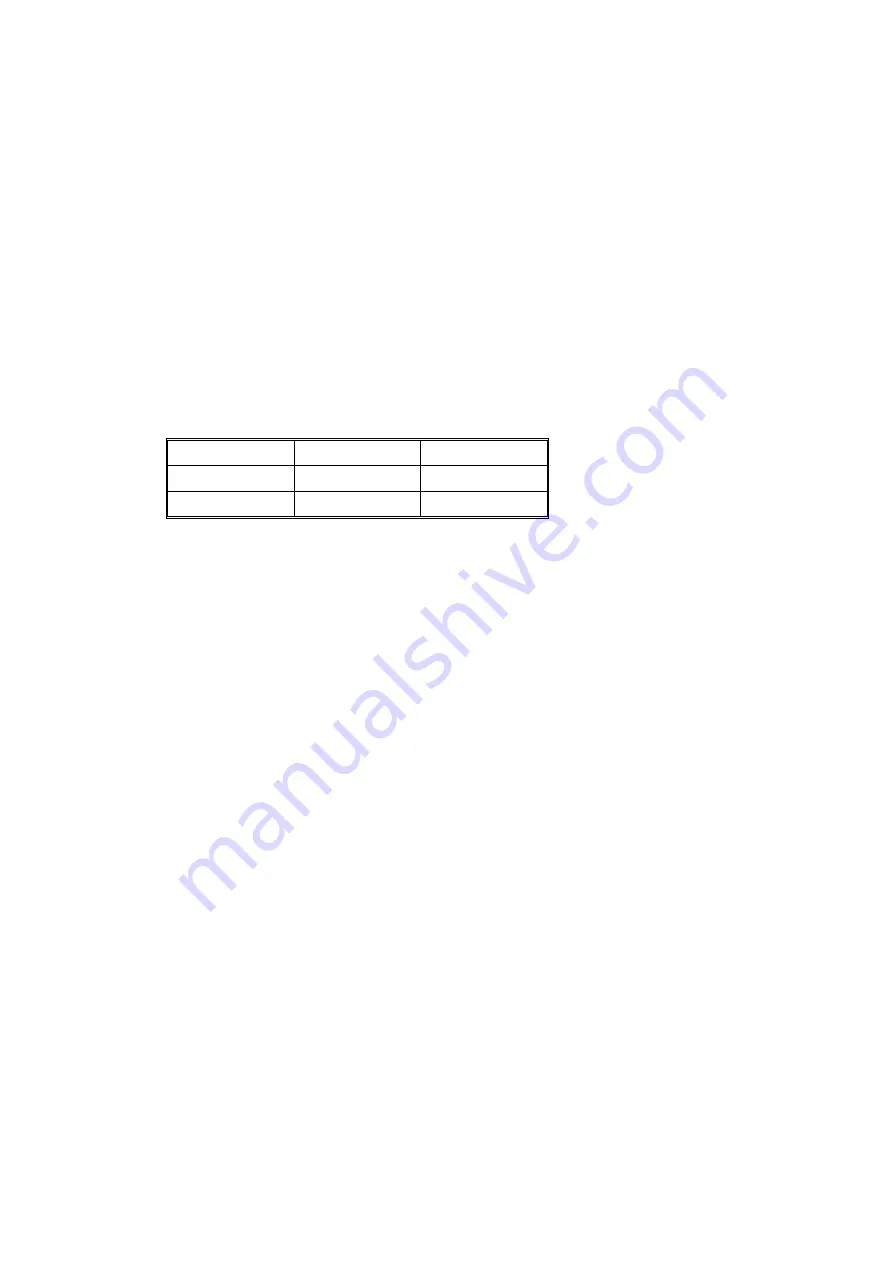
When the master feed clamper solenoid is de-energized, the drum starts
rotating forward (the printing direction) at 10 rpm to wrap the master
around the drum. The drum pulls the master and straightens out the
buckle. The drum stops when the buckle sensor is de-activated. Then the
master again buckles since the master feed motor keeps on feeding the
master. The master is wrapped around the drum by repeating these
steps, controlled by the ON/OFF action of the buckle sensor.
The original transport and master feed motors speed up once the master
plotting is done, so the master is now being wrapped more quickly. The
master feeding length for the plotting area is fixed at 410 millimeters
(maximum plotting length) in the standard A3/DLT drum (206 millimeters
in the A4/LT drum).
The master feed motor stops after the master is fed X1 and X2 millimeter.
X1 and X2 depend on the drum type as follows:
Drum Type
A3/DLT
A4/LT
X1 (mm)
410
206
X2 (mm)
60
61
T5: The drum (main motor) stops after the master has been fed 537
millimeters.
At the same time, the cutter motor starts rotating and the master is cut.
Then, the cutter motor changes the rotating direction when the cutter
holder pushes the right cutter switch. The cutter motor stops when the
cutter holder goes back to the home position and the left cutter switch is
again activated. (The pressure plate motor also starts turning to raise the
pressure plate at the same time.)
When the right cutter switch is activated, the drum starts rotating forward
at 30 rpm to go back to its home position. The drum keeps rotating
forward to make a trial print.
T6: When the left cutter switch is activated (the cutter home position) and the
cutter motor stops, the master feed motor again turns on to feed the
master 40 millimeters more, then turns off.
1 December 1993
2-37
Содержание VT3500
Страница 8: ...2 6 USER CODE MODE 4 27 2 6 1 User Codes 4 27 2 6 2 How To Use a User Code 4 27...
Страница 15: ...SECTION 1 OVERALL MACHINE INFORMATION...
Страница 19: ...2 GUIDETOCOMPONENTSANDTHEIRFUNCTION 1 2 3 4 5 6 7 8 9 10 11 12 13 14 15 1 December 1993 1 5...
Страница 21: ...16 17 18 19 20 21 22 23 24 25 26 27 28 1 December 1993 1 7...
Страница 37: ...SECTION 2 SECTIONAL DESCRIPTION...
Страница 89: ...E H D G F D C A B C I J K 1 December 1993 2 53...
Страница 123: ...1 December 1993 2 87...
Страница 127: ...1 December 1993 2 91...
Страница 161: ...Background Patterns The 40 background patterns shown below can be selected 1 2 3 4 5 6 7 8 9 1 December 1993 2 125...
Страница 162: ...13 14 15 16 17 18 10 11 12 1 December 1993 2 126...
Страница 163: ...19 20 21 22 23 24 25 26 27 1 December 1993 2 127...
Страница 164: ...28 29 30 31 32 33 34 35 36 1 December 1993 2 128...
Страница 165: ...37 38 39 40 1 December 1993 2 129...
Страница 192: ...SECTION 3 INSTALLATION...
Страница 206: ...SECTION 4 SERVICE TABLES...
Страница 209: ...Q Fig 4 R S Fig 5 T U Fig 6 V Fig 7 1 December 1993 4 3...
Страница 234: ...SECTION 5 REPLACEMENT AND ADJUSTMENT...
Страница 317: ...SECTION 6 TROUBLESHOOTING...