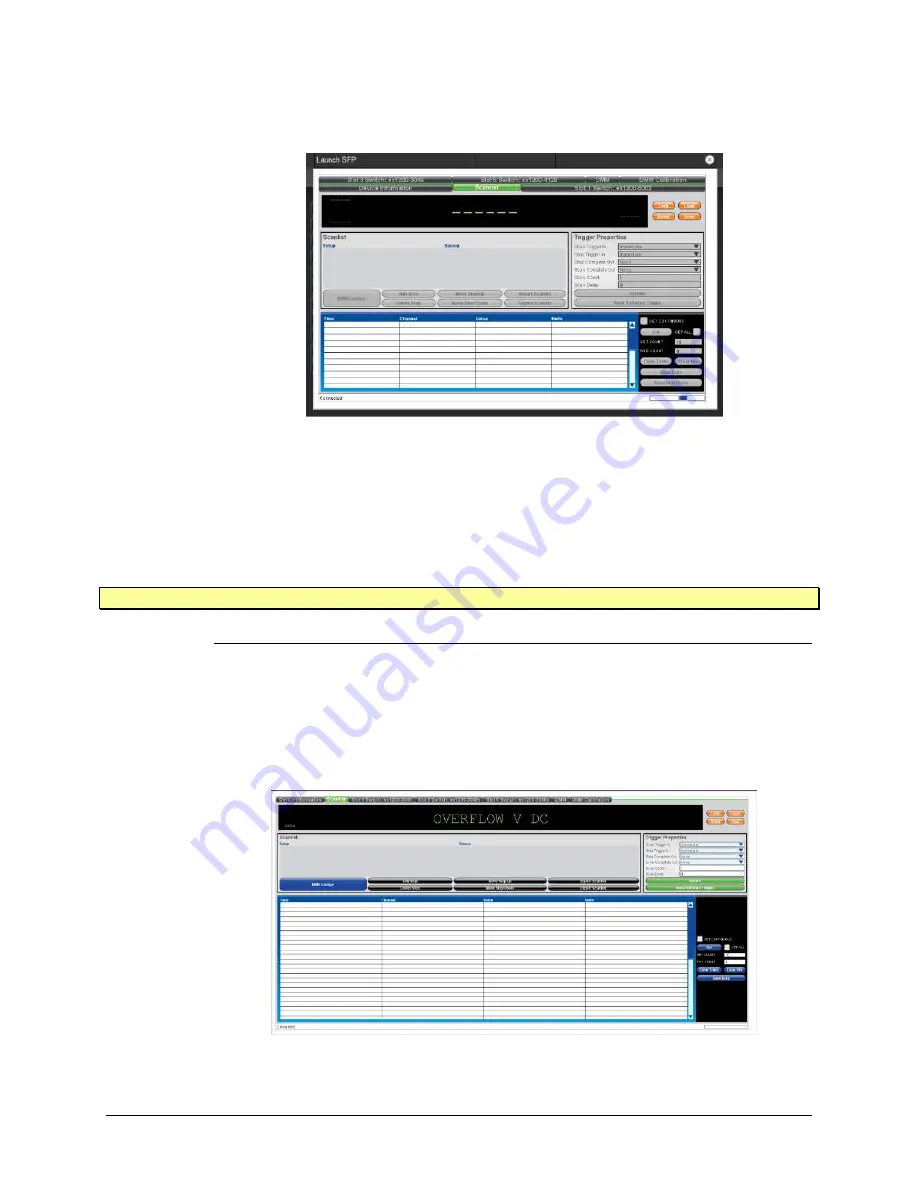
VTI Instruments Corp.
112
EX1200A Web Page Operation
Once a soft front panel is selected, a popup will appear displaying the appropriate information.
When the current SFP is no longer needed, simply click on the grey “X” in the upper right corner
to close the SFP and return to the main
Soft Front Panel
page.
F
IGURE
7-4:
SFP
P
OPUP FOR
S
CANNER
S
CANNER
S
OFT
F
RONT
P
ANEL
The EX1200A scanner allows the user to configure setup a scanlist. The
Scanlist
field allows for
the creation of a list which can be sequentially executed once the Arm and Trigger requirements
have been met. For more information on controlling the scanner programmatically, please refer to
the
VTEXScanner Programmer’s Manual
included with the EX1200A system.
NOTE
Scanner is only available when a switch card is installed in an EX1200A series mainframe.
Tab Bar
The general purpose of the
Tab
bar located at the top of the scanner SFP is to allow the user
access to all the components of the EX1200A system to which they are connected.
Device Information
: When clicked, a screen appear that provides SFP and firmware version
information for the scanner. The user is also provided information for each card that has been
installed in the EX1200A
system. This information includes the instrument’s model number
and its hardware version.
F
IGURE
7-5:
S
CANNER
S
OFT
F
RONT
P
ANEL
Summary of Contents for Ametek EX1200A Series
Page 33: ......
Page 51: ...VTI Instruments Corp 50 EX1200A Series Preparation for Use ...
Page 64: ...www vtiinstruments com EX1200A Series Preparation for Use 63 ...
Page 65: ......
Page 73: ......
Page 107: ...VTI Instruments Corp 106 EX1200A Triggering ...
Page 109: ...VTI Instruments Corp 108 EX1200A Triggering FIGURE 6 1 EX1200A SERIES TRIGGER MODEL ...
Page 143: ...VTI Instruments Corp 142 EX1200A Web Page Operation ...
Page 145: ...VTI Instruments Corp 144 EX1200A Series Programming ...
Page 155: ......
Page 161: ......