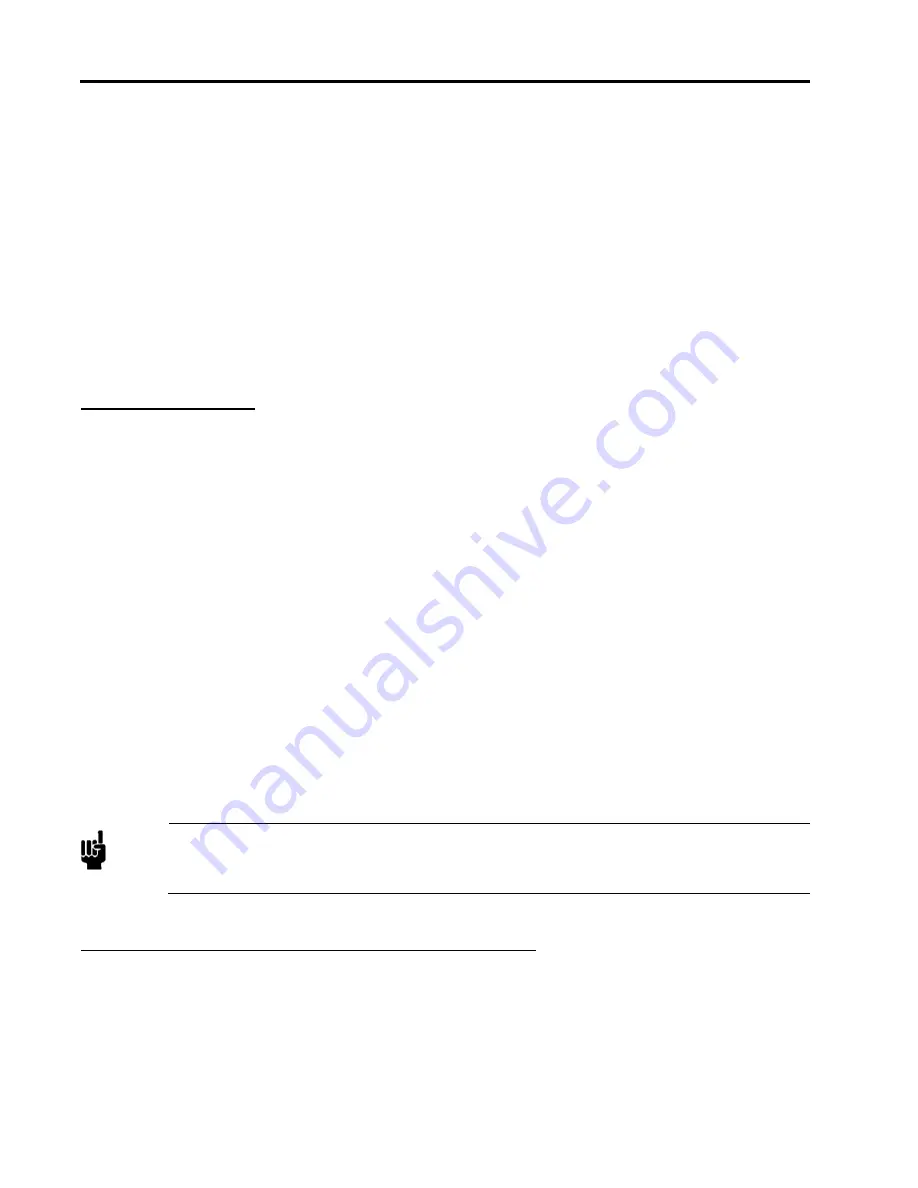
Chapter Two: Overview
How the MFC Works
24
Control Circuitry
The controller employs the above thermal flow measurement technique along with the pressure and utilizes a
control circuit that provides drive current for the proportioning control valve. The flow controller accepts a
setpoint signal, compares it to its own flow signal, and generates an error voltage. This error signal is then
conditioned so that it can reposition the control valve, thus reducing the control error to zero.
In the normally closed control valve, the MFC instrument lifts the armature and plug assembly from the seat
to regulate the gas flow rate. In the normally open valve, full valve current is applied when there is not an
active setpoint which closes the valve so long as there is power to the device.
Control Valve
The control valve is a specially constructed solenoid valve in which the armature (moving valve mechanism)
is suspended. The arrangement ensures that no friction is present and makes precise control possible.
How the MFC Works
The MKS MFC includes technology improvements in functionality and performance to help users in
semiconductors increase tool throughput and reduce overall system costs. Real-time accurate flow control is
provided through advanced digital algorithms. Enabling real-time control of process gas flow, accuracy and
repeatability are significantly improved over conventional PID based digital MFC’s. For optimum control
performance, the device utilizes pressure sensing in addition to the flow sensing and dynamically adjusts
control accordingly.
The MFC compares the flow reading to the setpoint, and positions the valve to maintain, or achieve, the
setpoint rate. The controller functions as a model based, pressure insensitive flow controller.
Example
Assume that your MFC is positioned upstream of the process chamber. The MFC is positioned
before
the
chamber so it will regulate the flow rate of the gas entering the process chamber.
When the actual flow rate reading is
less than
the setpoint value, the MFC opens the valve to increase the
amount of gas entering the system. As the valve opens, assuming adequate differential pressure across the
flow controller, gas enters the process chamber, so the flow rate rises to meet the setpoint value.
When the actual flow rate reading is
more than
the setpoint value, the MFC closes the valve to decrease the
amount of gas entering the system. As the valve closes, there is a reduced flow of gas entering the process
chamber, so the flow rate decreases to meet the setpoint value.
Note
The MFC must have sufficient differential pressure from inlet to outlet to achieve the setpoint.
If the device does not reach setpoint for lack of differential pressure, either increasing the inlet
pressure or decreasing the outlet pressure may be necessary.
Operation of the MFC with Gases other than Nitrogen
The P9B MFC does not use gas correction factors as many other mass flow controllers do. The operation of
the P9B MFC is based on thermodynamic principals and multi-component functions have been developed to
accurately calculate the non-linear gas flow of non-calibration gases, with respect to the calibration gas. The
current MKS library of gases and functions is in excess of 50 in number and includes most gases in common
usage. For gases whose parameters that are not already stored on the MFC, consult MKS.
Содержание P9B
Страница 1: ...1042936 001 Rev A January 2013 MKS Type P9B Digital Mass Flow Controller Instruction Manual...
Страница 4: ......
Страница 10: ...List of References vi This page intentionally left blank...
Страница 20: ......
Страница 22: ...12...
Страница 23: ...13 MKS Instruments Inc MKS Calibration and Service Center...
Страница 24: ...14...
Страница 26: ...16 MKS Instruments Inc MKS MKS Calibration and Service Center...
Страница 27: ...17...
Страница 28: ...18...
Страница 32: ......
Страница 56: ...Chapter Four Analog and Digital Interface Digital Interface Input and Output Options 46...
Страница 64: ......
Страница 68: ...Chapter Five Ethernet Interface Setup and Configuration Digital Interface Input and Output Options 58...
Страница 86: ...Chapter Six Embedded Web Based GUI and Diagnostics Tuning the MFC for Optional PC 76...
Страница 92: ...Chapter Seven Maintenance Pressure Zero Adjustment 82 This page intentionally left blank...
Страница 99: ...Troubleshooting Chart Chapter Eight Troubleshooting 89 This page intentionally left blank...
Страница 100: ......
Страница 105: ...Appendix A Product Specifications Electrical Specifications 95...
Страница 111: ...Model Code Description 101...
Страница 112: ...Model Code Description Appendix C Health and Safety Form 102 Appendix C Health and Safety Form...