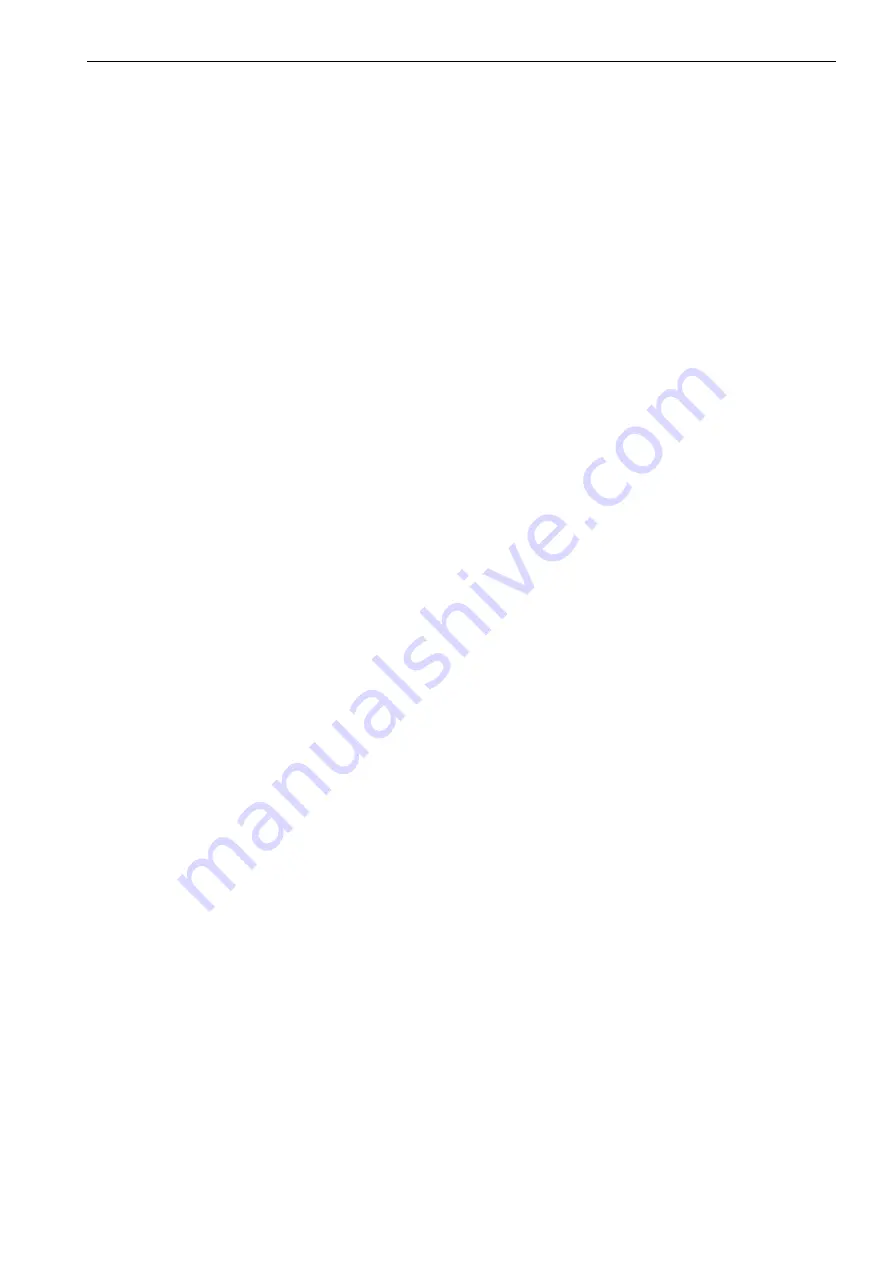
AD104-R2, AD104-R5
9 / 75
ba_aed104_8_e.doc
Trigger input (electrical data):
High:
3.2V ... 5V
Low:
0V ... 0.8V
Input current:
<2.5 mA
Important notes on EMC protection:
The PCB AD104 alone has no EMC protection. The EMC protection can be achieved in addition with a shielded
housing for the electronic and the use of shielded cable.
Mount the load cell onto a metallic carrier which is connected to the ground connection of the device, or shield
AD104 with the load cell and load introduction parts as a complete unit. The cable shield needs to be connected
with the measuring body of the loadcell and the housing of the AED.
The housing of the AED or the load cell has to be connected via the solder pad to the PCB (see Fig. 5,
‘connection to housing’).
The AED unit itself is provided with a protective filter for all interfaces and supply lines.
The connection between load cell and electronics should be as short as possible. Depending on the bridge
resistance of the transducer used, line length, and line cross-section of the transducer connection cable, voltage
drops arise that lead to a reduction in the bridge supply voltage. Additionally, the voltage drop on the connection
cable is also temperature-dependent ( copper resistance ). The transducer output signal also changes in
proportion to the bridge supply voltage.
With the 4-wire circuit used, there still result measurement errors in conditions with changing temperatures,
caused by the temperature-dependent cable resistance and possibly also by transitory resistances in the
connectors.
When setting up a measurement chain (electronics outside the transducer) it should also be noted that the
AD104 uses a rectangular carrier frequency for bridge supply. Therefore, the cable length between AD104 and
the transducer is limited to 100 cm max. For high precision applications(>= 3000d), the length should be
reduced to 30cm (shielded cable, shield connection on the measuring body and on the shielded housing for
AD104).