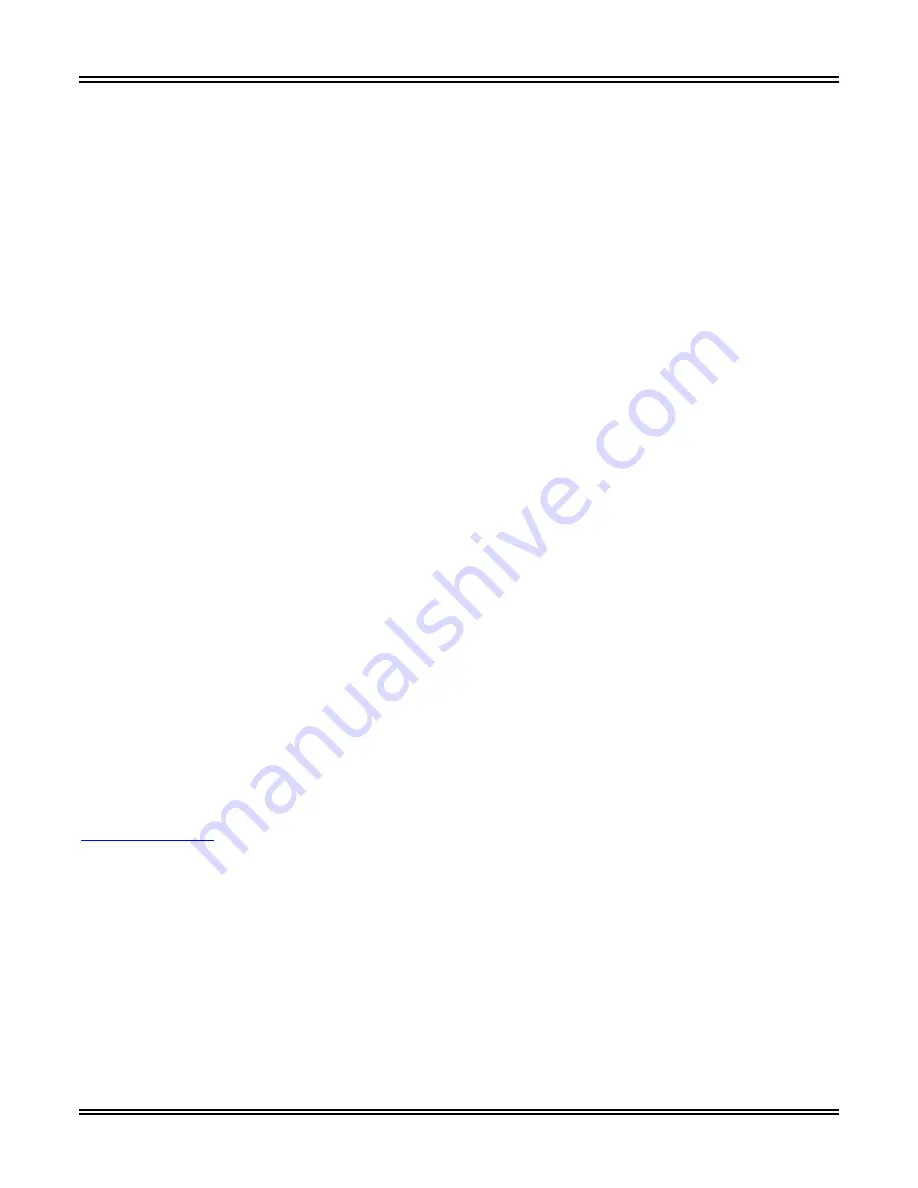
TPU2000/2000R Modbus/Modbus Plus/ Modbus TCP/IP Automation Guide
358
Appendix D- TELEBYTE RS 232/485 Converter Connection To
ABB Protective Relays
ABSTRACT
: There are many RS 232 to RS 485 converters on the market. Although ABB cannot and does not
endorser a particular manufacturer of product, it does document several manufacturers’ products with their use in
systems using ABB protective relays. This application note illustrates the setup and connection of the TELEBYTE
Model 245 optically isolated RS 232 to RS485 (2-wire/4wire) physical interface converter.
Typical Installation
The ABB protective relay is designed with a variety of physical communication interfaces. The ABB distribution
relays such as the MSOC, GPU 2000R, TPU 2000R, DPU 2000R, DPU 2000, DPU 2000 and DPU 1500R are
available with an RS 232, and/or RS 485 port(s).
Other devices such as the PONI M card for the REL 356 have only an RS 485 port.
Many host devices only have an RS 232 port(s). A method to connect such a device is required. Several
converters are available to transform the physical interface on a device from RS 232 to RS 485. The advantages
of RS 485 are that many devices may be attached to a single host in a multi-drop topology. RS 485 may
communicate with up to 32 devices with an addressable protocol. An advantage of the Telebyte 245 converter is
that, like the ABB protective relay, it is an isolated device.
General Information
Figure 1 illustrates the packaging of the Telebyte converter. The Telebyte Converter has two sets of red LED’s
indicating transmission and reception of information on its ports. One set of LED’s indicates
transmission/reception of data on its RS 232 port. The second set of LED’s indicates transmission/reception of
data on its RS 232/RS 485 port. These LED’s are invaluable in visual troubleshooting of communications.
The Telebyte converter has two sets of dB 25 connectors. One connector is a standard RS 232 interface
whereas the other connector is the RS 485/RS 422 interface. Switches 1 and 2 configure the RS 485 interface.
A DTE/DCE (Data Terminal Emulation / Data Communication Emulation) switch configures the RS 232 pins
determining where the data is expected (DTE = Data is Transmitted on Pin 2 and Data is Receive on Pin 3| DCE
= Data is Transmitted on Pin 3 and Data is Received on Pin 2) on the RS 232 interface. Furthermore, Switch 2
configures the RS 485-control mode from the RS 232 port. In two-wire emulation, data control may occur from
the RS 232 port’s RTS (Request To Send) line or whether the data on the TD (Transmitted Data) pin is sensed. If
the ABB device is a MSOC, GPU 2000R, TPU 2000R, DPU 2000R, DPU 2000, DPU 2000 and DPU 1500R, no
data handshaking is permitted, thus the RS 232/485 converter must be configured for TD (Transmitted Data)
mode. However, if the device attaching to the RS 232 port is a host which utilizes RTS/CTS (Request To Send/
Clear To Send) handshaking, the unit must be configured using the RTS dipswitch settings as illustrated in Figure
1. Additional information on the TELEBYTE 245 Optically Isolated converter is available on their website at
www.telebyteusa.com
.
There are several steps required to successfully install a communication network using a physical interface
converter. They are:
1. Knowledge of the RS 232 interfaces. (What type of handshaking is employed?, Is the port DCE or DTE
emulation?, Does the program executing on the attached device require certain signals such as CTS [Clear
To Send], RTS [Request To Send], CD [ Carrier Detect], DTR [Data Terminal Ready])? , What is the voltage
of the RS 232 interface signals?)
2. Knowledge of the available power required. (If the converter requires external power, what is the voltage
required?)
3. Knowledge of the RS 485 devices connected (2 Wire or 4 Wire?, Biasing Required?, Length of network?,
Number of Devices Attached? Are the devices isolated?)
4. Proper installation of bias resistors.
5. Proper installation of termination resistors.