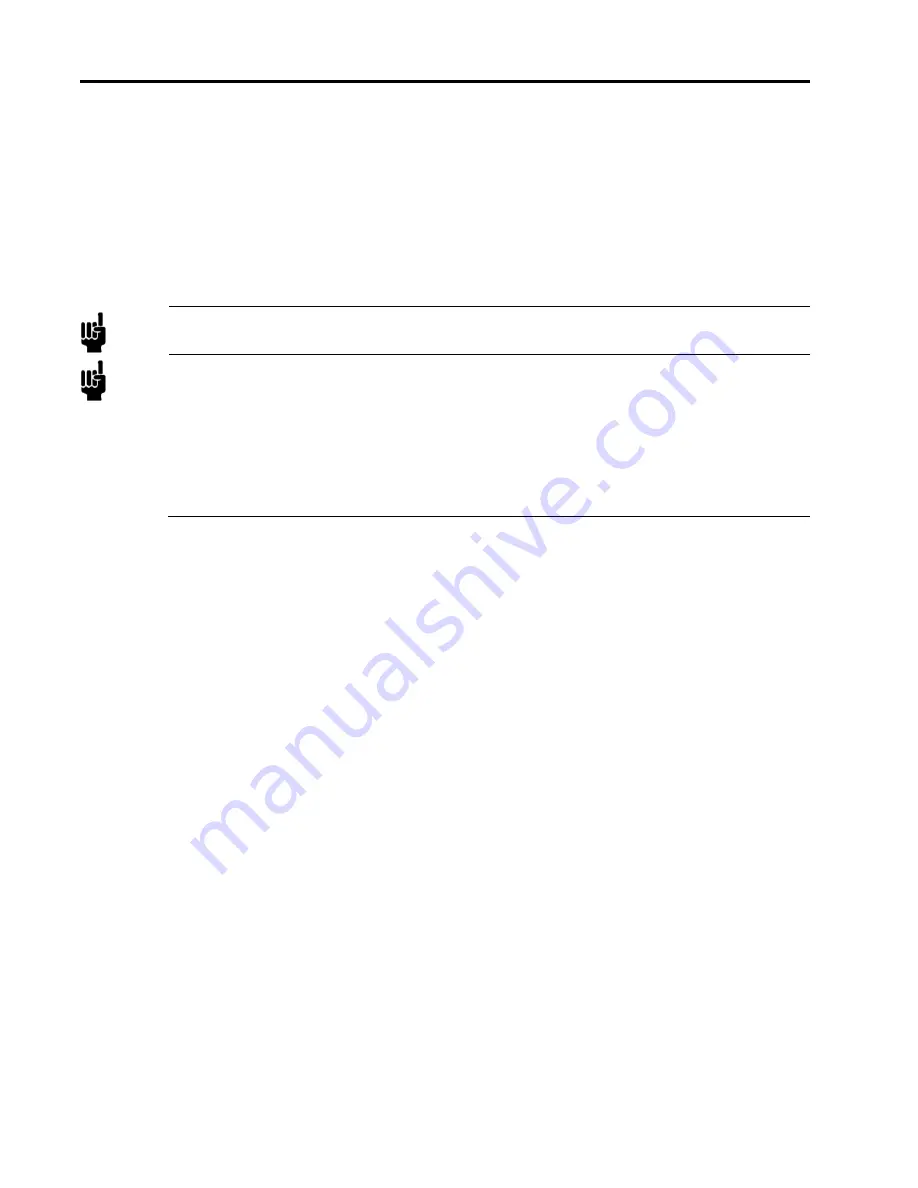
Chapter Four: Analog and Digital Interface
Analog Interface Input and Output Options
38
The Optional Input (15 Pin D Analog Controllers Only)
The standard 15-pin MFC can control flow based on a 0 to 5 Volt (or 0 to 10 VDC) signal from an external
sensing device using the optional input feature. A common application of this feature is for pressure control
using input from a pressure transducer. Configuring the device to use the optional input feature is done using
the embedded Ethernet User Interface. Refer to Chapter 6 for additional information on the configuration and
use of the option input.
To use the optional input feature, route the 0-5 Volt output from the desired external device to the optional
input pin 10.
Note
The Optional Input feature of the device is enabled using the Ethernet User Interface in the
Setup Mode. See Chapter 6 for further details.
Note
The optional input feature is only available on the 15-pin Type D connector with standard MKS
pinout assignments. The 9-pin Type D connector does not support the optional input feature.
Voltage applied to the optional input pin overrides the signal generated by the flow sensor
internal to the MFC. The control electronics drives the valve so that the optional input signal
matches the setpoint. Use the same pin for the setpoint signal, regardless of whether you are
using the optional input or the standard flow control signal. Although controlling to the external
optional input signal, the metered flow output signal is still provided on the standard output pin
2.
Start-Up Procedure for the Analog MFC
1.
Leak test the fittings on the unit using standard helium leak check procedures. Do not proceed to the
next step until you are certain that there is no gas leakage.
2.
Before connecting the cable leading to the MFC, verify all pinouts for power and signals match those
for the connector being used.
3.
Plug the power supply/readout cable (MKS or customer-supplied) into the connector (either a 9-pin or
15-pin D type) located at the inlet end of the device.
4.
Plug the other end of the cable into an MKS or MKS-compatible power supply/readout unit.
5.
Apply power to the device. Once the device is sufficiently warmed-up, you can proceed to zero it.
See instructions in Chapter 7 for instructions on the zero procedure.
Warm Up Time
After installation and power connection, allow the MKS MFC to warm up for a minimum of 30 minutes.
This is to account for both warm-up of the device electronics as well as for the device to reach ambient
temperature conditions.
Zeroing the Device
Although MKS flow devices are zeroed at the factory prior to shipment, it is normal to check the zero and re-
zero them, if needed, when they are first installed on the tool.
A mass flow meter or mass flow device will provide a zero output signal under no flow gas conditions.
Zero offset from improper zeroing procedures can contribute to flow measurement inaccuracy. This is more
apparent at the lower end of the device flow range.
Содержание P9B
Страница 1: ...1042936 001 Rev A January 2013 MKS Type P9B Digital Mass Flow Controller Instruction Manual...
Страница 4: ......
Страница 10: ...List of References vi This page intentionally left blank...
Страница 20: ......
Страница 22: ...12...
Страница 23: ...13 MKS Instruments Inc MKS Calibration and Service Center...
Страница 24: ...14...
Страница 26: ...16 MKS Instruments Inc MKS MKS Calibration and Service Center...
Страница 27: ...17...
Страница 28: ...18...
Страница 32: ......
Страница 56: ...Chapter Four Analog and Digital Interface Digital Interface Input and Output Options 46...
Страница 64: ......
Страница 68: ...Chapter Five Ethernet Interface Setup and Configuration Digital Interface Input and Output Options 58...
Страница 86: ...Chapter Six Embedded Web Based GUI and Diagnostics Tuning the MFC for Optional PC 76...
Страница 92: ...Chapter Seven Maintenance Pressure Zero Adjustment 82 This page intentionally left blank...
Страница 99: ...Troubleshooting Chart Chapter Eight Troubleshooting 89 This page intentionally left blank...
Страница 100: ......
Страница 105: ...Appendix A Product Specifications Electrical Specifications 95...
Страница 111: ...Model Code Description 101...
Страница 112: ...Model Code Description Appendix C Health and Safety Form 102 Appendix C Health and Safety Form...