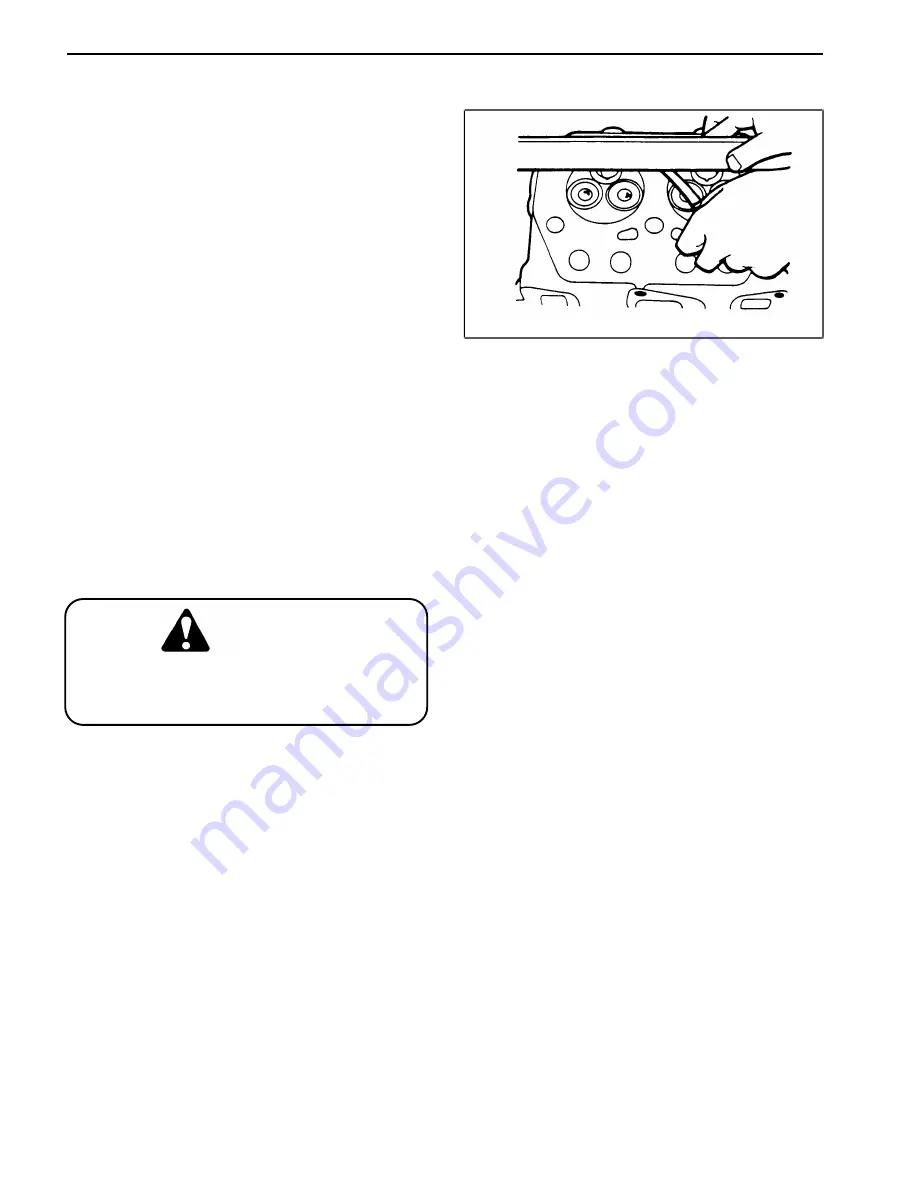
Cylinder Head Servicing (Fig. 54)
1. Use a spring compressor to compress the valve
springs. Remove the retainer locks (keepers), retainers,
and valve springs. Place each part in a holder or rack
so that they can be replaced in their original position.
2. Remove the valves and place them in position in the
rack. Examine each valve for indications of burning,
pitting, heavy carbon deposits or wear. The condition of
the valves can give important clues to other components
which may require service (example: improper valve
clearance, worn valve guides, damaged seals, etc.).
Remove the valve seals.
3. Remove all of the carbon deposits from the combus-
tion chamber using a scraper and wire brush.
4. Clean the cylinder head thoroughly with solvent or
degreasing solution and dry. Inspect it carefully for
cracks.
5. Remove all carbon deposits from the valve guide
bores with a valve guide cleaner. Use a valve guide
bristle brush to remove loosened carbon deposits in the
valve guide. Push a solvent soaked cloth through the
valve guides to remove all foreign materials.
6. Use compressed air to ensure that the oil passage
way through the head is not clogged.
Wear eye protection during use of com-
pressed air. Limit air pressure to 40 psi
(280 kPa).
7. Check the flatness of the cylinder head lower surface
using a straight edge and feeler gauge. Be sure to check
the surface variation crosswise, lengthwise, and diago-
nally. If a surface flatness variation greater than 0.002
inch (0.05 mm) exists, the cylinder head or cylinder
block must be replaced or resurfaced.
8. Use a micrometer and a small hole gauge to check
the valve guide to valve stem clearance. The valve and
valve guide should be replaced if the clearance exceeds
the following limits:
Intake Valve . . . . . . . . . . . . . . . . 0.0039 inch (0.10 mm)
Exhaust Valve . . . . . . . . . . . . . . . 0.0059 inch (0.15 mm)
Figure 54
Checking cylinder head distortion
Cylinder Head Overhaul
Page 4 - 48
Groundsmaster
®
300 Series
Summary of Contents for Groundsmaster 328-D
Page 2: ......
Page 12: ...Torque Specifications Page 2 4 Rev A Groundsmaster 300 Series ...
Page 44: ...Troubleshooting Page 4 16 Groundsmaster 300 Series ...
Page 45: ...Groundsmaster 300 Series Page 4 17 Troubleshooting ...
Page 171: ...Groundsmaster 300 Series Page 6 25 Testing ...
Page 220: ...Repairs Page 7 24 Groundsmaster 300 Series ...
Page 320: ...Troubleshooting Troubleshooting Page 11 4 Groundsmaster 300 Series ...
Page 348: ...Troubleshooting Troubleshooting Page 12 4 Groundsmaster 300 Series ...
Page 379: ...Troubleshooting Groundsmaster 300 Series Page 13 3 Troubleshooting ...
Page 400: ...This page is blank ...
Page 401: ...This page is blank ...