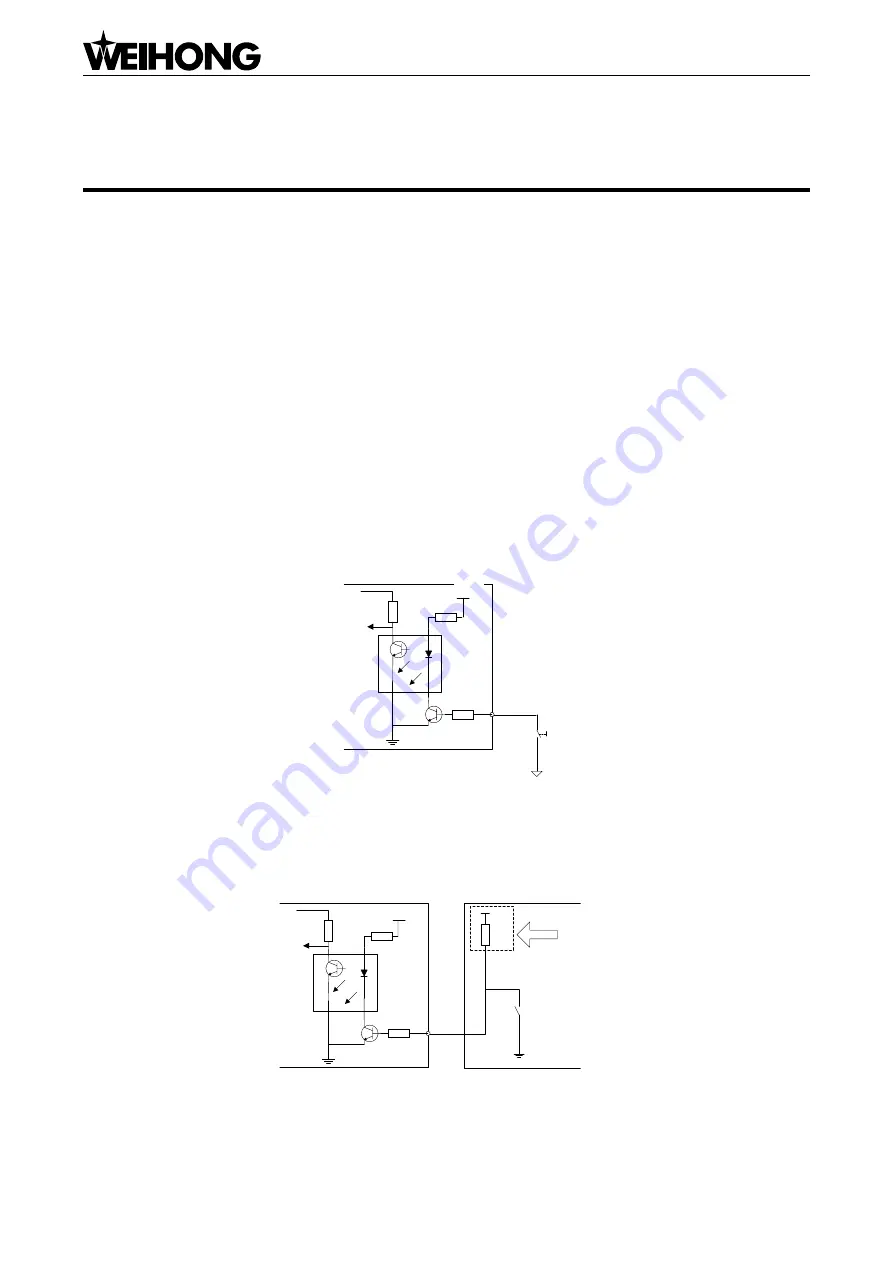
Specialized Concentrated Focused
「
14
」
Principle of System Signal
2. Principle of System Signal
The signal types of NK105G2F/G3F system can be divided into the following 4 types: binary input signal,
open collector output signal, differential output signal and analog output signal.
2.1. Binary Input Signal
Binary input signal is active low and supports NO and NC input signals (through modifying input port
polarity in the software). Conducting to GND (i.e. grounding signal) in NO connection means signal
detected, and disconnecting with GND in NC connection means signal detected.
2.1.1.
Binary Input
Connection of Binary Input and External Circuit
The wiring method between binary input signal and a mechanical switch is shown in Fig. 2-1.
GND
IN
24V
I/O Board Card
Fig. 2-1 Connection of mechanical switch and binary input
Binary input signal can be connected with a photoelectric switch or a proximity switch of NPN (NO or NC
type). Its joining method is as below.
24V
1
0
K
COM
IN
24V
I/O Board Card
External Input
Recommended
Fig. 2-2 Binary input of NPN type connecting with photoelectric switch or proximity switch