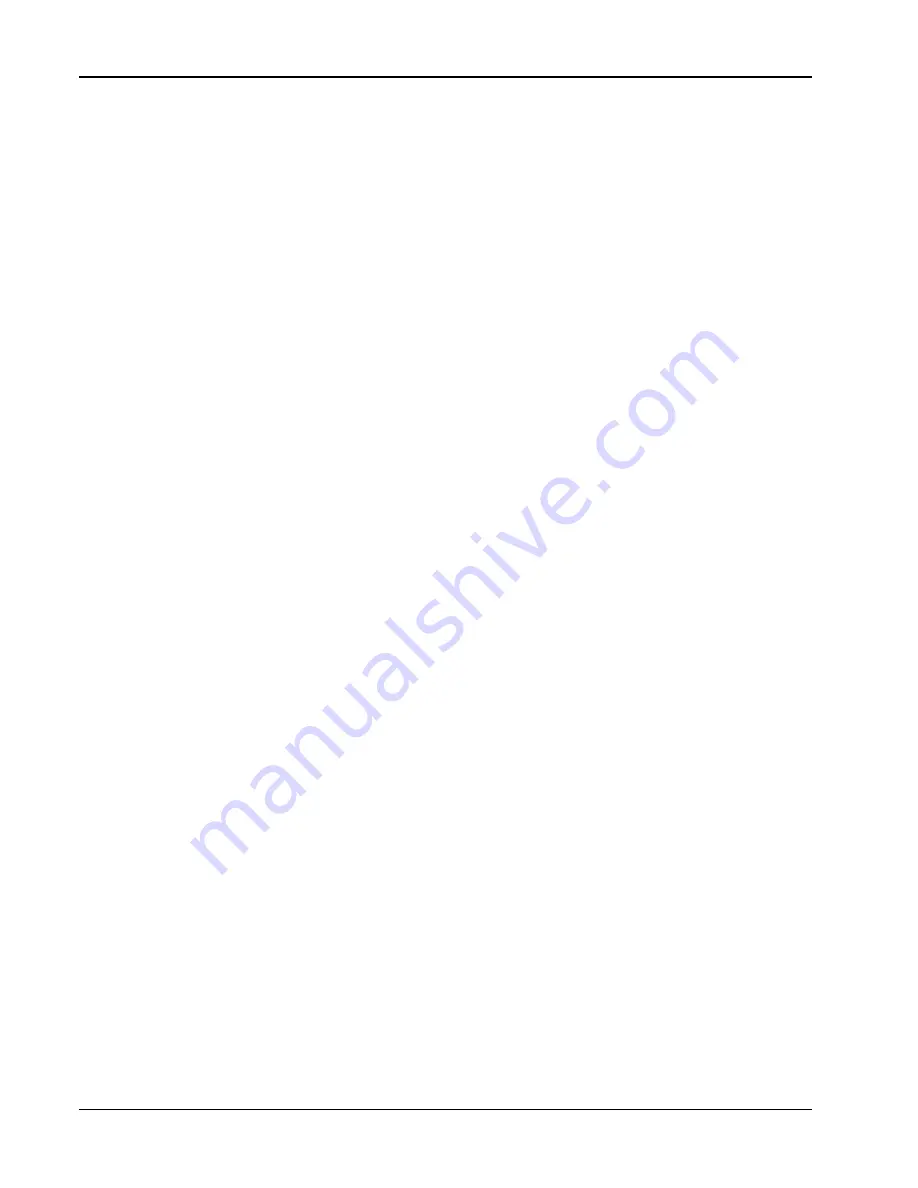
Lake Shore Model 370 AC Resistance Bridge User’s Manual
2.9.2 Sensor
Calibration
The Model 370 can convert the resistance of a sensor to temperature if a temperature response curve is loaded into the
instrument. Most curves are generated from an individual sensor calibration because few sensors follow a standard curve
at low temperatures. The instrument can use curve options, called CalCurves, available with Lake Shore calibrated
sensors or curves generated by the user. The Lake Shore Temperature Measurement and Control catalog gives complete
specifications for calibrated sensors and gives the calibration range available for each sensor.
When calibrating sensors in house remember to account for error caused by interpolation between curve breakpoints.
The Model 370 allows curves with up to 200 breakpoints and uses linear interpolation between breakpoints. Linear
interpolation is considered by some to be less accurate than polynomial interpolation but it is more predictable. If linear
interpolation errors are larger than desired in a specific temperature range more breakpoints can be added to reduce the
error. NTC resistor breakpoints are entered as Log
Ω
vs. K which acts to linearize temperature response data. Polynomial
interpolation has the potential to calculate a result that is well off the curve if data points are not smoothed properly and
there is a small discontinuity between breakpoints.
2.9.3 Sensor
Installation
This section highlights some of the important elements of proper temperature sensor installation. Information on
installing temperature sensors applies equally well to other resistance measurements. For more detailed information,
Lake Shore sensors are shipped with installation instructions covering that specific sensor type and package. The Lake
Shore Temperature Measurement and Control Catalog includes an installation section as well. Lake Shore also offers a
line of Cryogenic Accessories. Many of the materials discussed here are available through Lake Shore and can be
ordered with sensors or instruments.
2.9.3.1 Mounting
Materials
Choosing appropriate mounting materials is very important in a cryogenic environment. The high vacuum used to
insulate cryostats is one source of problems. Materials used in these applications should have a low vapor pressure so
they do not evaporate or out-gas and spoil the vacuum insulation. Metals and ceramics do not have this problem but
greases and varnishes must be checked. Another source of problems is the wide extremes in temperature most sensors
are exposed to. The linear expansion coefficient of a materials becomes important when temperature changes are so
large. Never try to permanently bond materials with linear expansion coefficients that differ by more than three. A
flexible mounting scheme should be used or the parts will break apart, potentially damaging them. The thermal
expansion or contraction of rigid clamps or holders could crush fragile samples or sensors that do not have the same
coefficient. Thermal conductivity is a property of materials that can change with temperature. Do not assume that
materials that work well at room temperature will do the same job at low temperatures.
2.9.3.2 Sensor
Location
Finding a good place to mount a sensor in an already crowded cryostat is never easy. There are fewer problems if the
entire load and sample holder are at the same temperature, unfortunately, this not the case in many systems. Temperature
gradients (differences in temperature) exist because there is seldom perfect balance between the cooling source and heat
sources. Even in a well-controlled system, unwanted heat sources like thermal radiation and heat conducting through
mounting structures can cause gradients. For best accuracy, sensors should be positioned near the sample, so that little or
no heat flows between the sample and sensor. This may not, however, be the best location for temperature control as
discussed below.
2.9.3.3 Thermal
Conductivity
The ability of heat to flow through a material is called thermal conductivity. Good thermal conductivity is important in
any part of a cryogenic system that is intended to be the same temperature. Copper and aluminum are examples of metals
that have good thermal conductivity, while stainless steel does not. Metals that super conduct tend to be better thermal
conductors when normal and poor thermal conductors below their transition temperature. Non-metallic, electrically
insulating materials like alumina oxide and similar ceramics have good thermal conductivity, while G-10 epoxy-
impregnated fiberglass does not. Sensor leads should have poor thermal conductivity. Sensor packages, cooling loads,
and sample holders should have good thermal conductivity to reduce temperature gradients. Surprisingly, the
connections between thermally conductive mounting surfaces often have very poor thermal conductivity.
2-16
Theory of Operation
Содержание 370
Страница 22: ...Lake Shore Model 370 AC Resistance Bridge User s Manual 1 12 Introduction This Page Intentionally Left Blank ...
Страница 60: ...Lake Shore Model 370 AC Resistance Bridge User s Manual 3 16 Installation This Page Intentionally Left Blank ...
Страница 106: ...Lake Shore Model 370 AC Resistance Bridge User s Manual 5 12 Advanced Operation This Page Intentionally Left Blank ...