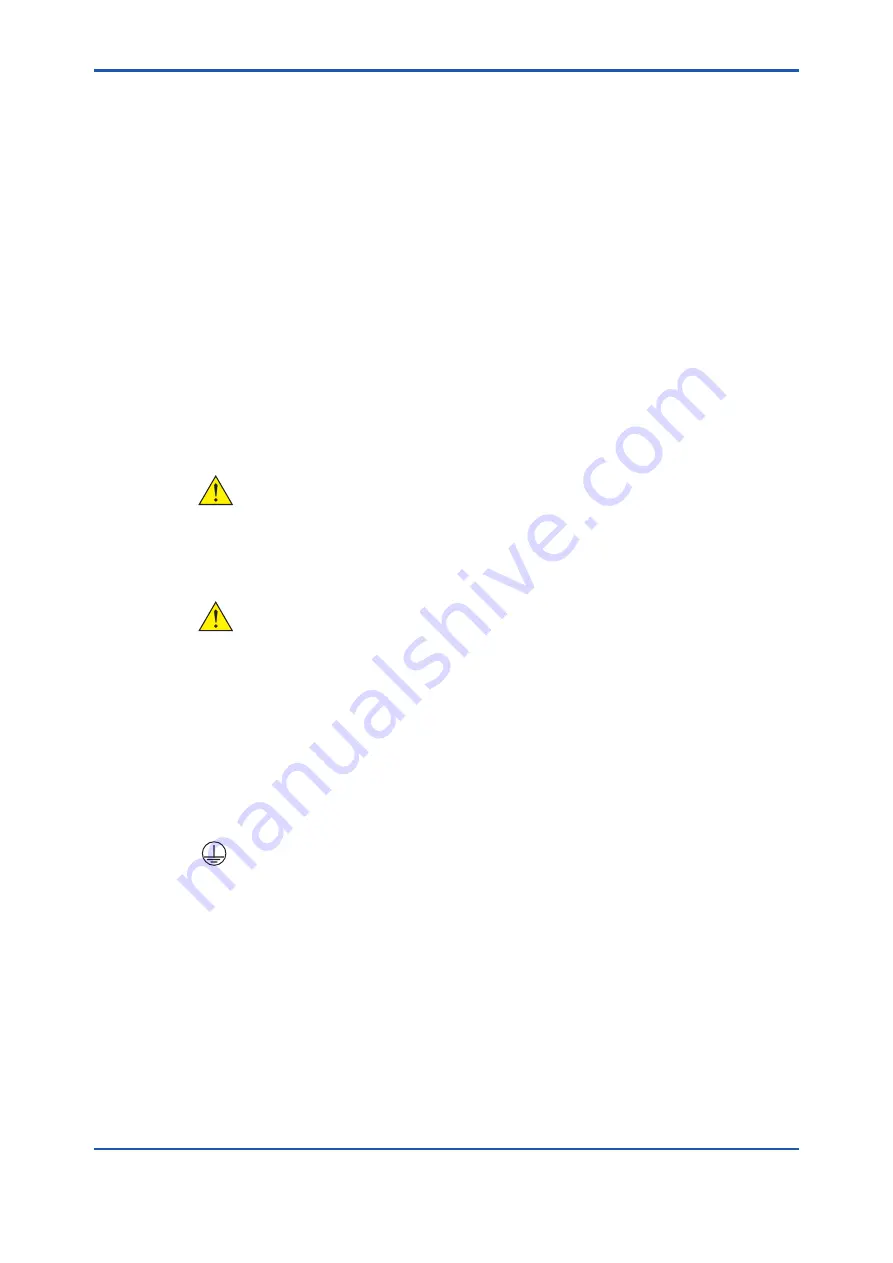
v
PREFACE
IM11G06A01-02EN
1st Edition : Oct. 27, 2023-00
u
Safety Precautions
n
Safety, Protection, and Modification of the Product
• This manual is intended for the following personnel :
• Engineers responsible for installation, wiring, and maintenance of the equipment
• Personnel responsible for normal daily operation of the equipment.
• In order to protect the system controlled by the product and the product itself and ensure
safe operation, observe the safety precautions described in this user’s manual. We assume
no liability for safety if users fail to observe these instructions when operating the product.
• If this instrument is used in a manner not specified in this user’s manual, the protection
provided by this instrument may be impaired.
• If any protection or safety circuit is required for the system controlled by the product or for
the product itself, prepare it separately.
• Be sure to use the spare parts approved by Yokogawa Electric Corporation (hereafter
simply referred to as YOKOGAWA) when replacing parts or consumables.
• Modification of the product is strictly prohibited.
• The following safety symbols are used on the product as well as in this manual.
WARNING
This symbol indicates that an operator must follow the instructions laid out in this manual
in order to avoid the risks for the human body and health including risk of injury, electric
shock, or fatalities. or the damages to instruments. The manual describes what special
care the operator must take to avoid such risks.
CAUTION
This symbol indicates that the operator must refer to the instructions in this manual in
order to prevent the instrument (hardware) or software from being damaged, or a system
failure from occurring.
The following are signal words to be found only in our instruction manuals.
CAUTION
This symbol gives information essential for understanding the operations and functions.
NOTE
This symbol indicates information that complements the present topic.
This symbol indicates Protective Ground Terminal.
Summary of Contents for IR800G
Page 17: ...Blank Page...
Page 47: ...Blank Page...
Page 121: ...Blank Page...
Page 123: ......
Page 125: ......
Page 127: ...Blank Page...