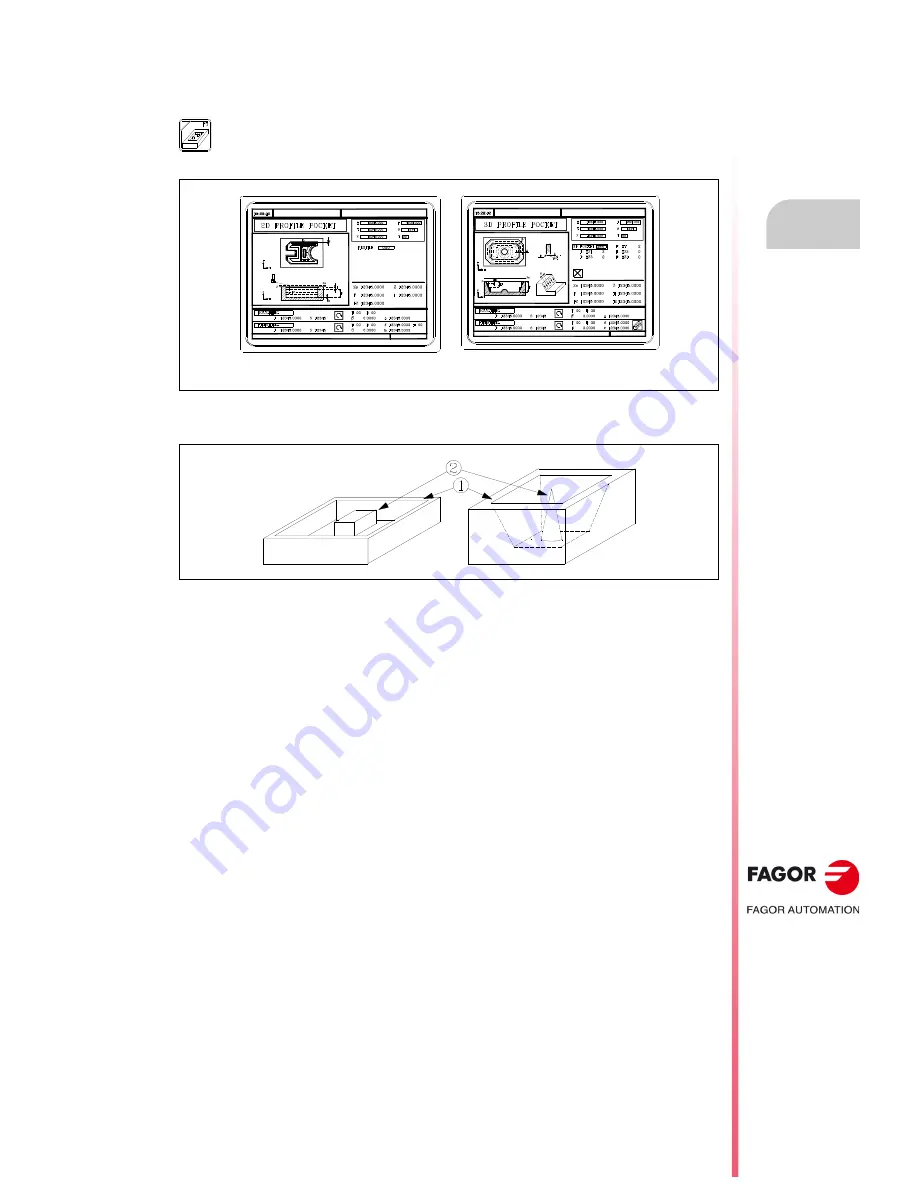
Operating manual
CNC 8055
CNC 8055i
WORKING
WITH OPERATIONS OR
CYCLES
3.
·MC· O
PTION
S
OFT
: V02.2
X
·87·
P
o
cket cycle with a profile
3.5
Pocket cycle with a profile
A pocket is composed by an external contour or profile (1) and a series of internal contours or profiles
(2). These internal profiles are called islands.
• In 2D pockets (top left figure), all the walls of the outside profile and of the islands are vertical.
• In 3D pockets (top right figure), one, several or all the walls of the outside pocket and/or of the
islands are not vertical (up to a maximum of 4).
Programming 2D pockets with profile.
When defining the profile, one must indicate, besides the outside contour of the pocket, the contour
or contours of the islands.
The machining in Z is defined with the following parameters:
Zs
Safety plane coordinate.
Z
Part surface coordinate.
P
Pocket depth.
I
Step in Z.
Fz
Penetrating feedrate in Z.
The following must be defined in the data area for the roughing operation:
The sideways penetration angle.
The milling pass.
The following must be defined in the data area for the finishing operation:
The sideways penetration angle.
Finishing stock on the side walls.
z
Finishing stock at the bottom.
N
Number of finishing passes in Z.
This key accesses the pocket-with-profile operation.
There are two types of pocket with profile; 2D and 3D.
Pocket with 2D profile
Pocket with 2D profile
Содержание 8055i FL EN
Страница 1: ...CNC 8055 MC Operating manual Ref 1705 Soft V02 2x...
Страница 10: ...10 CNC 8055 CNC 8055i Version history...
Страница 16: ...16 CNC 8055 CNC 8055i Returning conditions...
Страница 18: ...18 CNC 8055 CNC 8055i Declaration of conformity and Warranty conditions...
Страница 20: ...20 CNC 8055 CNC 8055i Additional notes...
Страница 22: ...22 CNC 8055 CNC 8055i Fagor documentation...
Страница 70: ...70 Operating manual CNC 8055 CNC 8055i 2 OPERATING IN JOG MODE MC OPTION SOFT V02 2X ISO management...
Страница 126: ...126 Operating manual CNC 8055 CNC 8055i 3 WORKING WITH OPERATIONS OR CYCLES MC OPTION SOFT V02 2X Multiple positioning...
Страница 132: ...132 Operating manual CNC 8055 CNC 8055i 4 OPERATING IN ISO MODE MC OPTION SOFT V02 2X Programming assistance...
Страница 157: ...Operating manual CNC 8055 CNC 8055i 6 SOFT V02 2X 157...
Страница 158: ...158 Operating manual CNC 8055 CNC 8055i 6 SOFT V02 2X...
Страница 159: ......