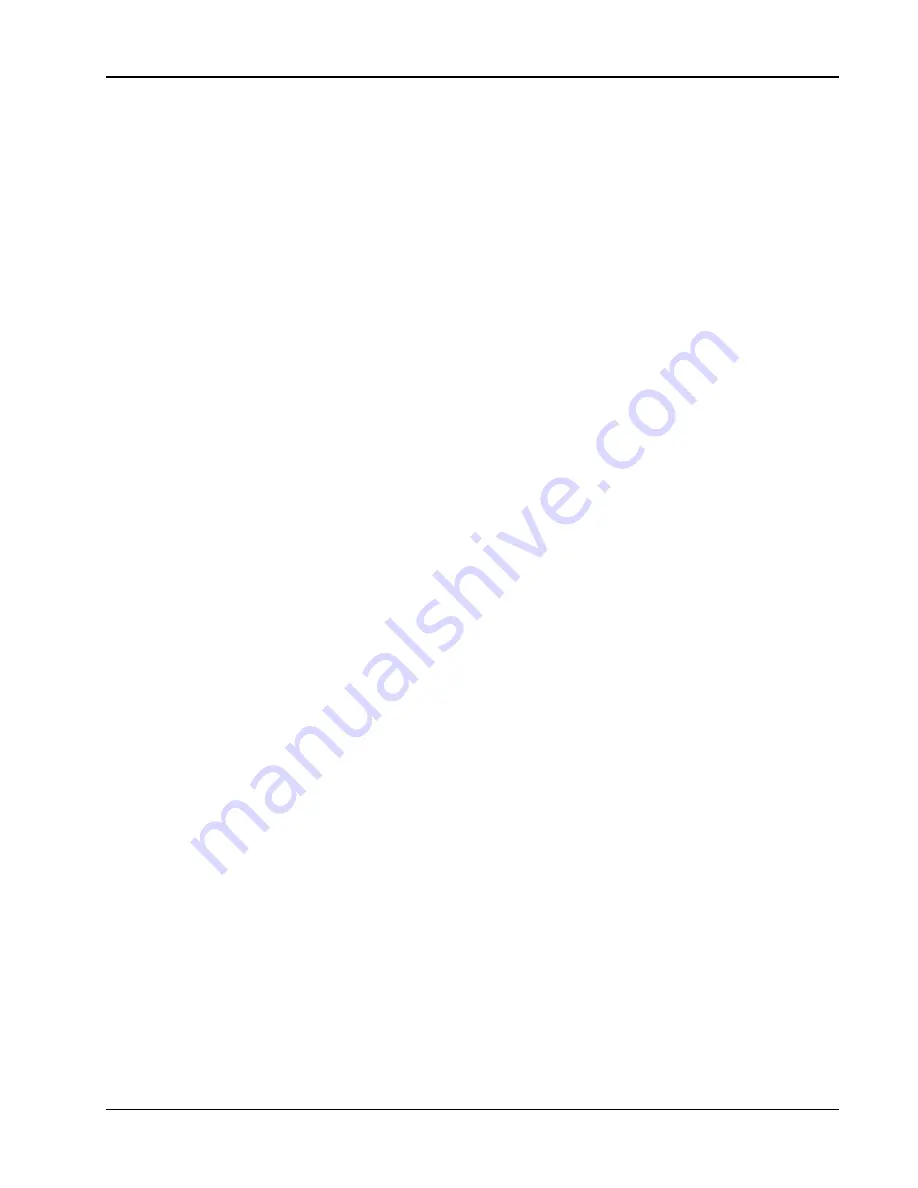
Lake Shore Model 370 AC Resistance Bridge User’s Manual
4.10 TEMPERATURE
MEASUREMENT
One application of the Model 370 is measuring temperature of resistive temperature detectors (RTDs). The resistance
range and excitation power of the instrument are ideal for temperature measurements using any common cryogenic RTD.
Resistance of an RTD can be measured and displayed at any time. The instrument can convert resistance to temperature
and display temperature in Kelvin if a temperature response curve is loaded into the instrument and assigned to the
sensor. Information on how to load curves into the instrument is given in Paragraph 5.2. This paragraph summarizes
other operations related to temperature measurement. Paragraph 4.11 describes temperature control.
4.10.1 Curve
Selection
After a temperature response curve is loaded into the instrument it must be assigned to an input channel, even if only one
channel is active. Curve selection is done under the
Input Setup
key as described in Paragraph 4.6.4. If a curve is not
properly chosen for a channel, any temperature displays for that channel will show the message “NOCURV”.
4.10.2 Temperature
Display
After a curve is assigned to an input channel, the channel resistance, temperature, or both, can be displayed or queried
over computer interface. Temperature is displayed when Kelvin units are chosen for the display data source under the
Display Setup
key as described in Paragraph 4.4.1. Refer to Paragraph 4.12 for instructions on displaying Max and Min
in temperature, refer to Paragraph 4.11 for instructions on displaying a control setpoint in temperature.
4.11 TEMPERATURE
CONTROL
There are many steps involved in configuring a temperature control loop. Chapter 2 of this manual describes the
principals of closed loop (feedback) control. Chapter 3 describes the necessary hardware installation. This paragraph
describes how to operate control features and set control parameters. Temperature measurement should be operating
fully before proceeding to control. The action of each control parameter should be considered before enabling
temperature control or the instrument may not be able to perform even the most simple control functions. The more
complex features of setpoint ramping and zone control should only be used after the basic functions are operating.
4.11.1
Temperature Control Modes
The Model 370 offers three temperature control modes or the control output can be disabled. Each mode requires
different control parameters so the control mode must be selected before other parameter values.
• Open Loop:
Open loop control is less complicated than closed loop control but is also less powerful. Open loop
control mode allows the user to directly set the heater output value using only the Manual Output parameter. During
Open Loop control only the heater range and Manual Output parameters are active, the setpoint, control channel and
PID parameters are ignored. This type of control guarantees constant power to the load but it does not actively control
temperature. Any change in the characteristics of the cooling system or load will cause a change in temperature.
• Closed Loop PID:
Closed loop PID control, often called feedback control, is the control mode most often associated
with temperature controllers. In this mode the controller attempts to keep the load at exactly the user entered setpoint
that can be entered in resistance or temperature. To do this, it uses feedback from the control sensor to calculate and
actively adjust the control (heater) output. The Model 370 uses a control algorithm called PID that refers to the three
terms used to tune the controller for each unique system. Manual output can also be active during closed loop control
and must be set to zero if not wanted.
The Model 370 offers two tuning modes or ways to set the necessary P, I, and D parameters for closed loop control. In
closed loop PID mode the control parameter values are set manually as described in Paragraph 2.10. Once appropriate
parameters are found they can be stored in the instrument and recalled with the zone feature.
• Zone Tuning:
Optimal control parameters values are often different at varied temperatures within a system. Once
values have been chosen for each temperature range or zone, the zone feature can automatically select the correct
values each time the setpoint is changed. This mode does not help choose control parameter values; it helps use chosen
values more efficiently. Refer to Paragraph 5.3 for details on how to program parameter values into the zone table.
• Off:
When control is turned off the control output is set to zero. If a key related to temperature control is pressed, the
display will show a message indicating that control is off. Use the
Control Setup
key to enable control by choosing
one of the three control modes.
Operation
4-15
Содержание 370
Страница 22: ...Lake Shore Model 370 AC Resistance Bridge User s Manual 1 12 Introduction This Page Intentionally Left Blank ...
Страница 60: ...Lake Shore Model 370 AC Resistance Bridge User s Manual 3 16 Installation This Page Intentionally Left Blank ...
Страница 106: ...Lake Shore Model 370 AC Resistance Bridge User s Manual 5 12 Advanced Operation This Page Intentionally Left Blank ...