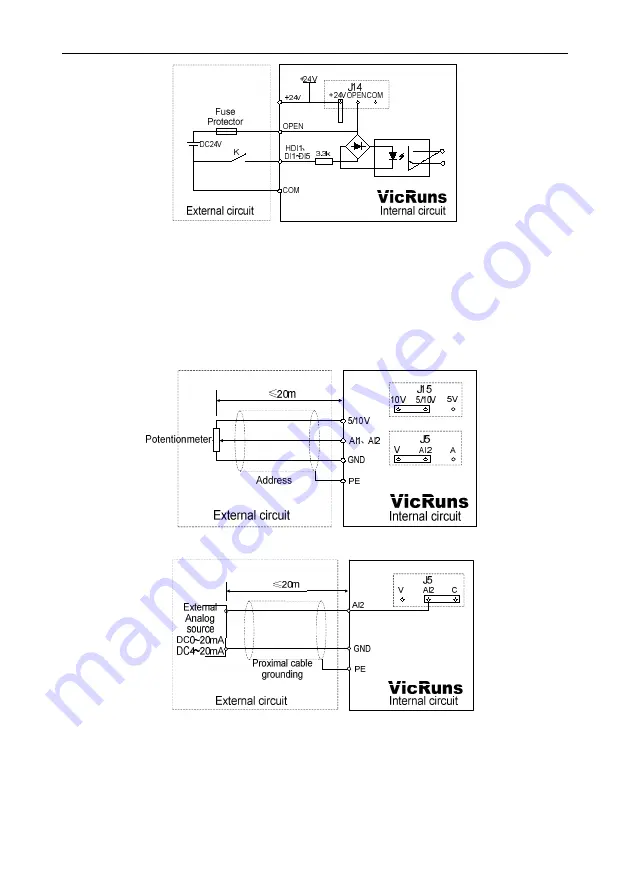
Mechanical and Electrical Installation VD560 Series Inverter User Manual
- 34 -
Fig 3.7-3 Diagram of digital input terminal with external power connection
Use external power(power must comply with UL CLASS 2 standard, a 4A fuse protector should be
added between power and port), wiring diagram as Fig 3.7-3 showed.(take note to remove the
connect wire between J14 jumper OPEN and +24V terminal)
3.7.5.2 Analog Input Terminal
Since the weak analog voltage signal is easy to suffer external interferences, it needs to use shielded
twist cable generally and the length shall be no longer than 20meters, as shown in Fig. 3.7-4, 3.7-5. In
case the analog signal is subject to severe interference, and analog signal source side shall be
installed with filter capacitor or ferrite magnetic core, as shown in Fig.3.7-6.
Fig 3.7-4 Schematic diagram of analog input terminal input voltage signal with shield twist cable
Fig 3.7-5 Schematic diagram of analog input terminal input current signal with shield twist cable