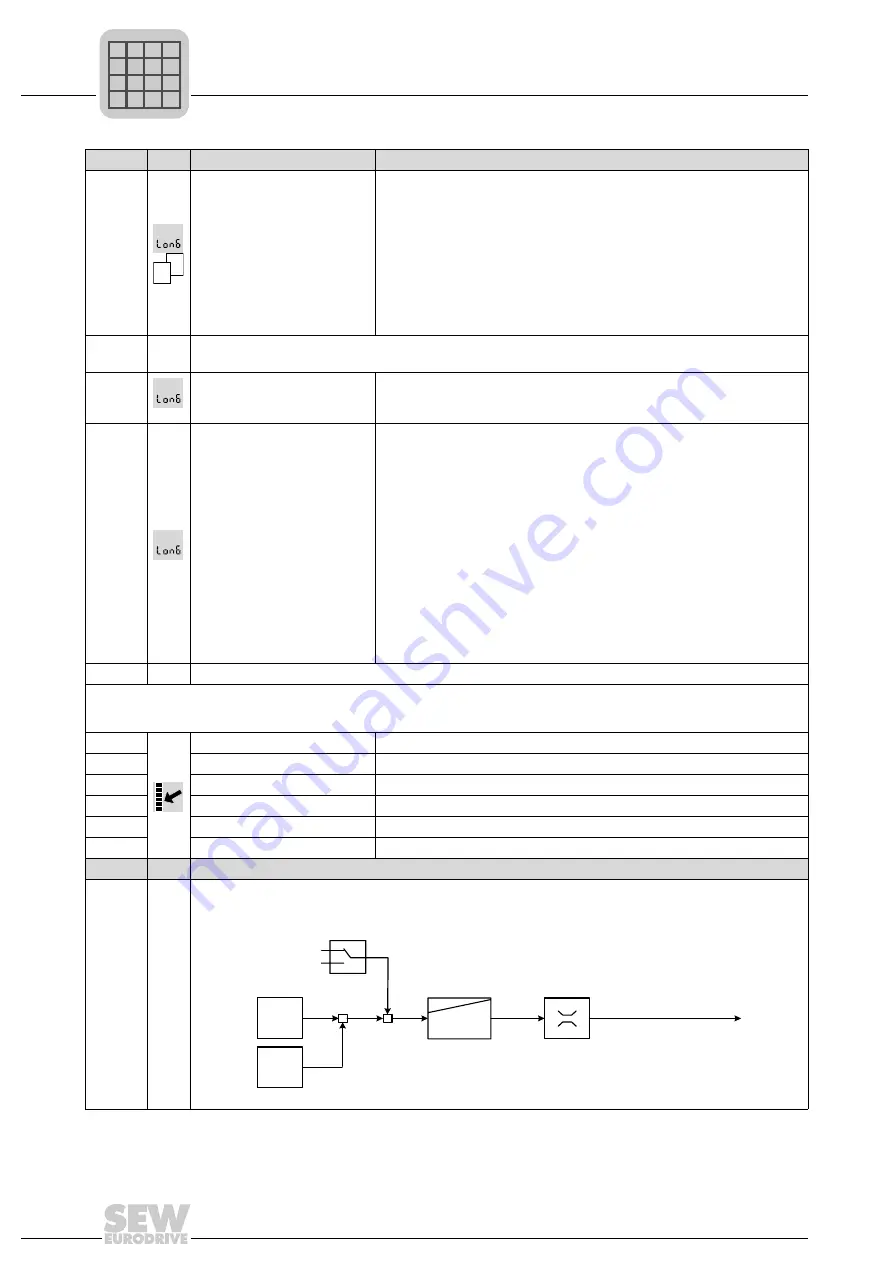
96
System Manual V2 – MOVITRAC® B
5
Explanation of the parameters
Parameters
139 / 149
Ramp monitoring 1 / 2
Setting range:
YES
/ NO
If you set the deceleration ramps to a value that is a lot shorter than can be
physically accomplished in this system, the turning drive will be stopped after
expiration of the monitoring time. Such a setting will cause a fault signal and
increase brake wear.
This step also entails an increased setting of the respective ramp, if the ramp
timeout definitely appears in form of a preset ramp that cannot be traveled.
This parameter is an additional monitoring function for speed monitoring. This
parameter only applies to the downwards ramp. This means the parameter can
be used to monitor the downwards ramp, stop ramp or emergency stop ramp if
speed monitoring is not desired.
15_
Motor potentiometer functionn
(se
P100 Setpoint source
)
The ramp times refer to a setpoint change of n = 3000 rpm.
150
Ramp t3 up = down
Setting range 0.2 ...
20
... 50 [s]
The ramp is in effect when using the terminal functions
Motor pot. up
and
Motor
pot. down
.
152
Save last setpoint
off / OFF
The inverter starts with n
min
:
•
After power off and on
•
After revoking ENABLE
If you use the motor potentiometer for permanent speed control, you will
have to set
P152 Save last setpoint to OFF
. Otherwise, error message F25
EEPROM will appear after about 100,000 storage operations.
Store only after setpoint change. If a fixed setpoint is deselected, the fixed
setpoint will be used as motor potentiometer value.
on / ON
The inverter starts with the last set motor potentiometer setpoint:
•
After power off and on
•
After revoking ENABLE
If a fixed setpoint is deselected, the old motor potentiometer setpoint will be
used again.
16_ / 17_
Fixed setpoints 1 / 2
You can activate the fixed setpoints via the binary inputs DI02 ... DI05 with the arguments n11/n21 / n12/n22 and activate FIXED SETP.
CHANGE (parameter 60_). You activate the fixed setpoints n13/n23 by assigning the functions n11/n21 and n12/n22 to two binary
inputs and applying a "1" signal to the two inputs.
160 / 170
Internal setpoint n11 / n21
Setting range –5000 ...
150
... 5000 [rpm]
161 / 171
Internal setpoint n12 / n22
Setting range –5000 ...
750
... 5000 [rpm]
162 / 172
Internal setpoint n13 / n23
Setting range –5000 ...
1500
... 5000 [rpm]
163 / 173
n11/n21 PI controller
Setting range 0 ...
3
... 100 [%] (see section Project planning / PI controller)
164 / 174
n12/n22 PI controller
Setting range 0 ...
15
... 100 [%] (see section Project planning / PI controller)
165 / 175
n13/n23 PI controller
Setting range 0 ...
30
... 100 [%] (see section Project planning / PI controller)
2__
Controller parameters
25_
PI controller
(for an explanation of the parameters, refer to the project planning/PI-controller section)
No.
FBG
Name
Description
1
2
Speed setpoint (value)
Actual
value
AI1 %
Setpoint
%
-1
1
n
max
n
min
P251 P-gain
P252 I-component
-
x
P250 PI controller
Normal
Inverted
Contr
ol diff
erence
Correcting
v
ariab
le
P301/311 n
max
P302/312 n
min
P
i
f
kVA
Hz
n
Содержание MOVITRAC MC07B0037-2A3-4-00
Страница 250: ......