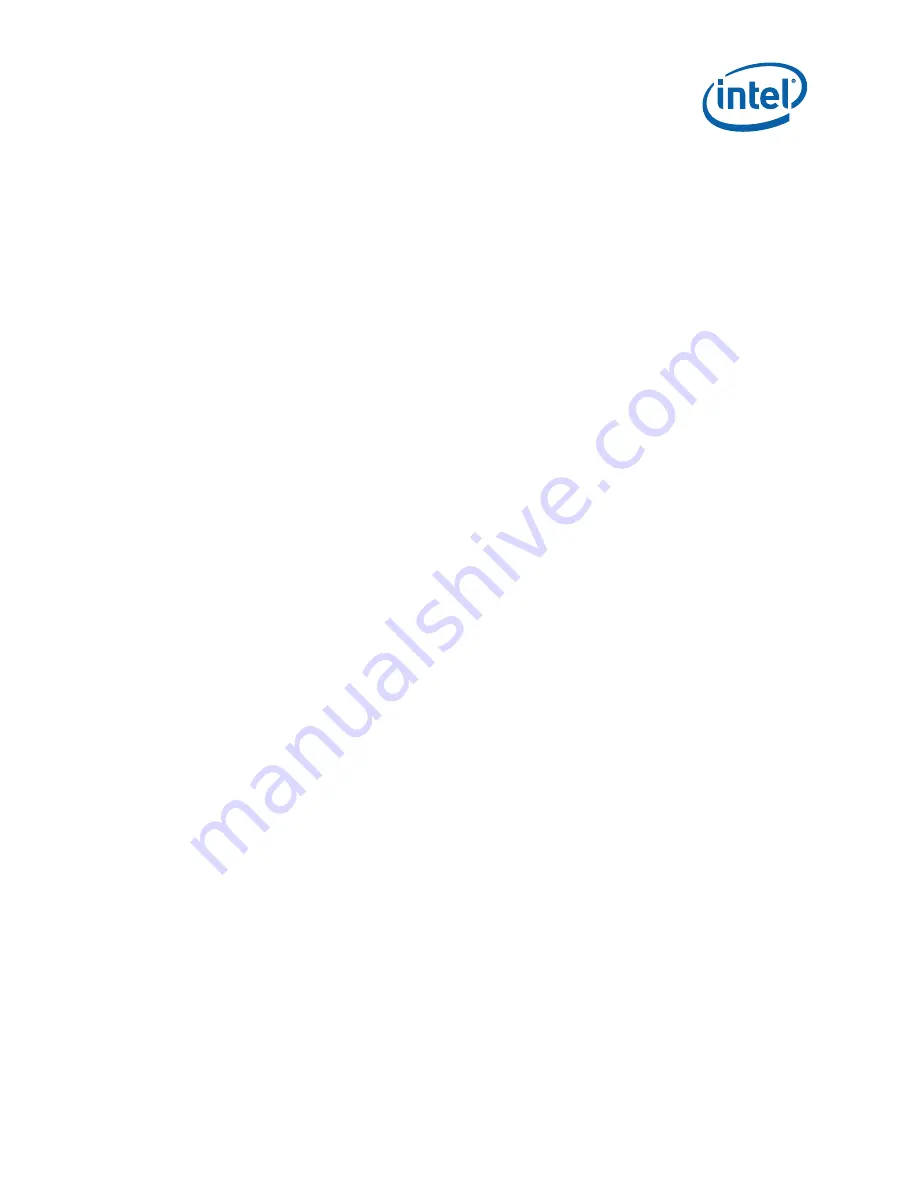
Processor Thermal/Mechanical Information
Thermal and Mechanical Design Guidelines
25
In addition to passive heatsinks, fan heatsinks and system fans are other solutions
that exist for cooling integrated circuit devices. For example, ducted blowers, heat
pipes and liquid cooling are all capable of dissipating additional heat. Due to their
varying attributes, each of these solutions may be appropriate for a particular system
implementation.
To develop a reliable, cost-effective thermal solution, thermal characterization and
simulation should be carried out at the entire system level, accounting for the thermal
requirements of each component. In addition, acoustic noise constraints may limit the
size, number, placement, and types of fans that can be used in a particular design.
To ease the burden on thermal solutions, the Thermal Monitor feature and associated
logic have been integrated into the silicon of the processor. By taking advantage of
the Thermal Monitor feature, system designers may reduce thermal solution cost by
designing to TDP instead of maximum power. Thermal Monitor attempts to protect the
processor during sustained workload above TDP. Implementation options and
recommendations are described in Chapter
2.4.3
Summary
In summary, considerations in heatsink design include:
•
The local ambient temperature T
A
at the heatsink, which is a function of chassis
design.
•
The thermal design power (TDP) of the processor, and the corresponding
maximum T
C
as calculated from the thermal profile. These parameters are usually
combined in a single lump cooling performance parameter,
Ψ
CA
(case to air
thermal characterization parameter). More information on the definition and the
use of
Ψ
CA
is given Sections
•
Heatsink interface to IHS surface characteristics, including flatness and roughness.
•
The performance of the thermal interface material used between the heatsink and
the IHS.
•
The required heatsink clip static load, between 18 lbf to 70 lbf throughout the life
of the product (Refer to Section
2.1.2.2 for further information).
•
Surface area of the heatsink.
•
Heatsink material and technology.
•
Volume of airflow over the heatsink surface area.
•
Development of airflow entering and within the heatsink area.
•
Physical volumetric constraints placed by the system
2.5
System Integration Considerations
Manufacturing with Intel
®
Components using 775–Land LGA Package and LGA775
Socket documentation provides Best Known Methods for all aspects LGA775 socket
based platforms and systems manufacturing. Of particular interest for package and
heatsink installation and removal is the System Assembly module. A video covering
system integration is also available. Contact your Intel field sales representative for
further information.
Содержание Celeron Dual-Core E1000 Series
Страница 10: ...10 Thermal and Mechanical Design Guidelines...
Страница 26: ...Processor Thermal Mechanical Information 26 Thermal and Mechanical Design Guidelines...
Страница 68: ...ATX Thermal Mechanical Design Information 68 Thermal and Mechanical Design Guidelines...
Страница 86: ...Heatsink Clip Load Metrology 86 Thermal and Mechanical Design Guidelines...
Страница 88: ...Thermal Interface Management 88 Thermal and Mechanical Design Guidelines...
Страница 120: ...Legacy Fan Speed Control 120 Thermal and Mechanical Design Guidelines...
Страница 124: ...Balanced Technology Extended BTX System Thermal Considerations 124 Thermal and Mechanical Design Guidelines...
Страница 126: ...Fan Performance for Reference Design 126 Thermal and Mechanical Design Guidelines...
Страница 127: ...Fan Performance for Reference Design Thermal and Mechanical Design Guidelines 127...
Страница 139: ...Mechanical Drawings Thermal and Mechanical Design Guidelines 139 Figure 7 57 Reference Fastener Sheet 1...
Страница 140: ...Mechanical Drawings 140 Thermal and Mechanical Design Guidelines Figure 7 58 Reference Fastener Sheet 2...
Страница 141: ...Mechanical Drawings Thermal and Mechanical Design Guidelines 141 Figure 7 59 Reference Fastener Sheet 3...
Страница 142: ...Mechanical Drawings 142 Thermal and Mechanical Design Guidelines Figure 7 60 Reference Fastener Sheet 4...