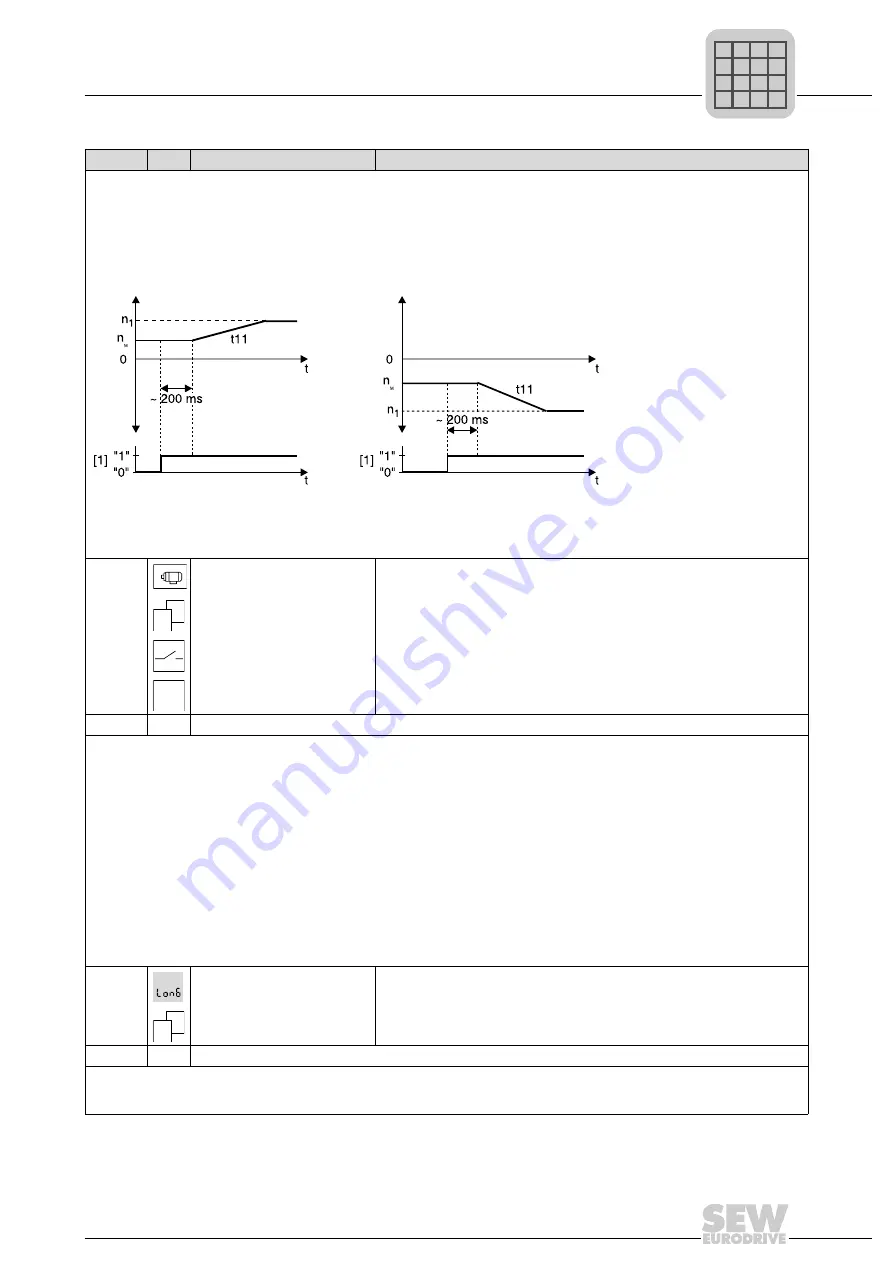
System Manual V2 – MOVITRAC® B
105
5
Explanation of the parameters
Parameters
VFC & flying start function
: The flying start function lets you synchronize the inverter to an already running motor. This is used in
particular with drives that are not braked actively, run on for a long time or are turned by a flowing medium, e.g. pumps and fans. The
maximum flying start time is approx. 200 ms.
P320 Automatic adjustment is deactivated in the FLYING START operating mode.
It is important that the IxR value P322 stator
resistance is set correctly to ensure that the flying start function is performed properly.
Startup of an SEW motor: The IxR value is set for an SEW motor at operating temperature. This value has to be reduced if flying start
takes place with a cold motor.
The IxR value is measured at startup when a non-SEW motor is started up with MOVITOOLS
®
MotionStudio.
n
1
= Setpoint speed
n
M
= Motor speed
[1] = Enable
The flying start function does not function if an output filter is connected to the inverter.
Caution!
Do not use the flying start function in hoist applications.
700 / 701
Operating mode 1 / 2
0 / VFC (field-oriented voltage flux control mode)
2 / VFC & hoist (field-oriented control mode for hoist applications, can only be
set in MOVITOOLS
®
MotionStudio)
3 / VFC & DC braking (field-oriented controlled mode with DC braking)
4 / VFC & flying start function (field-oriented control mode with flying start
function)
21 / V/f characteristic curve
(voltage/frequency controlled mode)
22 / V/f & DC braking (voltage/frequency controlled mode with DC braking)
71_
Standstill current 1 / 2
With activated standstill current function, the inverter injects a current in the motor at standstill. This allows the inverter to fulfill the
following functions:
•
When the ambient temperature of the motor is low, the standstill current prevents the risk of condensation and freezing (in
particular of the disc brake). Set the amount of current in such a way that the motor does not overheat.
Recommendation:
Motor
housing should be hand hot.
•
With activated standstill current, you can start the motor without premagnetization.
Recommendation:
For hoists, set to 45 ...
50 %.
You can activate the standstill current function by setting P710 = 0. Set the standstill current in % of the rated motor current. The stand-
still current cannot exceed the current limit (P303).
You can switch off the standstill current by setting /CONTROLLER INHIBIT to 0.
When the standstill current function is activated, the output stage remains enabled even in the "No enable" status to inject the motor
standstill current.
The standstill current is not switched off by pressing the stop/reset key.
You have to set the function of an input terminal to controller inhibit to activate the standstill current function. Else the output stage will
be energized directly.
710 / 711
Standstill current 1 / 2
0
... 50 % I
Mot
72_
Setpoint stop function 1 / 2
Use the
P720 / P723 Setpoint stop function
to enable the inverter automatically depending on the main setpoint. The inverter is
enabled with all the necessary functions, such as premagnetization and brake control. It is important that you also enable the drive via
terminals.
No.
FBG
Name
Description
1
2
AUTO
1
2
P
i
f
kVA
Hz
n
Содержание MOVITRAC MC07B0037-2A3-4-00
Страница 250: ......