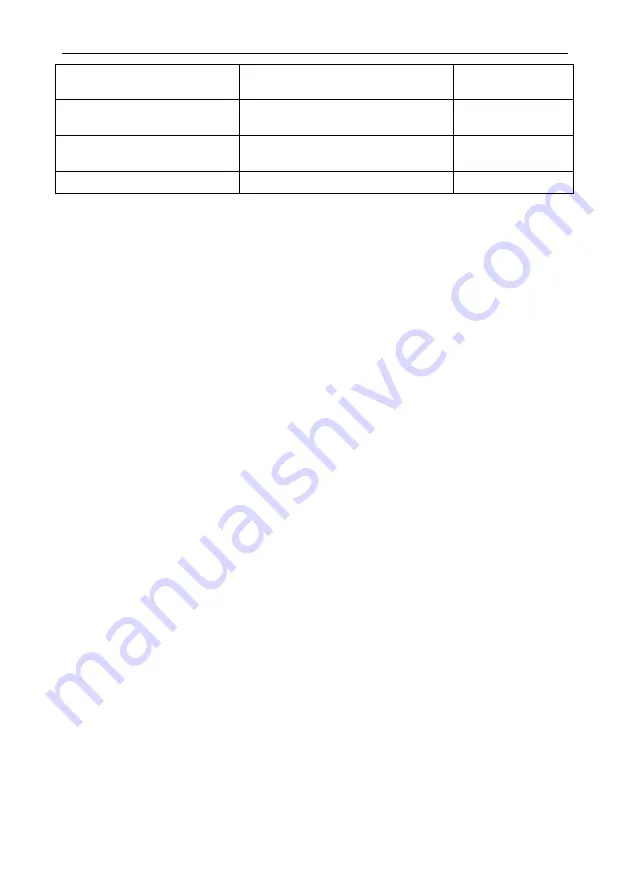
Appendix B Incremental PG Card VD560 Series Inverter User Manual
- 216 -
OA+, OA-
Frequency division difference signal
output terminal
0~300kHz
OB+, OB-
Frequency division difference signal
output terminal
0~300kHz
OA, OB
Difference open collector output
terminal
0~300kHz
COM
Output terminal
-
5. Dial switch introduction: PG card frequency division coefficient determined by dial the code switch
on the card. There are total four dial switch on PG, respectively S1, S2, S3, S4. Defined as, separate
the S1 dial switch to ON time for 2 frequency division, separate the S2 dial switch is ON for four
frequency division, separate the S3 dial switch to ON for eight frequency division, separate the S4 dial
switch to ON for 16 frequency division.
B.2 Debugging of V5GT005PG3Y0 Difference PG Card
1. Complete the wiring of main loop and other control circuit.
2. Insert the PG card to J7 scoket, because of the connector no stay prevention measures, please
ensure correct when insertion.
3. To correct the encoder line access PG card terminals. (Note: signal line is separated from the
power line layout, prohibit parallel lines, in order to avoid the encoder signal interference, do select
PG card signal lines use shielded cable, shielding layer should be grounded)
4. Ensure that all the above operations is correct, electricity to frequency converter, set parameters
FF – 01 for 1, parameters to restore the factory values. After set the the related motor parameters of
F2 group, then set F2-26 doing motor parameter self learning, set up the related parameters of
encoder of F2 group, parameters values of F2-17 for incremental encoder line number.
5. Verify the encoder installation and settings are correct of not: in F0-00 for 00 (V/F mode), operation
frequency converter, check the encoder measured frequency values, the parameter is U0-29, the
value is positive and similar with operation frequency, suggesting that the encoder installed correctly,
the parameter is set correctly. If parameter value is negative, please change the U, V, W three-phase
between any two phase is positive, if only a single motor rotation direction, also can set the
parameters for F2-20 = 1 to get the direction of the encoder feedback.
6. Set F0-00 to 02, coding meaning for motor control method for a speed sensorless vector control.
B.3 Debugging of PG Card
The line number of incremental ecoder is defined as number of calibration code disc each lap a phase,
corresponding to every rotation motor encoder pulse signal output (unit P/R namely pulse/roll). Motor
speed is defined as the number of turns per minute, such as 4 pole machine 50 Hz run-time
synchronous speed is 1500 RPM, then speed as 1500/60 = 25 RPM. So the encoder pulse signal
output per second is the 25 times of line number, such as encoder of line number is 2000 line, its
output frequency is 2000 * 25 = 50000 Hz at 50Hz running.