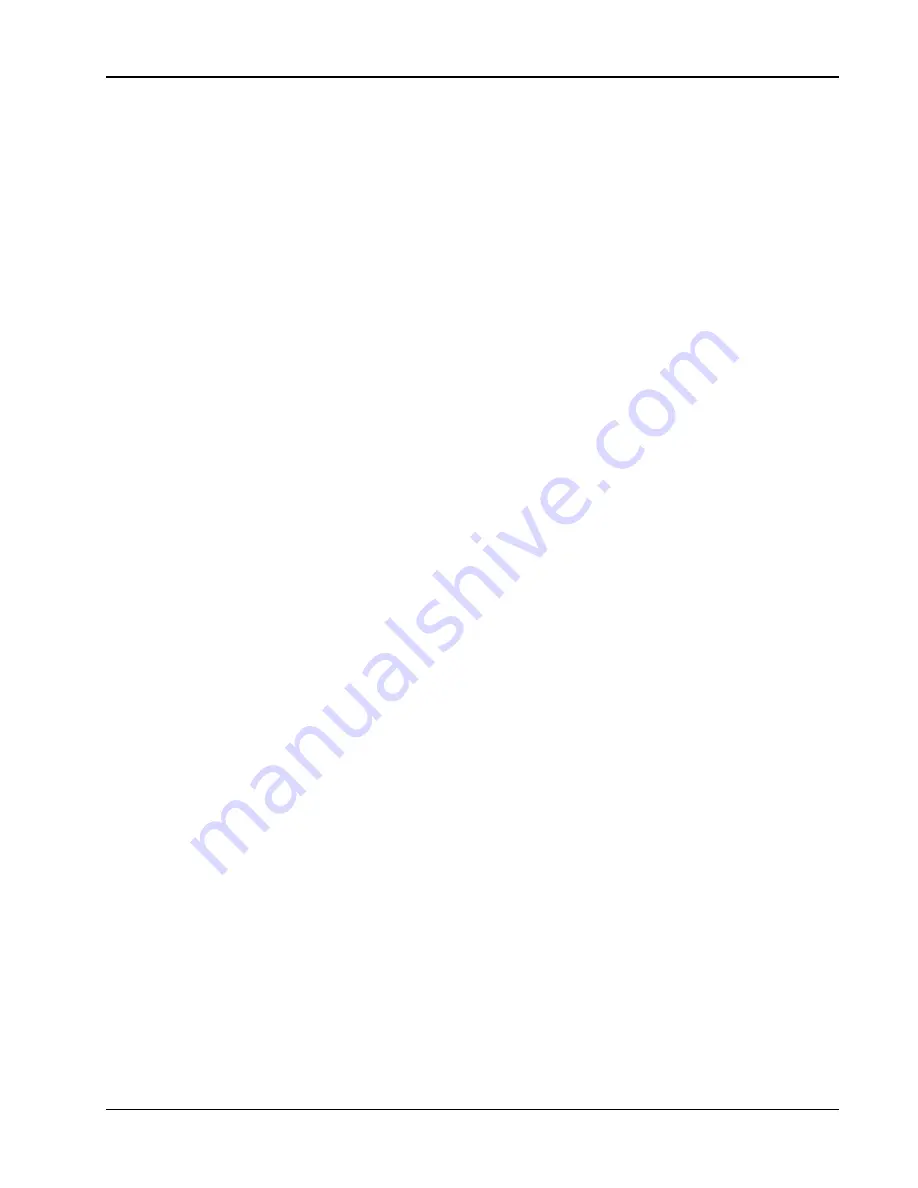
Lake Shore Model 370 AC Resistance Bridge User’s Manual
2.9.3.4 Contact
Area
Thermal contact area greatly affects thermal conduction because a larger area has more opportunity to transfer heat. Even
when the size of a sensor package is fixed, thermal contact area can be improved with the use of a gasket material. A soft
gasket material forms into the rough mating surface to increase the area of the two surfaces that are in contact. Good
gasket materials are soft, thin, and have good thermal conductivity. They must also withstand the environmental
extremes. Indium foil (when not super conducting) and cryogenic grease are good examples.
2.9.3.5 Contact
Pressure
When sensors are permanently mounted, the solder or epoxy used to hold the sensor act as both gasket and adhesive.
Permanent mounting is not a good solution for everyone because it limits flexibility and can potentially damage sensors.
Much care should be taken not to over heat or mechanically stress sensor packages. Less permanent mountings require
some pressure to hold the sensor to its mounting surface. Pressure greatly improves the thermal resistance of joints and
reduces thermal gradients. A spring clamp is recommended so that different rates of thermal expansion do not increase or
decrease pressure with temperature change.
2.9.3.6 Lead
Wire
Different types of sensors come with different types and lengths of electrical leads. In general a significant length of lead
wire must be added to the sensor for proper heat sinking and connecting to a bulk head connector at the vacuum
boundary. The lead wire must be an electrical conductor, but should not be a good
thermal
conductor, or heat will
transfer down the leads and change the temperature reading of the sensor. Small 30 to 40 AWG wire made of an alloy
like Manganin or phosphor bronze is much better than copper wire. Super conducting wire is a good choice if wire
temperature remains below the transition temperature. Thin wire insulation is preferred for better heat sinking. Twisted
wire is recommended if electrical noise is present. The wire used on the room temperature side of the vacuum boundary
is not critical so shielded copper cable is normally used.
2.9.3.7 Lead
Soldering
When additional wire is soldered to short sensor leads, care must be taken not to overheat the sensor. A heat sink such as
a metal wire clamp or alligator clip will heat sink the leads and protect the sensor. Lead wires should be tinned before
bonding to reduce the time that heat is applied to the sensor lead. Solder flux should be cleaned after soldering to prevent
corrosion.
2.9.3.8 Heat
Sinking
Leads
Sensor leads can be a significant source of error if they are not properly heat sinked. Heat will transfer down even small
leads and alter the sensor reading. The goal of heat sinking is to cool the leads to a temperature as close to the sensor as
possible. This can be accomplished by putting a significant length of lead wire in thermal contact with every cooled
surface between room temperature and the sensor. Lead wires can be adhered to cold surfaces with varnish over a thin
electrical insulator like cigarette paper. They can also be wound onto a bobbin that is firmly attached to the cold surface.
Some sensor packages include a heat sink bobbin and wrapped lead wires to simplify heat sinking.
2.9.3.9 Thermal
Radiation
Thermal (black body) radiation is one of the ways heat is transferred. Warm surfaces radiate heat to cold surfaces even
through a vacuum. The difference in temperature between the surfaces is one thing that determines how much heat is
transferred. Thermal radiation causes thermal gradients and reduces measurement accuracy. Many cooling systems
include a radiation shield. The purpose of the shield is to surround the load, sample, and sensor with a surface that is at or
near their temperature to minimize radiation. The shield is exposed to the room temperature surface of the vacuum
shroud on its outer surface, so some cooling power must be directed to the shield to keep it near the load temperature. If
the cooling system does not include an integrated radiation shield (or one cannot be easily made), one alternative is to
wrap several layers of super-insulation (aluminized Mylar) loosely between the vacuum shroud and load. This reduces
radiation transfer to the sample space.
2.10 TEMPERATURE
CONTROL
The Model 370 includes the necessary electronics to perform closed-loop temperature control in a dilution refrigerator or
other low power cryogenic cooling system. The load must be equipped with a temperature sensor for feedback and a
resistive heater to add heating power into the system. The instrument, sensor, and heater play important roles in
establishing stable temperature control.
Theory of Operation
2-17
Содержание 370
Страница 22: ...Lake Shore Model 370 AC Resistance Bridge User s Manual 1 12 Introduction This Page Intentionally Left Blank ...
Страница 60: ...Lake Shore Model 370 AC Resistance Bridge User s Manual 3 16 Installation This Page Intentionally Left Blank ...
Страница 106: ...Lake Shore Model 370 AC Resistance Bridge User s Manual 5 12 Advanced Operation This Page Intentionally Left Blank ...