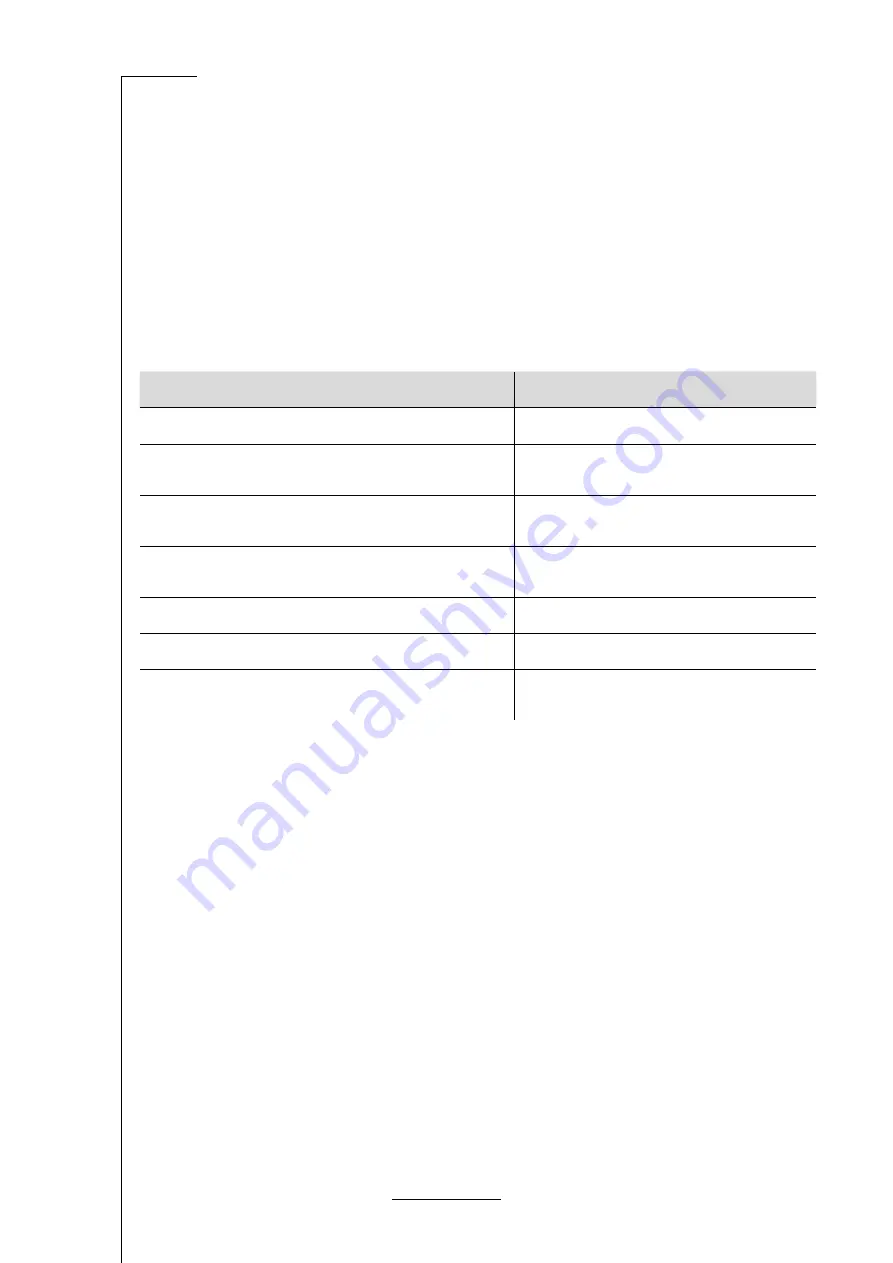
item Controller BL 1-04 /C
― Product manual
40
HIPERFACE
®
encoders
Shaft encoders with HIPERFACE
®
made by Sick-Stegmann are supported in the single- turn and multi-turn variants. The follow
-
ing encoder models can be connected:
▪ Single-turn SinCos encoders: SCS 60/70, SKS 36, SRS 50/60/64, SEK 34/37/52
▪ Multi-turn SinCos encoders: SCM 60/70, SKM 36, SRM 50/60/64, SEL 34/37/52
▪ Single-turn SinCos encoders for hollow shaft drives: SCS-Kit 101, SHS 170, SCK 25/35/40/45/50/53
▪ Multi-turn SinCos encoders for hollow shaft drives: SCM-Kit 101, SCL 25/35/40/45/50/53
In addition, the following Sick-Stegmann encoder systems can be connected and evaluated:
▪ Absolute, non-contact length measuring systems L230 and TTK70 (HIPERFACE
®
)
▪ Digital incremental encoder CDD 50
Characteristic
Value
Parameterisable number of encoder lines
depending on the encoder
Track signals A, B (Z0 track)
As per RS485
Input: 0.4 V, output: 0.8 V to 2 V
Hall generator input
TTL Pegel (<0.5 V = Low, > 2 V = Hi)
2 kΩ Pullup
Error input (pin 6)
TTL level (<0.5 V = Low, > 2 V = Hi) 2 kΩ pull-up
Track signal input impedance
Differential input 120 Ω
Limit frequency
Up to 10 MHz, depending on the encoder system
Supported operating modes
Storage of the parameter set in the encoder in the
case of Endat and HIPERFACE
®
Angle encoders made by Sick with the HIPERFACE DSL
®
interface (e.g. EKM36) are supported. They must be connected to
X6. See section 8.3 BL 1-04 /C: Motor connector [X6] on page 35.
EnDat encoders
Incremental and absolute encoders by Heidenhain with the ordering code ENDAT22 can be evaluated. The following encoder
models can be connected:
▪ Analogue incremental encoders: ROD 400, ERO 1200/1300/1400, ERN 100/400/1100/1300
▪ Single-turn encoders (ENDAT22): ROC 425, ECI 119/1118/1319, ECN 125/425/1023
▪ Multi-turn encoders (ENDAT22): ROQ 437/1035, EQI 1131/1331, EQN 437/1035/1135/1337
▪ Absolute length measuring systems (ENDAT22): LC 115/415
▪ Battery-buffered encoders (ENDAT22): EBI 135/1135/4010
▪ Angle encoder modules (ENDAT22): MRP 2010/5010/8010
BiSS encoders
®
Type C BiSS encoders are supported. The evaluation of the internal type plate, however, is not supported. The storage of data
in the encoder is not possible.
Encoders made by Hengstler, Kübler and Balluff are supported.