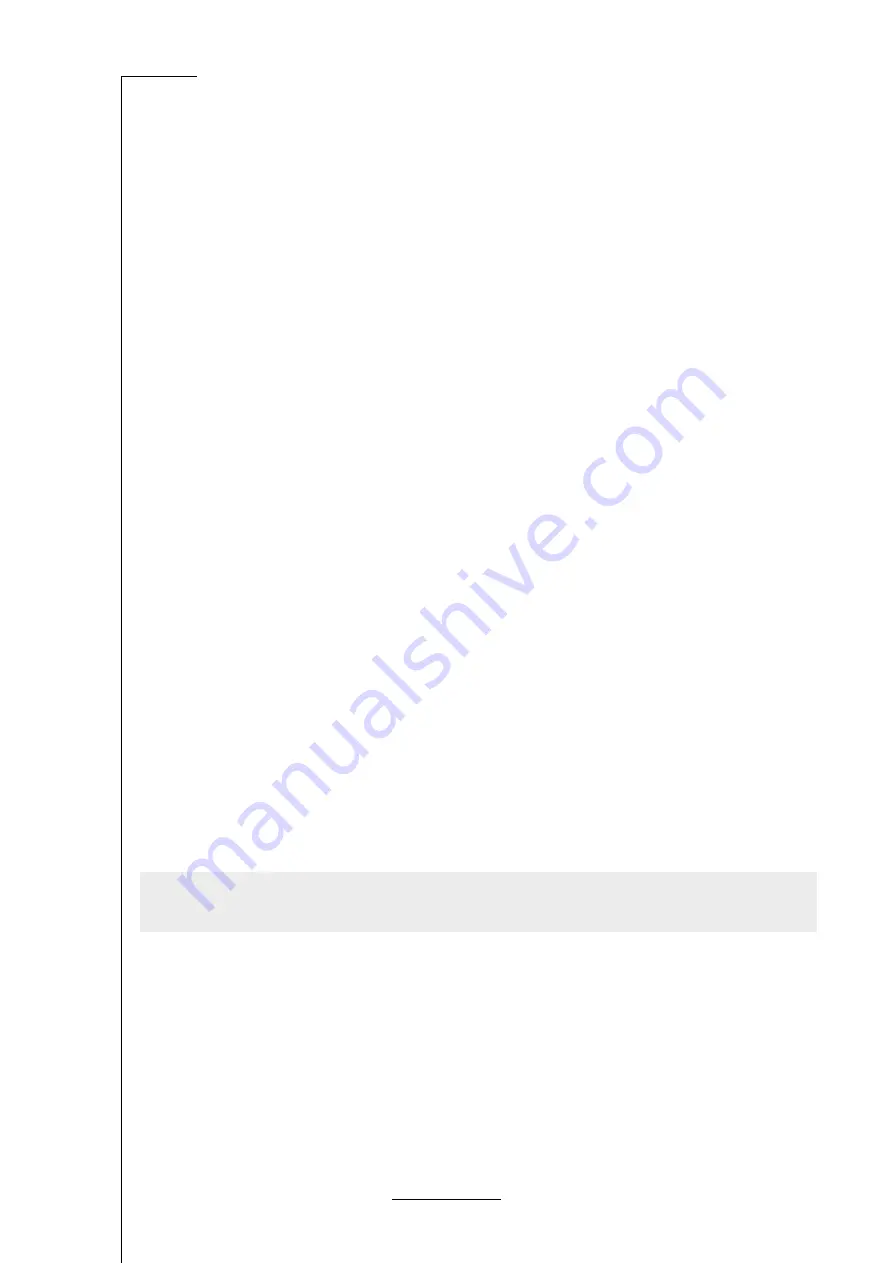
item Controller BL 1-04 /C
― Product manual
16
Brake control and automatic brake
▪ Direct control of a holding brake in the motor with high current. As a result, an external relay is not necessary. In addition,
variable delays can be used.
▪ "Automatic brake" for deactivating the power section during longer breaks to save energy
Electrical characteristics
▪ Wide-range supply input (AC)
▪ "Soft switch-on" features for the soft precharging and quick charging of the DC bus
▪ DC bus coupling between devices with the same mains power supply for buffering the brake energy
▪ Improved monitoring and analysis of the mains power supply by a direct measurement of the mains voltage
Applications
▪ Speed- and angle-synchronous operation with an electronic gear unit via the incremental encoder input or fieldbus. Exten
-
sive modes of operation for synchronisation, e.g. "flying saw"
▪ Jog mode, teach-in mode, motion programs, torque-limited set control and much more
Special control features
▪ High control quality due to high-quality sensors, far superior to conventional market standards, and above-average proces
-
sor resources
▪ Short cycle times, bandwidth in the current control circuit approx. 2 kHz (with ti= 32 µs), in the speed control circuit approx.
500 Hz (with tn= 64 µs)
▪ Parameterisable band-stop filters for suppressing the natural frequency of the controlled system
▪ Load torque compensation for vertical axes
▪ Synchronisable internal clock system for the synchronisation with external clock sources for CANopen and EtherCAT
fieldbus systems by way of an internal PLL
Certification and qualification
▪ Compliance with the current CE and EN standards without any additional external measures
▪ UL certification
▪ Completely closed, EMC-optimised housing for mounting on conventional switch cabinet mounting plates. The devices
have an IP20 degree of protection.
▪ Integration of all of the required filters, e.g. line filters, filters for the 24 V supply and filters for the inputs and outputs, into
the device in order to ensure compliance with the EMC regulations during operation (industrial environment)
4 STO (safe torque off)
The purpose of this chapter is to ensure the safe use of the STO (safe torque off) safety function that is integrated
in the servo drive.
This documentation refers to the following versions:
▪ Controller BL 1-04 /C with the STO function, revision 1.0 or higher
▪ item MotionSoft parameterisation program version 3.0 or higher.