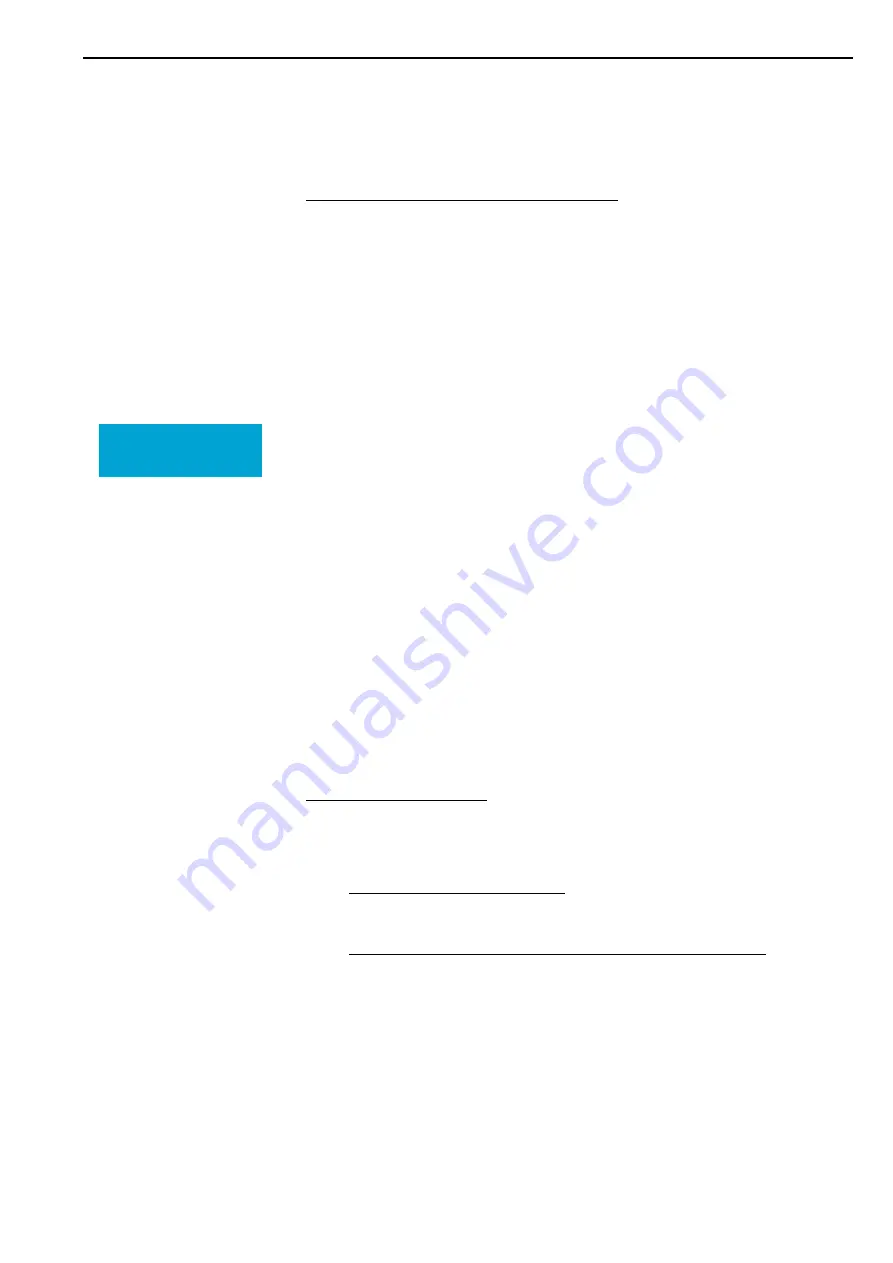
8. Setting of parameters
105204
– WTS-300-E - V4.1 - 20.01.2022
Page 87
Section 8.3
: Level “Extended cooling parameters” (P parameters)
Freezing protection by low pressure monitoring
Explanations see also section 10.8
Range
Def.
P84 Selection of sensor type
0 .. 2
0
0: Pressure detection via analogue input.
Is only active when one of the analog inputs
[A54, A56 or A57] => 2 (low pressure monitoring)
is parameterized.
1: Pressure detection via low pressure switch.
“High-active” – signal at input switches the
compressor off.
2: Pressure detection via low pressure switch.
“Low-active” – no signal at input switches the
compressor off.
NOTE: When recording pressure via the low pressure
switch, function assignment [A21..A33] => 20
(low pressure error input)
P85 has no function when using a low pressure switch!
P85 Pressure trigger limit (pressure too low)
1 .. 99,9 %
20
P87 Monitoring delay after start compressor
10 .. 999 sec.
120
P88 Switch off time compressor in case of too
low pressure
1 .. 15 min.
10
P89 Time limit after cooling start
0 .. 999 min.
0
0: no limitation
1..999: x minutes after start of the cooling, the low-pressure monitoring
switches off until the next cooling activation takes place.
Fault message compressor
Explanations see also section 10.10 and 10.11
Range
Def.
P90 Fault message low pressure
(F80)
0 .. 2
0
0: deactivated
Independent of freeze protection
1:* High-active => Signal on digital input triggers alarm
2:* Low-active => NO signal at digital input triggers alarm
In connecction with low pressure monitoring (freeze protection)
3..30 min.: If the fault message is present for longer than the time set
here after the low-pressure monitoring [P89] has ended with the compres-
sor switched on, the error (F80) is displayed..
P91 Fault message high pressure
(F81)
0 .. 2
0
0: deactivated
1*: high-active, signal at input triggers alarm
2*: low-active, no signal at the input triggers an alarm
NOTE: Observe function assignment [A21 - A28]!
* Note function assignment [A21..A33]!
NOTICE