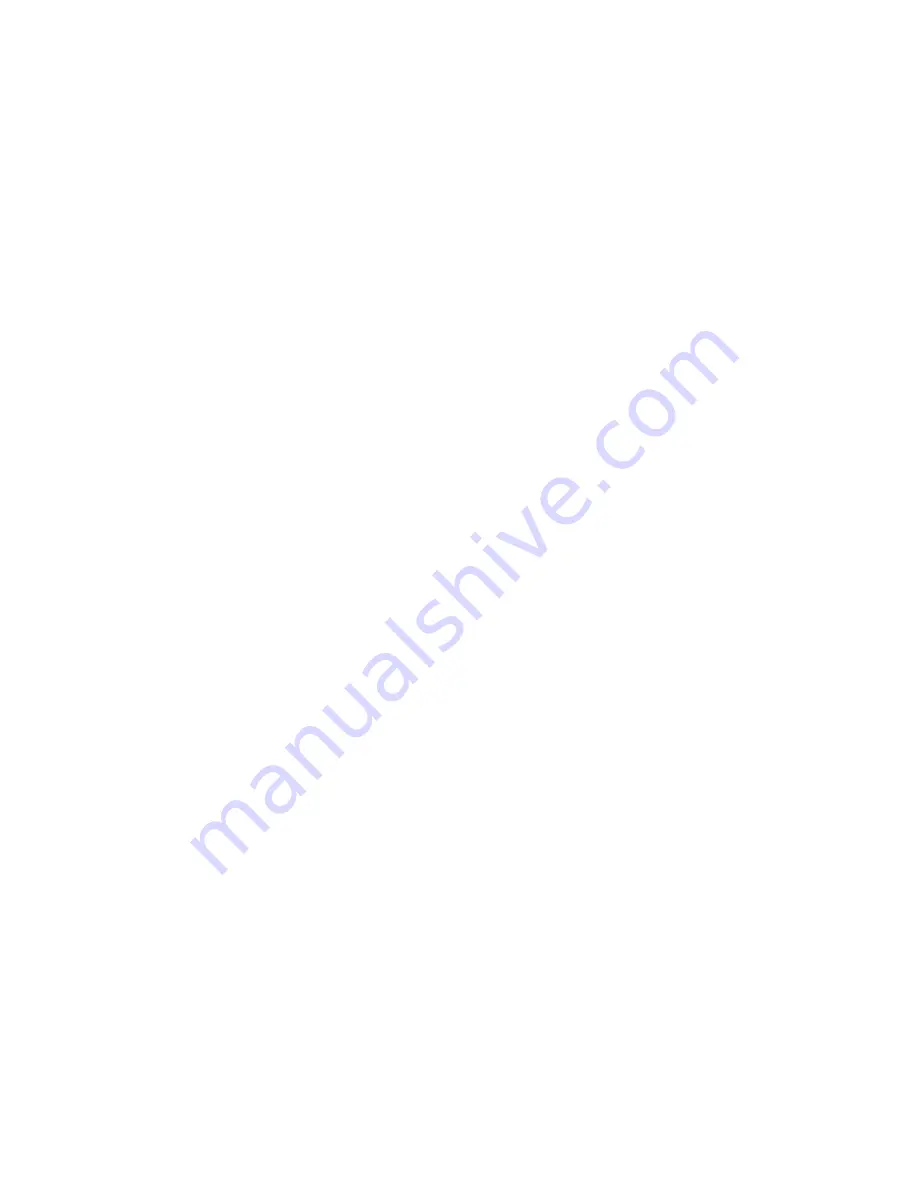
User Manual
Chapter 1
GFK-1742F
Jan 2020
Product Overview
10
torque interface servos, the torque control loop is closed in the servo amplifier, while
the DSM closes the position and velocity loops.
•
In both digital and analog applications, the module provides the same features as
Standard mode including configurable User Units to Counts ratio.
•
In addition, a Master Axis position input can be configured. Each Follower axis tracks
the Master Axis input at a programmable (A:B) ratio. Motion caused by Jog, Move at
Velocity and Execute Motion Program commands can be combined with follower
motion generated by the master axis.
•
Follower options include:
—
Master Axis source configurable as Actual or Commanded Position from any
other axis
—
Master Source Select %Q bit switches between two Master Axis sources
—
Acceleration Ramp to smoothly accelerate a slave axis until its position and
velocity synchronize to the master
—
Separate enable and disable follower trigger sources
Note that Winder mode is not supported in the DSM314. It is supported in the DSM302.
1.3.1
Standard Mode Operation
Figure 3 is a simplified diagram of the Standard mode Position Loop. An internal motion
Command Generator provides Commanded Position and Commanded Velocity to the
Position Loop. The Position Loop subtracts Actual Position (Position Feedback) from
Commanded Position to produce a Position Error. The Position Error value is multiplied by a
Position Loop Gain constant to produce the Servo Velocity Command. To reduce Position
Error while the servo is moving, Commanded Velocity from the Command Generator is
summed as a Velocity Feedforward term into the Servo Velocity Command output.
The following items are included in the data reported by the DSM314 to the host controller:
Commanded Velocity- the instantaneous velocity generated by
the DSM314’s internal path
generator.
Commanded Position-
the instantaneous position generated by the DSM314’s internal path
generator.
Actual Velocity- the velocity of the axis indicated by the feedback.
Actual Position- the position of the axis indicated by the feedback.
Position Error- the difference between the Commanded Position and the Actual Position.
The DSM314 allows a Position Loop Time Constant (in units of 0.1 millisecond) and a
Velocity Feedforward (in units of 0.01 percent) to be programmed. The Position Loop Time
Constant sets the Position Loop Gain and determines the response speed of the closed
Position Loop. The Velocity Feedforward percentage determines the amount of
Commanded Velocity that is summed into the Servo Velocity Command.