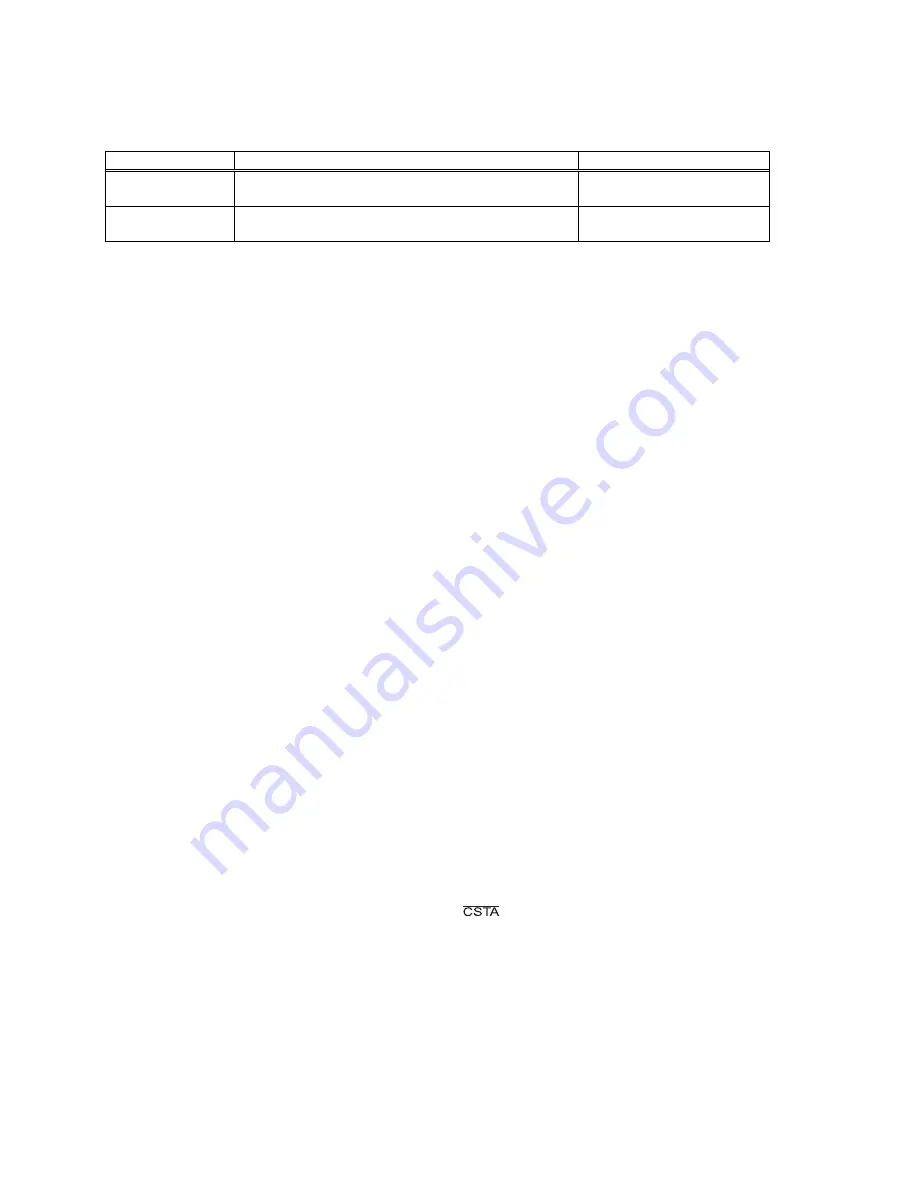
-
2
-
on
a
deceleration)
can
be
written
while
executing
the
current
data.
When
the
current
operation
is
complete,
the
system
will
immediately
execute
the
next
operation.
♦
A
variety
of
counter
circuits
The
following
four
counters
are
available
separately
for
each
axis.
Counter
Use
or
purpose
Counter
Input/Output
COUNTER1
28-bit
counter
for
control
of
the
command
position Outputs
pulses,
EA/EB
input
COUNTER2
28-bit
counter
for
mechanical
position
control
Outputs
pulses,
EA/EB
input
Both
of
them
can
also
be
latched
by
writing
a
command,
or
by
providing
an
LTC,
or
ORG
signal.
The
PCLs
can
also
be
set
to
reset
automatically
soon
after
latching
these
signals.
♦
Comparator
There
are
2
comparator
circuits
for
each
axis.
They
can
be
used
to
compare
target
values
and
internal
counter
values.
Comparator
1
can
be
compared
with
COUNTER1
and
Comparator
2
can
be
compared
with
COUNTER2.
♦
Simultaneous
start
function
Multiple
axes
controlled
by
the
same
LSI,
or
controlled
by
multiple
sets
of
this
LSI,
can
be
started
at
the
same
time.
♦
Simultaneous
stop
function
Multiple
axes
controlled
by
the
same
LSI,
or
controlled
by
multiple
sets
of
this
LSI,
can
be
stopped
at
the
same
time
by
a
command,
by
an
external
signal,
or
by
an
error
stop
on
any
axis.
♦
Manual
pulsar
input
function
By
applying
manual
pulse
signals,
you
can
rotate
a
motor
directly.
The
input
signals
can
be
90
˚ phase difference signals (1x, 2x, or 4x) or up and down signals.
When
an
EL
signal
of
the
feed
direction
is
input,
the
PCL
stops
the
output
of
pulses.
But,
it
can
feed
in
the
opposite
direction
without
any
command.
♦
Direct
input
of
operation
switch
An
input
terminal
for
operation
switch
is
provided
to
directly
drive
a
motor
with
an
external
operation
switch.
These
switches
turn
the
motor
forward
(+)
and
backward
(-).
The
results
of
a
switch
press
can
be
set
to
keep
feeding
pulses
while
pressed
down,
or
to
feed
a
single,
specified
number
of
pulses
for
each
press
of
the
switch.
♦
Operation
mode
The
basic
operations
of
this
LSI
are:
continuous
operation,
positioning,
zero
return,
and
linear
interpolation.
By
setting
the
optional
operation
mode
bits,
you
can
use
a
variety
of
operations.
<Examples
of
the
operation
modes>
1)
Start/stop
by
command.
2)
Continuous
operation
and
positioning
operation
using
a
manual
pulsar.
3)
Single-shot
or
continuous
operation
using
the
drive
switch.
4)
Zero
return
operation.
5)
Positioning
operation
using
commands.
6)
Hardware
start
of
the
positioning
operation
using
input.
7)
Feed
for
a
specified
amount
after
turning
ON
the
PCS.
(Position
override
(2))
♦
Zero
return
sequences
1)
Feeds
at
low
speed
and
stops
when
the
ORG
signal
is
turned
ON
2)
Feeds
at
low
speed
and
stops
when
an
EZ
signal
is
received
(after
the
ORG
signal
is
turned
ON).
3)
Feeds
at
high
speed,
decelerates
when
the
SD
signal
is
turned
ON,
and
stops
when
the
ORG
signal
is
turned
ON.
4)
Feeds
at
high
speed,
decelerates,
and
stops
when
the
ORG
signal
is
turned
ON.
5)
Feeds
at
high
speed,
starts
deceleration
when
the
ORG
signal
is
turned
ON.
Then,
it
stops
when
an
Содержание PCL6113
Страница 1: ...User s Manual For PCL6113 6123 6143 Pulse Control LSI Nippon Pulse Motor Co Ltd...
Страница 11: ...5 3 Terminal Assignment Diagram 3 1 PCL6113 3 2 PCL6123...
Страница 20: ...14 5 Block Diagram...
Страница 115: ...109 11 Stop timing by error...
Страница 116: ...110 13 External Dimensions 13 1 PCL6113...
Страница 117: ...111 13 2 PCL6123...
Страница 118: ...112 13 3 PCL6143...