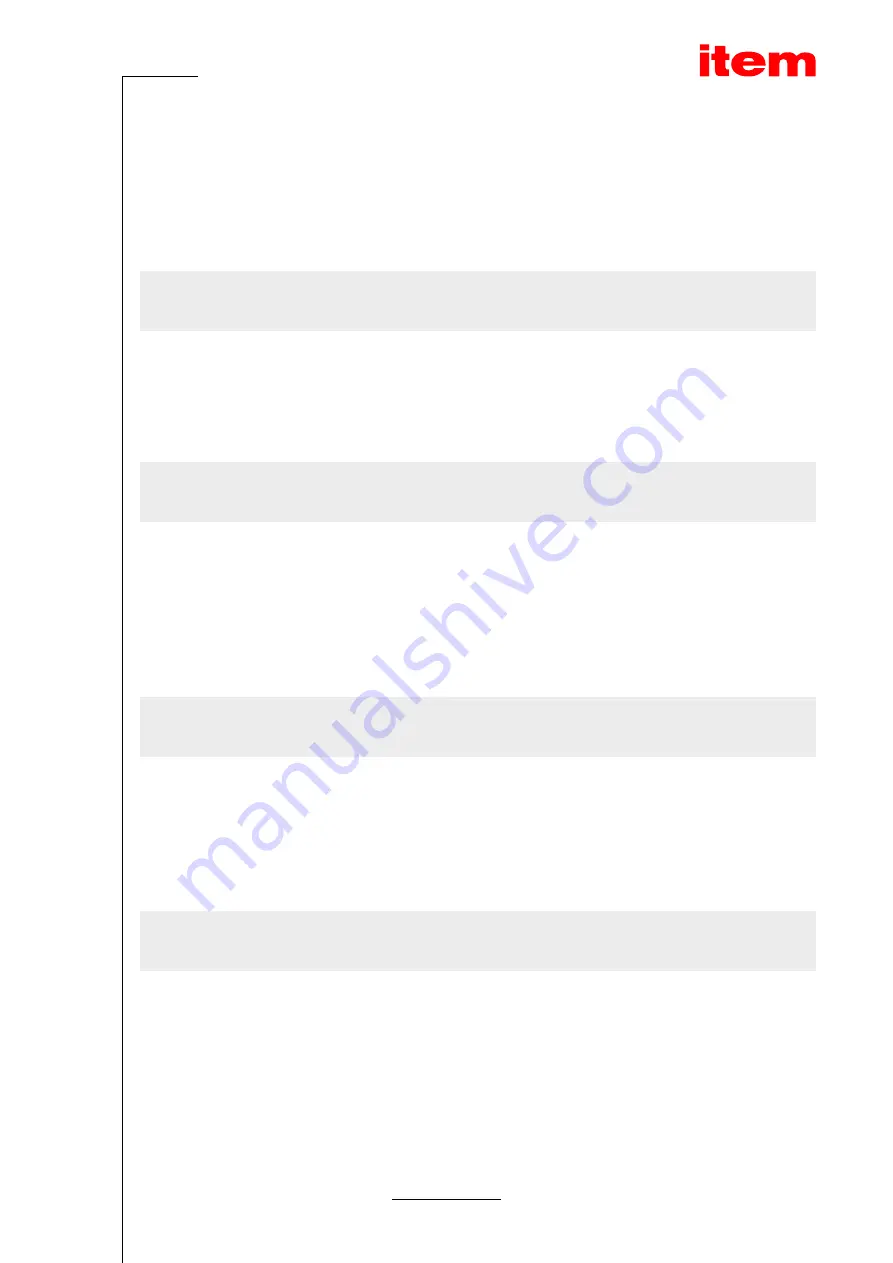
27
item Controller BL 1-04 /C
― Product manual
The window has several areas:
The first three LEDs indicate the status of the functional safety system in the servo drive firmware as it has been recognised by
the finite state machine of the servo drive.
The LEDs Input STOA and Input STOB indicate the state of the digital inputs as it has been recognised by the servo drive
firmware. The indication in MotionSoft is of an informative nature and not part of the safety function itself.
4.9 Functional test, validation
The STO function must be validated after the installation or after the installation has been changed.
This validation must be documented by the person performing the commissioning process. To assist you with the commission
-
ing process, section 11 Appendix on page 73 provides example checklists with questions for a risk reduction. However, these
checklists are no substitute for safety training. No guarantee can be provided for the completeness of the checklists.
4.10 Operation
Obligations of the owner/operator
The safety system must be checked for correct operation at appropriate intervals. It is the responsibility of the owner/operator
to choose the type of check and the time intervals in the specified time period. The check is to be conducted such that the
correct operation of the safety system can be verified based on an interaction of all of the components.
Maintenance and care
A servo drive of the BL 1-04 /C series with an integrated STO function is maintenance- free.
4.11 Diagnostics and fault clearance
STO-based fault messages
Error messages that are issued with regard to the functional safety system have error numbers from 51 to 52. These messag
-
es are described in the error table.
If an error message cannot be acknowledged, its cause must be remedied by applying the recommended measures. Then,
reset the servo drive and check whether the cause of the error, and the error message, have been eliminated.
5 Fault messages
Servo drives of the BL 1-04 /C series have an extensive sensor system that monitors the controller unit, power output stage
and motor as well as the communication with the outside world. Most errors will cause the controller unit to shut down the
servo drive and the power output stage. The power output stage cannot be switched back on until the cause of the error has
been eliminated and the error has been cleared.
If an error occurs, the servo drive will display an error message cyclically by way of its seven-segment display. The error mes
-
sage consists of the letter E (for error), a main index and a subindex, e.g.: E 0 1 0.